Aurora Circuits on Ultra-Heavy Copper PCBs
August 3, 2020 | Dan Beaulieu, D.B. Management GroupEstimated reading time: 3 minutes
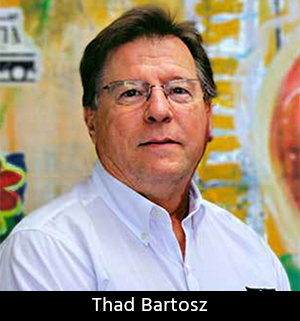
It’s always fun to talk with a company that can do something different—in this case, ultra-heavy copper PCBs, meaning over 20-ounce copper. Wanting to know more about this, I talked to Aurora Circuits Director of Business Development Thad Bartosz, who is one of our industry experts when it comes to ultra-heavy copper technology.
Dan Beaulieu: Thad, it’s good talking to you today. Let’s start with the basics. What is heavy copper?
Thad Bartosz: Heavy copper used to be defined as 4–5 ounce, but we do that for a snack. Aurora is capable of fabricating SS, NPTH, PTH, and multilayer types with up to 20-oz copper layers.
Beaulieu: What defines ultra-heavy copper?
Bartosz: Ounces of copper have been defined in ounces per square foot of area on the process panel. The thickness of the copper foil is based on 0.0014” per oz. Copper weights of 4–5 ounces are made with electrodeposited copper (ED), and ultra-heavy copper sheets are made with rolled annealed (RA) copper that must be treated to laminate to dielectrics used in fabrication.
Beaulieu: How many ounces of copper can you do at Aurora?
Bartosz: We have delivered PCBs with etched copper up to 20 ounces and would work with customers that may require any copper thickness.
Beaulieu: Why doesn’t every shop build this technology?
Bartosz: You need to have the proper equipment and process capabilities—some of these are customer or Aurora proprietary—so that you can fabricate a usable product that meets customer requirements.
Beaulieu: How did you get involved with this technology?
Bartosz: We have been building ultra-heavy copper products since 2003 when a customer asked if we could do this as they were having issues with their current source.
Beaulieu: What special equipment and processes do you have that allow you to build ultra-heavy copper boards?
Bartosz: As I mentioned earlier, these are processes that have been developed over years of sampling and production processing. We start with a sample run to establish a feasible process and then scale up for production. Etching is normally a big factor as well as machining, so you acquire equipment to properly process the PCB to make an acceptable finished product.
Beaulieu: What technology requires ultra-heavy copper?
Bartosz: Circuit boards that need high current or thermal dissipation like solar and wind power collection, aerospace/military, telecommunications, and automotive applications.
Beaulieu: What kind of end-products need it?
Bartosz: Some products include automotive junction boxes, battery management systems, and high-power circuits that have MOSFETs, IGBTs, and other high-current components, running hundreds of amps through the circuitry. For those who may not know, MOSFETs and IGBTs are a couple of power devices/components that can handle high-voltage and high-current needs. You will find them on inverters, converters, and power supplies.
Beaulieu: How do you think it will be used in the future?
Bartosz: Currently, designs have been made for power distribution, power collection, battery-powered transportation, and LED lighting. Future use will depend on new applications needed in the marketplace. You also need a supplier that changes with the market to meet these specialized needs. It will definitely be used more in the future.
Beaulieu: Is this kind of technology being designed right now?
Bartosz: Yes, it is still used in the automotive and power markets, such as new EV and autonomous vehicles where battery technology has higher current requirements and power-generation systems, solar, wind, or conventional types as their technology changes.
Beaulieu: How many ultra-heavy copper boards have you built?
Bartosz: Aurora has shipped over five million boards of single-sided, PTH, and multilayer designs over the last 10 years. Many of these were for junction boxes or battery systems in automobiles. For a few years, we shipped over 400,000 6/6 copper PCBs to China. We have processed over 800 tons (based on oz/sq ft) and over 1.7 million square feet without any EPA violations.
Beaulieu: Before we end, tell us a little bit about Aurora Circuits.
Bartosz: We have over 60 years of experience in printed circuit fabrication, providing advanced thermal management and interconnect technology solutions for PCB designs and specialty products. Product specialty areas include polymer thick-film (PTF) resistors, metal-clad materials for LED lighting and other markets, durable plating for contact areas, and, of course, ultra-heavy copper. We partner with companies to help them to maximize profitability and production sustainability.
Beaulieu: Thank you, Thad.
Bartosz: No problem, Dan.
Read more about Aurora Circuits and ultra-heavy copper PCBs here.
Suggested Items
RF PCB Design Tips and Tricks
05/08/2025 | Cherie Litson, EPTAC MIT CID/CID+There are many great books, videos, and information online about designing PCBs for RF circuits. A few of my favorite RF sources are Hans Rosenberg, Stephen Chavez, and Rick Hartley, but there are many more. These PCB design engineers have a very good perspective on what it takes to take an RF design from schematic concept to PCB layout.
Trouble in Your Tank: Causes of Plating Voids, Pre-electroless Copper
05/09/2025 | Michael Carano -- Column: Trouble in Your TankIn the business of printed circuit fabrication, yield-reducing and costly defects can easily catch even the most seasoned engineers and production personnel off guard. In this month’s column, I’ll investigate copper plating voids with their genesis in the pre-plating process steps.
Elephantech: For a Greener Tomorrow
04/16/2025 | Marcy LaRont, PCB007 MagazineNobuhiko Okamoto is the global sales and marketing manager for Elephantech Inc., a Japanese startup with a vision to make electronics more sustainable. The company is developing a metal inkjet technology that can print directly on the substrate and then give it a copper thickness by plating. In this interview, he discusses this novel technology's environmental advantages, as well as its potential benefits for the PCB manufacturing and semiconductor packaging segments.
Trouble in Your Tank: Organic Addition Agents in Electrolytic Copper Plating
04/15/2025 | Michael Carano -- Column: Trouble in Your TankThere are numerous factors at play in the science of electroplating or, as most often called, electrolytic plating. One critical element is the use of organic addition agents and their role in copper plating. The function and use of these chemical compounds will be explored in more detail.
IDTechEx Highlights Recyclable Materials for PCBs
04/10/2025 | IDTechExConventional printed circuit board (PCB) manufacturing is wasteful, harmful to the environment and energy intensive. This can be mitigated by the implementation of new recyclable materials and technologies, which have the potential to revolutionize electronics manufacturing.