iNEMI 2019 Roadmap Webinar Review: Aerospace and Defence Products
August 25, 2020 | Pete Starkey, I-Connect007Estimated reading time: 4 minutes
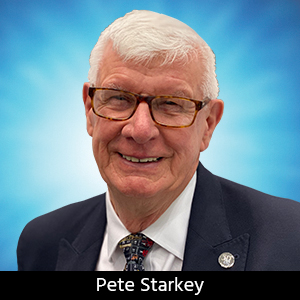
The International Electronics Manufacturing Initiative (iNEMI) is an R&D consortium of electronics manufacturers, suppliers, associations, government agencies, and universities with a mission to forecast and accelerate improvements in the electronics manufacturing industry for a sustainable future. The iNEMI Roadmap is recognised as a valuable tool for defining the state-of-the-art in the electronics industry, identifying emerging and disruptive technologies, and setting industry R&D priorities over the next 10 years.
Grace O'Malley, iNEMI’s vice president of global operations, introduced the latest in a series of webinars highlighting the roadmap’s assessments of evolving product requirements, manufacturing infrastructure issues, and technological needs and gaps. One of the seven product emulator group (PEG) chapters reported in the iNEMI 2019 Roadmap focused on anticipating the future technology needs and functionality requirements of the aerospace and defence industry segment.
Presented by Marc Carter, a prominent contributor to international electronics industry initiatives over many years and co-chair of iNEMI’s aerospace/defence PEG, the webinar underlined significant factors and key attributes characterising aerospace and defence products and differentiating them from other product sectors included in the roadmap. Primary considerations included extreme operating environments, security, reworkability, functional lifetimes, and long-duration storage requirements.
Carter remarked that the geopolitics of recent years had seen a shift back from “asymmetric warfare” to “great-power competition” with significant elements of “conflict by proxy,” and discussed its effects on the needs and available resources for development work. Because military and aerospace electronics represented only a small fraction of the world electronics industry, its market share was insufficient to drive its independent development. Product development had, therefore, become increasingly dependent on organisations not primarily engaged in military or aerospace work, and the needs of the segment had been largely supported by adaptation and ruggedisation of advanced commercial technology. Moreover, the segment relied on a complex and fragile international supply network.
Carter referred to a report from the United States Government Accountability Office, which had observed that many innovative companies were reluctant to do business with the Department of Defence (DoD) because of challenges, including defence budget uncertainties, concerns about intellectual property rights, the complexity of DoD’s processes, government-specific contract conditions, and long contracting timelines. As a result, they considered that their resources could be better spent pursuing commercial business. An additional concern was that essential skills were in short supply. Much of the technical and engineering expertise in aerospace and defence electronics was approaching retirement age and increasingly difficult to replace: “If we set out to build Saturn 5 today, we couldn’t do it!”
Against this somewhat gloomy background, Carter reviewed technology gaps and challenges, beginning with the applicability and reliability of commercial components in defence applications, for which testing was considered inadequate. Investigation of the reliability of stacked microvia constructions continued, and Carter chaired IPC’s V-TSL-MVIA working group, which was cooperating with the European Space Agency and IMEC. Product miniaturisation presented new challenges in thermal management, together with cost, readability, and form factor considerations in miniaturised displays. The availability of reliable printed circuit assemblies from trusted sources was a major supply chain security issue.
Carter made encouraging comments on the subject of improving time-to-field, which had traditionally progressed through multiple iterations of bread-boarding, prototyping, and several revisions followed by low-rate initial production. He made it clear that this iterative procedure was no longer viable in today’s fast-moving global competitive world and discussed the tremendous progress being made in simulation and modelling, which urgently needed to be integrated with design early in the process—preferably not later than the schematic stage at the ODM-OEM level.
Although the tools were not yet fully deployed, they certainly were developing, and the ultimate goal was to achieve full-circle simulation, including simulation for manufacturability that would require a tighter partnership between the ODM-OEM and the manufacturer than had previously been possible because of competition concerns. As early as possible in the process, it would be necessary to understand the effect of design choices on manufacturability at the place selected to do the actual manufacturing. He hesitated to suggest that this might promote a swing back to vertical integration but believed that such a link was essential. And the issue of design and simulation needed to be addressed by the whole supply chain.
He highlighted and briefly commented on the long list of the critical infrastructure issues identified in this chapter of the roadmap: affordability, mitigating the risks associated with lead-free products, thermal management, weight and size reduction, increases in printed circuit density and complexity, reliability and ruggedisation of commercial-off-the-shelf technologies, anti-tamper implementation, component availability, obsolete part strategies, configuration control, testability, reworkability, and component authenticity.
What were the recommendations? What directions and activities did the team suggest to mitigate the critical issues and resolve the gaps? Carter explained that a high-level team in iNEMI took recommendations from the product emulator groups and proposed projects, both to their own teams and to other organisations better positioned to action them. In his opinion, there was an urgent need for a coherent long-term consistent national technology and industrial plan. He appealed for support from the webinar audience to expand the industry-academia-government collaborative development and acquisition reform consortia that were already in place. “I would encourage you to get involved. Waiting for that mythical ‘somebody else’ to address a problem is not going to get it done! By getting involved, you get your voice heard, and you get your concerns aired.”
For more information on iNEMI’s roadmap, visit inemi.org/2019-roadmap-overview, and to get involved in future iNEMI Roadmap Working Groups, visit inemi.org/get-involved-roadmap.
Suggested Items
TT Electronics Secures £20 Million in Aerospace and Defence Contracts as European Programmes Accelerate
06/06/2025 | TT ElectronicsTT Electronics has been awarded more than £20 million in new and renewed defence contracts, marking a major step forward in its contribution to Europe’s rapidly evolving defence landscape.
I-Connect007 Editor’s Choice: Five Must-Reads for the Week
06/06/2025 | Nolan Johnson, I-Connect007Maybe you’ve noticed that I’ve been taking to social media lately to about my five must-reads of the week. It’s just another way we’re sharing our curated content with you. I pay special attention to what’s happening in our industry, and I can help you know what’s most important to read about each week. Follow me (and I-Connect007) on LinkedIn to see these and other updates.
Essemtec USA Welcomes Frank Hart as Head of Sales for North America
06/05/2025 | Essemtec USAEssemtec USA is proud to announce the appointment of Frank Hart as Head of Sales for North America, effective immediately. With over 30 years of experience in the SMT industry, Frank brings a wealth of knowledge, leadership, and a strong track record of success to our team.
AT&S Opens Europe’s First IC Substrate Plant and Competence Center in Leoben
06/04/2025 | AT&SAT&S officially inaugurated its new Competence Center for R&D and IC Substrate Production on Tuesday with a high-profile ceremony at its headquarters in Leoben-Hinterberg. Numerous high-ranking guests from politics, industry, and the media were welcomed to the event and given an exclusive tour of the 11,000-square-meter site of cutting-edge technology. With an investment of more than € 500 million,
New Era Electronics Establishes U.S. Presence with New Salt Lake City Operation
06/04/2025 | PRNewswireNew Era Electronics, a leading provider of high-performance industrial computing solutions, announces the establishment of its first United States location in Salt Lake City, Utah. This strategic expansion to the U.S. underscores New Era Electronics' commitment to enhancing supply chain continuity and delivering exceptional services across North America.