DELO Launches Liquid Pressure-sensitive Adhesives
November 5, 2020 | Delo Industrial AdhesivesEstimated reading time: 2 minutes
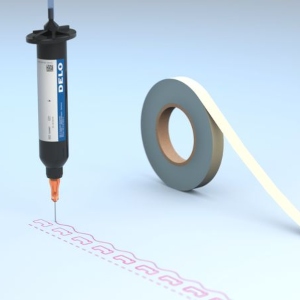
DELO has developed adhesives that have similar properties to (double-sided) adhesive tapes but are applied in liquid form. This helps users save time and costs in the production process. The liquid pressure-sensitive adhesives can be dispensed accurately and once the components have been joined, they can be further processed immediately in a fully automated process. The adhesives are particularly suitable for electronic applications such as smartphone speakers or display frames.
Adhesive tapes are used for numerous bonding applications in the electronics industry. Their advantage is the immediate adhesion after two components have been pressed together. However, adhesive tapes have two major disadvantages. The first is: When using small or complex tape geometries, automated handling becomes very time-consuming or even impossible due to the low stiffness of the carrier material and the high adhesive force. The second is that structures with a low fill factor, like those found in frame bonding, involve a large amount of waste from cutting the geometric shapes, which increases component costs.
The liquid pressure-sensitive adhesives from DELO now open up new possibilities. They are dispensed in liquid form directly onto the component and then irradiated by UV light. This creates a tacky surface, which is characteristic for tapes. Since the adhesive reaches its initial strength immediately after the second component is pressed on, the bonded assembly can be processed directly and without any fixing devices. This is a great advantage over many standard liquid adhesives.
The entire process, from precise dispensing even on tiny components or three-dimensional geometries to irradiation and mechanical pressing, can be fully automated. This makes the liquid pressure-sensitive adhesives particularly suitable for high-output production.
Depending on the requirements, users can choose liquid pressure-sensitive adhesives with different chemical bases. The acrylate-based adhesive DELO PHOTOBOND PS4130 has very similar properties to typical adhesive tape in terms of flexibility, peel resistance and strength. It is particularly suitable for adhesive applications with short cycle times and moderate requirements on final strength. Thanks to its excellent damping properties and low outgassing values, DELO PHOTOBOND PS4130 is already being used, for example, in the assembly of smartphone speakers.
The epoxy-based adhesive DELO KATIOBOND PS6372, on the other hand, was developed specifically for structural bonding applications requiring high strength. Once the initial strength has been achieved by pressing on the components, the assembly can be processed immediately, with the strength of the bonded joint increasing afterwards. When fully cured, DELO KATIOBOND PS6372 achieves compression shear strengths of over 30 MPa on aluminum and over 10 MPa on FR4. Its high resistance to temperature and media makes it also suitable for automotive applications.
Suggested Items
Statement from IPC, the Global Electronics Association, on Recent U.S. Tariffs and Global Trade
03/07/2025 | IPCIPC shared the following statement today on U.S. tariffs and their implications on the global electronics industry. This statement can be attributed to Dr. John W. Mitchell, IPC president and CEO:
CELUS Drops BOM on Electronics Design Complexity
03/05/2025 | BUSINESS WIRECELUS, developer of the leading AI-assisted electronics design platform used by developers and engineers globally, unveiled a new bill of materials (BOM) experience that better satisfies the needs of electronic engineers by helping them choose the right components for the early stages of their PCB design.
2025 IEEE Electronic Components and Technology Conference
03/04/2025 | IEEEMore than 2,000 scientists, engineers and businesspeople are expected to attend the 75th annual IEEE Electronic Components and Technology Conference (ECTC) from May 27-30, 2025 at the Gaylord Texan Resort & Convention Center here.
ASMPT at IPC APEX EXPO 2025
03/04/2025 | ASMPTASMPT, the leading provider of hardware and software for semiconductor and electronics manufacturing, will again demonstrate its technology leadership in component flexibility and software solutions at this year’s IPC APEX EXPO being held March 18-20 in Anaheim, California.
Incap’s Estonian Factory Invests in Innovative X-ray Technology
03/04/2025 | IncapThe electronics manufacturing company Incap Estonia, based in Saaremaa, has enhanced its quality control capabilities with a new high-resolution X-ray system.