-
-
News
News Highlights
- Books
Featured Books
- pcb007 Magazine
Latest Issues
Current IssueThe Hole Truth: Via Integrity in an HDI World
From the drilled hole to registration across multiple sequential lamination cycles, to the quality of your copper plating, via reliability in an HDI world is becoming an ever-greater challenge. This month we look at “The Hole Truth,” from creating the “perfect” via to how you can assure via quality and reliability, the first time, every time.
In Pursuit of Perfection: Defect Reduction
For bare PCB board fabrication, defect reduction is a critical aspect of a company's bottom line profitability. In this issue, we examine how imaging, etching, and plating processes can provide information and insight into reducing defects and increasing yields.
Voices of the Industry
We take the pulse of the PCB industry by sharing insights from leading fabricators and suppliers in this month's issue. We've gathered their thoughts on the new U.S. administration, spending, the war in Ukraine, and their most pressing needs. It’s an eye-opening and enlightening look behind the curtain.
- Articles
- Columns
- Links
- Media kit
||| MENU - pcb007 Magazine
IPS Expanding to Accommodate Growing Market
November 24, 2020 | Barry Matties, I-Connect007Estimated reading time: 2 minutes
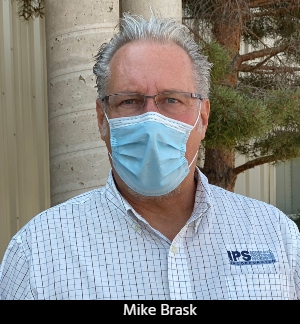
I recently had the opportunity to visit IPS in their Cedar City, Utah, facility, where Mike Brask, founder and president of IPS, shared his business strategy and gave me a tour of the expanding manufacturing facility. IPS produces a wide range of PCB manufacturing equipment, including plating, DES, VCM, VRPs, ventilation, and spare parts for older equipment.
As I toured the facility, it was easy to see there was plenty of work on the manufacturing floor. IPS now employs around 60 people and has integrated a number of automated tools in the manufacturing process. By doing this, he has optimized material usage and increased product quality.
To facilitate the evolving business plan, Mike expanded his manufacturing space with a new 17,000-square-foot addition to provide the space needed to accommodate the increased business and to carry IPS into the future. Here, I share my interview with Mike.
Barry Matties: Mike, let’s start with an overview of IPS, please.
Mike Brask: In 2008, IPS made a conscious business decision regarding what’s best for our customers in North America. Our customers want American-made machines, and when those machines need parts and service, we can respond immediately. IPS is a multi-product, multi-industry supplier within North America. IPS pushed harder to build that North American market and branch out into not just the circuit board industry but also to get into the aerospace equipment, general metal finishing, and semiconductor wet benches, where domestically, we’re getting paid U.S. wages to afford our healthcare and expenses of living in the U.S.
That business plan is what we’ve been executing since 2008. We have not only recognized the need for a Customer Service Department over the years, but we have also realized the need to develop skilled labor. I have been building up that staff to be able to support our level of manufacturing. My wife would like me to vacation more, but I love what I do, and with over 35 years of experience, I have something to offer.
The first thing was building and developing the infrastructure of key people. Now, we have five mechanical engineers doing SolidWorks and drawings, as well as four electrical engineers and two programming engineers. We have a production manager and a quality control manager. We have added more service technicians, and the whole idea is to be that company that can get the parts out and get the techs to the job site.
Last year we made the decision to add 17,000 square feet of space, so we have built up the engineering infrastructure and floor space. We have added more staff to the production and fabrication area, but the existing building is going to be all material prep. It will be cut, tack, weld, sub-assemblies, and then the new 17,000-square-foot space will be assembly, so that’s what we are doing. We have a 44,500-square-foot factory now to support our North American market. We are prepared to deliver on time, which I am very proud to say.
And then COVID-19 hit.
Read the full interview in the November 2020 issue of PCB007 Magazine.
Suggested Items
Hon Hai Education Foundation Continues to Promote Quantum Education
07/04/2025 | FoxconnHon Hai Education Foundation has long been committed to promoting forward-looking technology education in Taiwan's high schools, and held the "High School Quantum Teacher Training Camp" in Tainan City on July 1.
Incap UK Achieves JOSCAR Zero Accreditation
07/04/2025 | IncapIncap Electronics UK has been accredited under JOSCAR Zero, a new sustainability-focused extension of the defence and aerospace sector’s supplier assurance system.
Kitron Secures Contract for Components Supporting Unmanned Aerial Systems
07/04/2025 | KitronKitron has received a contract with an estimated value between EUR 4 and 8 million for the production and supply of advanced electronic components used in unmanned aerial systems (UAS).
NOTE Receives Order Worth 132 MSEK and Expands Collaboration with Customer within Security & Defense
07/04/2025 | NOTENOTE has received an order worth SEK 132 million from one of its existing customers operating within Security & Defense. NOTE thereby strengthens its long-term collaboration with the industry-leading customer.
Delta SEA Partner Event 2025 Unites Regional Partners to Embrace a “Future Ready” Vision
07/03/2025 | Delta ElectronicsDelta Electronics (Thailand) Public Company Limited, successfully hosted its Delta SEA Partner Event 2025: Future Ready at Delta Chungli Plant 5, Taiwan on June 10 – 11 , 2025.