-
-
News
News Highlights
- Books
Featured Books
- pcb007 Magazine
Latest Issues
Current IssueThe Hole Truth: Via Integrity in an HDI World
From the drilled hole to registration across multiple sequential lamination cycles, to the quality of your copper plating, via reliability in an HDI world is becoming an ever-greater challenge. This month we look at “The Hole Truth,” from creating the “perfect” via to how you can assure via quality and reliability, the first time, every time.
In Pursuit of Perfection: Defect Reduction
For bare PCB board fabrication, defect reduction is a critical aspect of a company's bottom line profitability. In this issue, we examine how imaging, etching, and plating processes can provide information and insight into reducing defects and increasing yields.
Voices of the Industry
We take the pulse of the PCB industry by sharing insights from leading fabricators and suppliers in this month's issue. We've gathered their thoughts on the new U.S. administration, spending, the war in Ukraine, and their most pressing needs. It’s an eye-opening and enlightening look behind the curtain.
- Articles
- Columns
- Links
- Media kit
||| MENU - pcb007 Magazine
Ucamco Webinar Explores Benefits of Front-End Automation Tool
December 17, 2020 | Pete Starkey, I-Connect007Estimated reading time: 2 minutes
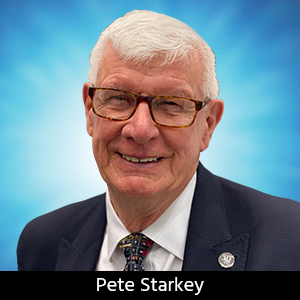
I have known the Ucamco people for over 30 years and recognise their company as an industry-leading provider of PCB CAM and pre-CAM software, as well as laser photoplotters and direct imaging systems. The team has always endeavoured to understand customer needs—often to anticipate them—and to respond with innovative solutions.
At the 2019 productronica exhibition in Munich last November, in a conversation with Ucamco managing director Karel Tavernier, I learned about a new concept in front-end software: iamcam, with “iam” standing for intelligence-aided manufacturing. Later, at this year’s IPC APEX EXPO, I had the opportunity to speak with Luc Maesen, director of Ucamco USA, and learn a little more about an automated workflow system using artificial intelligence on top of Ucamco’s automation engine to do the same for CAM as had been done for pre-CAM with Integr8tor software.
In the words of Tavernier, “The main goal is to take the drudgery out of CAM work. For standard boards, there’s no reason why the CAM process can’t be done completely automatically.” Maesen commented, “We don’t necessarily see it as a replacement of every CAM operator, but the vast majority of the work can be done by this fully-automated programme, which allows your experts to concentrate on the ones where you really need to pay attention because they have special requirements.”
When it was announced that there would be a webinar to describe the details of iamcam, I immediately signed up. The event was professionally presented by Ucamco applications engineers. Adam Newington provided the commentary, Denis Morin drove the live demonstration, and Sylvia Liemer responded to questions from the audience.
Newington introduced iamcam as a new, automated PCB front-end workflow, designed to overcome the challenges faced daily by typical PCB fabricators of tooling-up many low-added-value standard jobs with manual CAM—expensive, time-consuming, and with potentially inconsistent quality. It offers a client/server solution for off-loading routine PCB CAM data preparation, reducing front-end processing time and costs, avoiding human error, and enabling higher throughput with less manpower. He set out to explain how iamcam fitted in and how it worked.
Generally, as-received data is not good enough to go straight into production without a series of checks and setting-up operations, monotonous if performed manually. The primary purpose of iamcam is to help the PCB fabricator to automate the CAM process. In the majority of cases, the iamcam workflow-based solution takes care of all those manual operations necessary to get the job into production as quickly as possible. Combining the workflow system with a web-server allows it to work in the background as an “automation engine.”
The heart of the iamcam system is a suite of artificial intelligence (AI) algorithms that examine and analyse the data, filter out good from bad, and make assessments and judgments that enable the system to output production-ready, single-image data of the required quality. Iamcam has the proven capability to run a large percentage of jobs through the front-end in a fully automatic mode.
To read this entire article, which appeared in the December 2020 issue of PCB007 Magazine, click here.
Suggested Items
The Global Electronics Association Releases IPC-8911: First-Ever Conductive Yarn Standard for E-Textile Application
07/02/2025 | Global Electronics AssociationThe Global Electronics Association announces the release of IPC-8911, Requirements for Conductive Yarns for E-Textiles Applications. This first-of-its-kind global standard establishes a clear framework for classifying, designating, and qualifying conductive yarns—helping to address longstanding challenges in supply chain communication, product testing, and material selection within the growing e-textiles industry.
IPC-CFX, 2.0: How to Use the QPL Effectively
07/02/2025 | Chris Jorgensen, Global Electronics AssociationIn part one of this series, we discussed the new features in CFX Version 2.0 and their implications for improved inter-machine communication. But what about bringing this new functionality to the shop floor? The IPC-CFX-2591 QPL is a powerful technical resource for manufacturers seeking CFX-enabled equipment. The Qualified Product List (QPL) helps streamline equipment selection by listing models verified for CFX compliance through a robust third-party virtual qualification process.
Advancing Aerospace Excellence: Emerald’s Medford Team Earns Space Addendum Certification
06/30/2025 | Emerald TechnologiesWe’re thrilled to announce a major achievement from our Medford, Oregon facility. Andy Abrigo has officially earned her credentials as a Certified IPC Trainer (CIT) under the IPC J-STD-001 Space Addendum, the leading industry standard for space and military-grade electronics manufacturing.
Magnalytix and Foresite to Host Technical Webinar on SIR Testing and Functional Reliability
06/26/2025 | MAGNALYTIXMagnalytix, in collaboration with Foresite Inc., is pleased to announce an upcoming one-hour Webinar Workshop titled “Comparing SIR IPC B-52 to Umpire 41 Functional & SIR Test Method.” This session will be held on July 24, 2025, and is open to professionals in electronics manufacturing, reliability engineering, and process development seeking insights into new testing standards for climatic reliability.
IPC Rebrands as Global Electronics Association: Interview With Dr. John W. Mitchell
06/22/2025 | Marcy LaRont, I-Connect007Today, following a major announcement, IPC is embracing the rapid advancement of technology with a bold decision to change its name to the Global Electronics Association. This name more accurately reflects the full breadth of its work and the modern realities of electronics manufacturing. In this exclusive interview, Global Electronics Association President and CEO Dr. John W. Mitchell shares the story behind the rebrand: Why now, what it means for the industry, and how it aligns with the organization’s mission.