-
- News
- Books
Featured Books
- smt007 Magazine
Latest Issues
Current IssueWhat's Your Sweet Spot?
Are you in a niche that’s growing or shrinking? Is it time to reassess and refocus? We spotlight companies thriving by redefining or reinforcing their niche. What are their insights?
Moving Forward With Confidence
In this issue, we focus on sales and quoting, workforce training, new IPC leadership in the U.S. and Canada, the effects of tariffs, CFX standards, and much more—all designed to provide perspective as you move through the cloud bank of today's shifting economic market.
Intelligent Test and Inspection
Are you ready to explore the cutting-edge advancements shaping the electronics manufacturing industry? The May 2025 issue of SMT007 Magazine is packed with insights, innovations, and expert perspectives that you won’t want to miss.
- Articles
- Columns
- Links
- Media kit
||| MENU - smt007 Magazine
Happy’s Essential Skills: Recruiting and Interviewing
December 29, 2020 | Happy Holden, I-Connect007Estimated reading time: 2 minutes
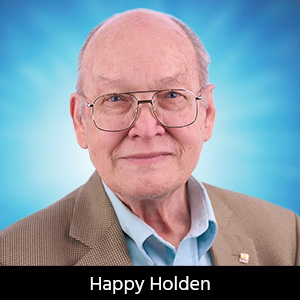
Editor’s note: This article was originally published online in 2016 and has since been updated.
Hopefully, your career has progressed to the point that you are empowered to recruit your own team or a key person for your team. There are always technical people looking for better jobs, but many times, the most talented are busy doing their work and not looking for new opportunities. If you are fortunate enough to work for a company that has established a stellar reputation, the job of recruiting becomes a lot easier. This was what I found after working a few years for Hewlett-Packard.
Recruiting
As a result of our rapid expansion and automation due to the phenomenal sales of the HP-35 scientific calculator, I was promoted to process engineering manager. I needed to recruit more printed circuit process engineers. HP had a unique method of distributing engineering resources. It was a kind of free-market method for the workforce. Management would approve 10 times as many “internal hire only,” as they would “authorized for external hire” and “relocation authorized.”
What this meant was that there was always a lot of competition for the most talented engineers in the company, as they could easily transfer to any of the open “internal hire only” jobs. If the recruiting manager pulled you into the new job, your current manager could not stop or oppose the transfer. This placed a lot of burdens on managers to properly coach, lead, and challenge their team. Any team manager who was dominating, lacked delegation skills, or always issued orders instead of letting engineers do their job was soon exposed because people transferred out, and no one wanted to transfer in. Without hiring from the outside (any good engineer would take any job just to get in), the lack of personnel became apparent.
Printed circuit manufacturing was not one of the jobs that electrical engineers in HP wanted to do. EEs were also not the best choice for printed circuit manufacturing because chemical engineers, chemists, and mechanical engineers had more skills useful to support the PCB manufacturing process. Therefore, I was authorized to recruit external hires. I was part of the college recruiting team, as 90% of HP engineers were recruited from universities (BS, MS, or Ph.D.). HP’s process for college recruiting was based on an early form of networking. HP maintained close contact with department heads and head professors of engineering departments at favored universities.
To recruit chemical engineers, we went to those universities noted for their focus on industries like electronics, process control, and environmental. I contacted the department heads for chemical engineering at five noted universities, including my alma mater. We asked professors to give us the names of their most talented graduating students that would likely be interested in a career in electronics. We contacted the students and scheduled appointments to interview them at a time convenient for them rather than the fixed slots at the engineering placement office. Most chemical engineers were not looking for careers in electronics, but rather in petroleum, chemicals, pulp and paper, or energy.
To read this entire article, which appeared in the December 2020 issue of SMT007 Magazine, click here.
Suggested Items
SMT007 Magazine July—What’s Your Competitive Sweet Spot?
07/01/2025 | I-Connect007 Editorial TeamAre you in a niche that’s growing or shrinking? Is it time to reassess and refocus? We spotlight companies thriving by redefining or reinforcing their niche—what are their insights? In the July 2025 issue of SMT007 Magazine, we spotlight companies thriving by redefining or reinforcing their niche and offer insights to help you evaluate your own.
Smarter Machines Use AOI to Transform PCB Inspections
06/30/2025 | Marcy LaRont, PCB007 MagazineAs automated optical inspection (AOI) evolves from traditional end-of-process inspections to proactive, in-line solutions, the integration of AI and machine learning is revolutionizing defect reduction and enhancing yields, marking a pivotal shift in how quality is managed in manufacturing.
Magnalytix and Foresite to Host Technical Webinar on SIR Testing and Functional Reliability
06/26/2025 | MAGNALYTIXMagnalytix, in collaboration with Foresite Inc., is pleased to announce an upcoming one-hour Webinar Workshop titled “Comparing SIR IPC B-52 to Umpire 41 Functional & SIR Test Method.” This session will be held on July 24, 2025, and is open to professionals in electronics manufacturing, reliability engineering, and process development seeking insights into new testing standards for climatic reliability.
The Death of the Microsection
06/26/2025 | Bob Neves, Reliability Assessment Solutions, Inc.I got my start out of college grinding and polishing PCB microsections. My thumbs are a bit arthritic today because of the experience (microsection grinders know what I mean). Back then, via structures were rather large, and getting to the center in six steps of grinding and polishing was easy compared to what my team has been doing recently at the lab.
Specially Developed for Laser Plastic Welding from LPKF
06/25/2025 | LPKFLPKF introduces TherMoPro, a thermographic analysis system specifically developed for laser plastic welding that transforms thermal data into concrete actionable insights. Through automated capture, evaluation, and interpretation of surface temperature patterns immediately after welding, the system provides unprecedented process transparency that correlates with product joining quality and long-term product stability.