-
- News
- Books
Featured Books
- smt007 Magazine
Latest Issues
Current IssueWhat's Your Sweet Spot?
Are you in a niche that’s growing or shrinking? Is it time to reassess and refocus? We spotlight companies thriving by redefining or reinforcing their niche. What are their insights?
Moving Forward With Confidence
In this issue, we focus on sales and quoting, workforce training, new IPC leadership in the U.S. and Canada, the effects of tariffs, CFX standards, and much more—all designed to provide perspective as you move through the cloud bank of today's shifting economic market.
Intelligent Test and Inspection
Are you ready to explore the cutting-edge advancements shaping the electronics manufacturing industry? The May 2025 issue of SMT007 Magazine is packed with insights, innovations, and expert perspectives that you won’t want to miss.
- Articles
- Columns
- Links
- Media kit
||| MENU - smt007 Magazine
A New Captive PCB Facility in the U.S.
April 19, 2021 | I-Connect007 Editorial TeamEstimated reading time: 2 minutes
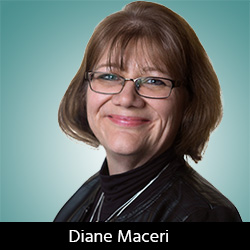
Diane Maceri and Jessi Hall discuss how Schweitzer Engineering Laboratories (SEL) has been working with Alex Stepinski of GreenSource Fabrication to build their own captive PCB facility in Moscow, Idaho; the thought process behind that decision; and their involvement in the Managers Forum at IPC APEX EXPO 2021.
Barry Matties: Diane, can you give us an overview of the decision process to build a new captive PCB factory?
Diane Maceri: We produce a high volume of PCBs, they’re lower complexity, and we have great supplier partners, but we have to take into consideration that they’re buying equipment and working toward manufacturing more complex PCBs. There’s always that tension between the capacity we need, and the complex needs of making a higher profit margin.
Because of this, and because we’re always growing, we looked at whether we wanted to bring on another supplier partner to expand. Do we want to buy an existing PCB factory, or do we want to build our own? We weighed those pros and cons. Through a lot of work over the past two years, we concluded that we wanted to build our own factory. We met Alex [Stepinski of GreenSource Fabrication] and mapped out a path that looked very interesting to us as far as the facility not having waste and that kind of thing.
Matties: Alex really focuses an automated process. Is that what you moved toward as well—a fully automated process?
Jessi Hall: Our primary concern is the flow through the factory so, yes, I would say it’s pretty automated, although not fully automated. There are some things where we don’t feel the technology is quite ready and we want to ensure that we have a reliable product—that’s very important for our industry. We decided to pursue automation for the things that make sense now, make sure we have space for future automation, and then we can invest in new technologies depending on where our designs go.
Matties: From a supply chain point of view, this must have been just a breath of fresh air. Now everything is under your control, even your timeline. What advantages do you expect to have from a supply chain perspective?
Maceri: It will ensure that our demand is covered, because we have a large volume of PCBs that we use every day. Another thing that’s interesting about SEL is that we have a five-day lead time from the time we get an order from a customer until we’re shipping it. Not that we don’t have great partners, but this will ensure—since we have such a short lead time—we can tie that PCB demand straight into our assembly and out the door. It’s bringing the whole process closer.
Matties: I would think that the cost of the circuit board itself has gone down a certain percentage. What savings, on a percentage basis, do you think you’ll gain here?
Maceri: We don’t know exactly. We have multiple different layer counts and so, at the lower layer counts, we’re looking at a much higher percentage, but we don’t know exactly what that would be. As you go up in layers, the percentage comes down a little bit.
To read this entire interview, which appeared in the April 2021 issue of SMT007 Magazine, click here.
Suggested Items
The Global Electronics Association Releases IPC-8911: First-Ever Conductive Yarn Standard for E-Textile Application
07/02/2025 | Global Electronics AssociationThe Global Electronics Association announces the release of IPC-8911, Requirements for Conductive Yarns for E-Textiles Applications. This first-of-its-kind global standard establishes a clear framework for classifying, designating, and qualifying conductive yarns—helping to address longstanding challenges in supply chain communication, product testing, and material selection within the growing e-textiles industry.
IPC-CFX, 2.0: How to Use the QPL Effectively
07/02/2025 | Chris Jorgensen, Global Electronics AssociationIn part one of this series, we discussed the new features in CFX Version 2.0 and their implications for improved inter-machine communication. But what about bringing this new functionality to the shop floor? The IPC-CFX-2591 QPL is a powerful technical resource for manufacturers seeking CFX-enabled equipment. The Qualified Product List (QPL) helps streamline equipment selection by listing models verified for CFX compliance through a robust third-party virtual qualification process.
Advancing Aerospace Excellence: Emerald’s Medford Team Earns Space Addendum Certification
06/30/2025 | Emerald TechnologiesWe’re thrilled to announce a major achievement from our Medford, Oregon facility. Andy Abrigo has officially earned her credentials as a Certified IPC Trainer (CIT) under the IPC J-STD-001 Space Addendum, the leading industry standard for space and military-grade electronics manufacturing.
Magnalytix and Foresite to Host Technical Webinar on SIR Testing and Functional Reliability
06/26/2025 | MAGNALYTIXMagnalytix, in collaboration with Foresite Inc., is pleased to announce an upcoming one-hour Webinar Workshop titled “Comparing SIR IPC B-52 to Umpire 41 Functional & SIR Test Method.” This session will be held on July 24, 2025, and is open to professionals in electronics manufacturing, reliability engineering, and process development seeking insights into new testing standards for climatic reliability.
IPC Rebrands as Global Electronics Association: Interview With Dr. John W. Mitchell
06/22/2025 | Marcy LaRont, I-Connect007Today, following a major announcement, IPC is embracing the rapid advancement of technology with a bold decision to change its name to the Global Electronics Association. This name more accurately reflects the full breadth of its work and the modern realities of electronics manufacturing. In this exclusive interview, Global Electronics Association President and CEO Dr. John W. Mitchell shares the story behind the rebrand: Why now, what it means for the industry, and how it aligns with the organization’s mission.