-
- News
- Books
Featured Books
- smt007 Magazine
Latest Issues
Current IssueWhat's Your Sweet Spot?
Are you in a niche that’s growing or shrinking? Is it time to reassess and refocus? We spotlight companies thriving by redefining or reinforcing their niche. What are their insights?
Moving Forward With Confidence
In this issue, we focus on sales and quoting, workforce training, new IPC leadership in the U.S. and Canada, the effects of tariffs, CFX standards, and much more—all designed to provide perspective as you move through the cloud bank of today's shifting economic market.
Intelligent Test and Inspection
Are you ready to explore the cutting-edge advancements shaping the electronics manufacturing industry? The May 2025 issue of SMT007 Magazine is packed with insights, innovations, and expert perspectives that you won’t want to miss.
- Articles
- Columns
- Links
- Media kit
||| MENU - smt007 Magazine
Hans-Peter Tranitz: Dieter Bergman IPC Fellowship Award Recipient
April 22, 2021 | Patty Goldman, I-Connect007Estimated reading time: 3 minutes
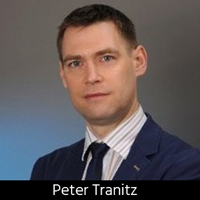
From the IPC website: The Dieter Bergman IPC Fellowship Award is given to individuals who have fostered a collaborative spirit, made significant contributions to standards development, and have consistently demonstrated a commitment to global standardization efforts and the electronics industry. Each recipient will be eligible to bestow the Dieter Bergman Memorial Scholarship upon the university or college of his/her choice.
Patty Goldman speaks with Continental Automotive’s Peter Tranitz about his IPC involvement with press-fit and other automotive standards which have earned him the coveted Dieter Bergman IPC Fellowship Award.
Patty Goldman: Peter, congratulations on this award. It’s quite an honor as you’re aware, and it means you have done a lot of work with IPC and standards development. Perhaps you can tell us a little bit about yourself and your involvement with IPC and the different committees.
Hans-Peter Tranitz: Hello, Patty. I’m working for Continental Automotive GmbH. My home location is Regensburg, and my profession is being an expert for mechanical joining technologies for metals and plastics in automotive final assembly, such as press fit and all kinds of technologies dealing with laser and material interaction. Welding, riveting and screwdriving are also within my and my team’s responsibility.
My first contact with IPC was in 2010 when I joined for the first time a tin whisker conference in Schaumburg, Illinois, near Chicago, and there I made a presentation about my current risk issues and how I deal with that. At that time, I felt that the people who joined the meeting were all “dinosaurs” that knew everything about whiskers and then here comes a freshman—even if I was already quite long in the industry at that time.
But, for them, I was a freshman, and I saw this very little smile in their faces when I was presenting. And I felt like, “Oh, they all know what I’m talking about. I don’t tell them anything new.” But when I arrived at the APEX EXPO one year later all of them recognized me and all of them talked to me. And there was a very, very open-minded communication and I felt really accepted right away. That is something which is quite unique and that is what I would consider the special environment that IPC has. I was impressed by its open-minded and warm welcome of new members and new arrivals.
Goldman: Yes, IPC and volunteers love new volunteers. Worker bees, as we call them.
Tranitz: Agreed. After that time, a few years later, I proposed to IPC to start a press-fit standard for the automotive industry and high reliability applications because the current standards that existed were basically coming from the former telecommunications industry. So simply, cold-joining technology is where a compliant zone of a connector or housing pin is pressed-in to a specific plated through-hole of a printed board. This joint can withstand very tough environmental conditions beyond those usually known for solder joints as long as the overall design is matching. And particularly from the reliability perspective, this is what we needed more in the automotive industry, and that’s why we made this proposal.
A year later my other co-chair, Udo Welzel, and myself got the request from IPC to write a PIN (project initiation request). From this moment onward, we were a very productive working team. After three years we were already in the ballot phase, and in May 2020 finally the standard has been published. I think we have been quite fast considering we started the standard absolutely from scratch.
To read this entire interview, which appeared in the 2021 issue of Show & Tell Magazine, click here.
Suggested Items
Driving Innovation: Direct Imaging vs. Conventional Exposure
07/01/2025 | Simon Khesin -- Column: Driving InnovationMy first camera used Kodak film. I even experimented with developing photos in the bathroom, though I usually dropped the film off at a Kodak center and received the prints two weeks later, only to discover that some images were out of focus or poorly framed. Today, every smartphone contains a high-quality camera capable of producing stunning images instantly.
Hands-On Demos Now Available for Apollo Seiko’s EF and AF Selective Soldering Lines
06/30/2025 | Apollo SeikoApollo Seiko, a leading innovator in soldering technology, is excited to spotlight its expanded lineup of EF and AF Series Selective Soldering Systems, now available for live demonstrations in its newly dedicated demo room.
Indium Corporation Expert to Present on Automotive and Industrial Solder Bonding Solutions at Global Electronics Association Workshop
06/26/2025 | IndiumIndium Corporation Principal Engineer, Advanced Materials, Andy Mackie, Ph.D., MSc, will deliver a technical presentation on innovative solder bonding solutions for automotive and industrial applications at the Global Electronics A
Fresh PCB Concepts: Assembly Challenges with Micro Components and Standard Solder Mask Practices
06/26/2025 | Team NCAB -- Column: Fresh PCB ConceptsMicro components have redefined what is possible in PCB design. With package sizes like 01005 and 0201 becoming more common in high-density layouts, designers are now expected to pack more performance into smaller spaces than ever before. While these advancements support miniaturization and functionality, they introduce new assembly challenges, particularly with traditional solder mask and legend application processes.
Knocking Down the Bone Pile: Tin Whisker Mitigation in Aerospace Applications, Part 3
06/25/2025 | Nash Bell -- Column: Knocking Down the Bone PileTin whiskers are slender, hair-like metallic growths that can develop on the surface of tin-plated electronic components. Typically measuring a few micrometers in diameter and growing several millimeters in length, they form through an electrochemical process influenced by environmental factors such as temperature variations, mechanical or compressive stress, and the aging of solder alloys.