-
- News
- Books
Featured Books
- smt007 Magazine
Latest Issues
Current IssueWhat's Your Sweet Spot?
Are you in a niche that’s growing or shrinking? Is it time to reassess and refocus? We spotlight companies thriving by redefining or reinforcing their niche. What are their insights?
Moving Forward With Confidence
In this issue, we focus on sales and quoting, workforce training, new IPC leadership in the U.S. and Canada, the effects of tariffs, CFX standards, and much more—all designed to provide perspective as you move through the cloud bank of today's shifting economic market.
Intelligent Test and Inspection
Are you ready to explore the cutting-edge advancements shaping the electronics manufacturing industry? The May 2025 issue of SMT007 Magazine is packed with insights, innovations, and expert perspectives that you won’t want to miss.
- Articles
- Columns
- Links
- Media kit
||| MENU - smt007 Magazine
Excerpt: The Printed Circuit Assembler’s Guide to… Smart Data, Chapter 3
May 5, 2021 | Sagi Reuven and Zac Elliott, Siemens Digital Industries SoftwareEstimated reading time: 3 minutes
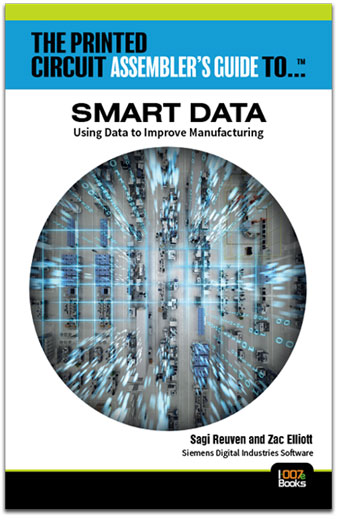
Chapter 3: Putting Data to Work in the Factory to Improve Business
There are many different and valid perspectives on the performance of a factory. For instance, the fact that the factory is on shutdown may be significant to a planner who is concerned with overall factory capacity. However, the shutdown is less significant to the production manager, who simply wants to know if the machines will run efficiently when they are scheduled to run.
With a mix of different customers, products, factories, lines, and machines, hundreds of different KPIs may need to be considered. Some of these measurements can be complex, requiring data from multiple processes—for example, overall equipment effectiveness (OEE) calculations in which the performance of the factory resources are considered as well as the quality of the end products.
With all of this complexity, a bottleneck is often caused by some external force that is not being measured. A machine may not be operating because of an actual malfunction in the equipment, or it may be waiting for some upstream or downstream process. Perhaps the operator is on break, or there is a shortage of materials causing the downtime. To identify the root cause of a problem and provide for an actionable response, these external forces must be considered.
The Opcenter Intelligence Electronics application addresses this need, considering information coming from the enterprise and processes. Process-specific applications provide performance data about the status of equipment. Site-based constraints can be used to qualify any process status based on constraints such as the overall factory schedule, material availability, or the upstream/downstream bottleneck.
With information about process performance and the external constraints influencing production, many optimization opportunities are possible using an intelligent application. The process-specific layer would be able to optimize based on external knowledge from other processes and higher-level applications, while the site-application layer would benefit from detailed process information from each individual equipment.
Feedback
A prime example of applying these layers in a smart factory is in closed-loop feedback. In this scenario, measurements taken at one process are used to adjust the operation of another process automatically to maintain a consistent result. For example, the SMT machine could adjust placements based on drift data measured at the AOI.
A site-level analysis application collects the placement and material information from the SMT machine through the process-specific application managing that equipment. Next, the real-time measurement results coming from the AOI are collected and analyzed to identify a process-control problem. The results of this statistical analysis are fed back to the SMT machine so that adjustments and compensations can be made as appropriate for the equipment.
Because a normalized interface is used at the AOI and the SMT machine, this application functions across varying platforms while allowing each individual equipment to take the optimal action for its technology.
Finite Planning
Finite planning of the SMT schedule can be significantly improved and optimized through automation and computerization. In the typical situation, the ERP system manages the customer demand and material requirements in coarse granularity with little detail of the resources used in manufacturing. Once the work order demand is generated in the ERP system, diligent work is put into developing a production plan to satisfy the orders.
Complicated spreadsheets and workbooks are used to model the manufacturing flow and to manage constraints that are external to the ERP system. Unexpected changes in customer demand or the manufacturing constraints are difficult to integrate into the existing plan. Optimization of product groupings infrequently happens outside of the day-to-day planning activity.
To download this free eBook, published by I-Connect007, click here.
To view the entire I-Connect007 eBook library, click here.
Other related content
I-007e Micro Webinar: Implementing "Digital Twin" Best Practices From Design Through Manufacturing
Real Time with... I-Connect007 Roundtable: Siemens and Computrol: Achieving Operational Excellence in Electronics Manufacturing
I-Connect007 Column: Lean Digital Thread, from Sagi Reuven, Siemens Digital Industries Software