Increasing Productivity Through Training
June 4, 2021 | Jahr Turchan, Blackfox Training InstituteEstimated reading time: 2 minutes
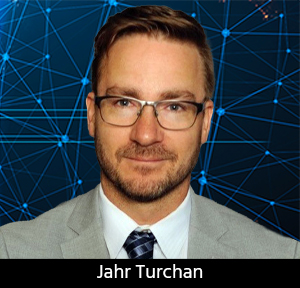
When I think of a manufacturing organization, I think of a “well-oiled machine”—a complex system of unique parts that work together to create something wonderful. This is a funny comparison to me, though, as most times actual machines are being employed to produce or assemble components at some point in the manufacturing process. While this “machine” consists of many working parts—such as systems, materials, actual machines, processes, and procedures—undeniably the most important component is the workforce. Our employees are also where we have the largest opportunity to have a substantial impact on the manufacturing process as we work toward excellence in operational management. Here, I will share feedback from training our clients and students as well as some training best practices.
One might think that such a substantial impact would require massive amounts of resources such as money and time (of which we all wish we had more), but that is not the case. Repeatedly, research has shown that productivity will increase when proper training is made available to the manufacturing workforce. We know that employees who gain new skills become more confident, get stimulated and engaged, and are more satisfied with their employment. It can also help to revive old skills not practiced in a while. This concept of improved productivity has been studied and proven time and time again. In a study conducted by the National Center on the Educational Quality of the Workforce in over 3,100 U.S. workplaces, they showed that on average if there was an increase by 10% in workforce education, an 8.6% increase in productivity would follow.[1]
Too often when we think of training our manufacturing workforce, we focus on the shop floor. We look for opportunities mainly with those who are doing the making. We need to cast a wider gaze as the manufacturing process is not limited to the manufacturing floor. Quality, engineering, sales and marketing, logistics, and even accounting/finance are all part of the process that starts with a business plan and culminates with your trinket in the hands of your happy customer. All departments make up that “well-oiled machine.”
Training members from one department about the processes and skills required in another department will help those units to work together better. This also leads to an increase in understanding, empathy, and respect between departments. For example, when the quality engineer inspects parts and finds defects, they are more likely to care about why the part is defective and what part of the process failed. This is invaluable, especially when activities such as root cause analysis are required to determine failure modes. They are also less likely to just stamp “REJECT” on the part and kick it back over to manufacturing to deal with. With increased communication comes increased quality. In another example, when your salespeople have a keen understanding of your manufacturing processes, they are more likely to have effective sales interactions, like knowing when a certain opportunity fits perfectly into your niche, or when to walk away and not waste the time of the engineering department.
To read this entire article, which appeared in the May 2021 issue of PCB007 Magazine, click here.