-
- News
- Books
Featured Books
- smt007 Magazine
Latest Issues
Current IssueSupply Chain Strategies
A successful brand is built on strong customer relationships—anchored by a well-orchestrated supply chain at its core. This month, we look at how managing your supply chain directly influences customer perception.
What's Your Sweet Spot?
Are you in a niche that’s growing or shrinking? Is it time to reassess and refocus? We spotlight companies thriving by redefining or reinforcing their niche. What are their insights?
Moving Forward With Confidence
In this issue, we focus on sales and quoting, workforce training, new IPC leadership in the U.S. and Canada, the effects of tariffs, CFX standards, and much more—all designed to provide perspective as you move through the cloud bank of today's shifting economic market.
- Articles
- Columns
- Links
- Media kit
||| MENU - smt007 Magazine
Estimated reading time: 4 minutes
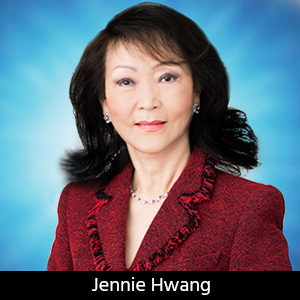
SMT Perspectives and Prospects: Digital Manufacturing—Just-in-Case or Just-in-Time
As the semiconductor chip shortage around the world shows no signs of abating in the imminent future, I was drawn to this headline: “How Toyota Dodged the Chip Shortage” from Bloomberg Businessweek on April 12. It reported the ways and means that led to Toyota’s success in weathering the supply chain disruptions. While its rivals are missing the product delivery, the company’s past experiences that prompted implementation of its contingency plan have helped it mitigate the impact of today’s global chip shortage on the production and delivery of cars in the global marketplace. Vividly, this is a timely business case as well as a use case to ponder.
Under today’s dynamic global-macro environment and the emerging digital manufacturing platforms, what will or should change?
Regardless of whether the global chip shortage is a result of pandemic or from unanticipated market supply-demand imbalance, it is warranted to deliberate on solutions to eschew recurring events in the manufacturing sector. One plausible question to ask is, “What are the lessons learned from the success of Toyota’s ability to keep its plants humming as other automakers shutter plants?” First, there is value in truly learning from the lesson by effectively taking actions. Toyota’s past encounter during the 2011 earthquake-triggered tsunami that wreaked havoc on its production capabilities (including the supply chain disruptions) has brought out its actions in scrupulously examining its supply chain. The company learned the lesson by acting. This time around, the company has benefited tremendously by previous astute actions in implementing a comprehensive system throughout its supply chain.
In deciphering the supply chain strategy and tactics[1], in broad strokes, it boils down to six key words: visibility, predictivity, identifying, monitoring, communicating, and balancing. These are positioned in the to-do list calling for planning and actions to dodge future supply chain challenges.
Visibility: A crucial question to address is the level of visibility throughout the supply chain. In the intricate supply chain network, knowing the direct suppliers is the starting point, not the end point, to acquire an adequate visibility of the supply chain. Understanding and knowing the second-, third- or even fourth-tier suppliers is also a part of the equation of supply chain management to gain adequate visibility and transparency.
Predictivity: It is not hard to look back to make conclusions, but it is dauntingly demanding to predict the future accurately. However, in supply chain management, what level of predictability is required is a necessary-evil question to tackle. The better the visibility, the more thorough planning, the higher level of predictability can be achieved.
Identifying: To identify a list of key parts for an end-use product is easier said than done; it takes knowledge and effort to make a “right” list. In the Toyota case, the automaker came up with a list of about 1,500 parts it deemed to be necessary to secure alternatives for or to stockpile.
Monitoring: Set a monitoring system in motion that gauges the network of suppliers that produce those key parts to ensure planned delivery from the chain of suppliers—another deliberate and elaborate effort. In tasking, one important question to ask is, “What is the technology employed to monitor the chain of supply?” Timely adopting of evolving technology, to leverage the capabilities of a digital tool to facilitate data acquisition and the flow of digital information in supply chain, is key to an agile operation.
Communicating: The following all play an essential role in the integrity of a supply chain: Effective and efficient communication between the OEM and Tier 1 suppliers; the data flow between the OEM and the Tier 1 suppliers; communication between the Tier 1 suppliers and their network to include Tiers 2, 3, 4; and the feed-back loop.
Balancing: To a manufacturer in producing and delivering a given product, inventory management is just as important as supply chain management because the inventory directly impacts the bottom line of a business. Reducing and minimizing the inventory of a part/component of a given product is an ongoing effort. Questions to address are:
-
Do all strategic raw materials (with sound justification) have alternate source(s)?
-
Do all mission-critical components have alternate source(s)?
-
Which parts/components call for stockpile? For those stockpiled parts/components, what is the “days in inventory” and what is the “dollar inventory” that can be justified?
Synchronizing with the holistic manufacturing strategy, be it supplied locally or globally, the goal is to reach an optimal level of inventory. It is an intricate balancing act to achieve both a secure supply chain and an optimal inventory management, which requires knowledge, know-how, and effort.
Just-in-Time or Just-in-Case
As the global landscape continues to change, the future remains the most precious commodity. Charles F. Kettering, a famed American inventor, and the founder of Delco of General Motors, conveyed it well:
“My interest is in the future, because I am going to spend the rest of my life there.”
Looking at the future, the manufacturing infrastructure is becoming more intricate; the swift and timely delivery of products to end-users (customers) is paramount to a viable business.
Going forward, under the dynamic global-macro factors and the burgeoning digital manufacturing platforms, the construct that is solely based on just-in-time inventory management as a stand-alone practice could be proven inadequate. Considering both just-in-time and just-in-case appear to be a pragmatic model to operate in the digitized enterprise; perhaps it is a “comforting” approach as well.
It is hoped that this article will spark deeper and wider thoughts and actions about the future supply chain enterprise and its role to business viability, competitiveness, and ultimately the prosperity.
Reference
-
“Rethinking Manufacturing—Bracing and Embracing Post-Pandemic Decade,” by Dr. Jennie S. Hwang, SMT007 Magazine, pp. 10–16, July 2020.
This column originally appeared in the July 2021 issue of SMT007 Magazine.
More Columns from SMT Perspectives and Prospects
SMT Perspectives and Prospects: Warren Buffett’s Perpetual Wisdom, Part 2SMT Perspectives and Prospects: Warren Buffett’s Perpetual Wisdom, Part 1
SMT Perspectives and Prospects: Artificial Intelligence, Part 5: Brain, Mind, Intelligence
SMT Perspectives and Prospects: Artificial Intelligence, Part 4—Prompt Engineering
SMT Perspectives and Prospects: The AI Era, Part 3: LLMs, SLMs, and Foundation Models
SMT Perspectives and Prospects: A Dose of Wisdom
SMT Prospects and Perspectives: AI Opportunities, Challenges, and Possibilities, Part 1
SMT Perspectives and Prospects: Critical Materials—A Compelling Case, Part 3