-
- News
- Books
Featured Books
- smt007 Magazine
Latest Issues
Current IssueWhat's Your Sweet Spot?
Are you in a niche that’s growing or shrinking? Is it time to reassess and refocus? We spotlight companies thriving by redefining or reinforcing their niche. What are their insights?
Moving Forward With Confidence
In this issue, we focus on sales and quoting, workforce training, new IPC leadership in the U.S. and Canada, the effects of tariffs, CFX standards, and much more—all designed to provide perspective as you move through the cloud bank of today's shifting economic market.
Intelligent Test and Inspection
Are you ready to explore the cutting-edge advancements shaping the electronics manufacturing industry? The May 2025 issue of SMT007 Magazine is packed with insights, innovations, and expert perspectives that you won’t want to miss.
- Articles
- Columns
- Links
- Media kit
||| MENU - smt007 Magazine
Rehm Thermal Systems Offers Various Types of Cooling for VisionXP+ Convection Soldering System
July 28, 2021 | Rehm Thermal SystemsEstimated reading time: 2 minutes
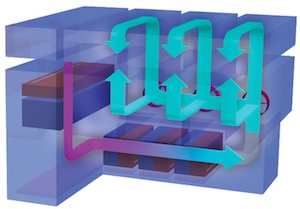
With the VisionXP+ convection soldering system from Rehm Thermal Systems, the soldering process does not end with the melting of the solder. For an optimal soldering result, a stable and reliable cooling process is particularly important, which can be flexibly designed with this type of system. In addition to standard cooling with four cooling modules, customers can also choose an extended cooling section ("Power Cooling Unit"), underside cooling or an energy-saving cooling variant. With Rehm CoolFlow, Rehm also offer an innovative cooling system using liquid nitrogen.
The standard cooling system installed in all Vision convection soldering systems consists of up to four individual cooling modules. These allow a precisely controlled cooling process as well as individual adjustment of the cooling gradient. For the cooling process, a small part of the warm and charged air volume present due to the soldering process is first extracted into the lower part of the system. It is then cleaned over several cooling modules and cooled to the desired temperature (usually below 20 °C). The air is then blown back from above onto the assembly, which results in the cooling. The “closed loop principle” guarantees a closed atmosphere cycle. The standard cooling section consists of active and passive cooling modules. The active cooling modules are supplied with water via a heat exchanger. The cooling filters can be easily cleaned and serviced at the rear of the system: the process chamber does not need to be opened to do this.
Gentle cooling with Power Cooling Unit
For gentle cooling, especially for complex assemblies, an extended cooling section can be connected to the VisionXP+. This can be implemented as an extension to standard cooling zones under a nitrogen atmosphere or as a separate, downstream module ("Power Cooling Unit") in an air atmosphere for higher cooling performance for insensitive materials. Advantage of the air-cooled variant: while nitrogen is needed in the process section of the convection unit to prevent oxidation, the extended cooling section no longer needs to be flooded with nitrogen, resulting in nitrogen savings.
Underside cooling for uniform cooling from above and below
For particularly massive or large assemblies or boards with product carriers, the VisionXP + can also be equipped with underside cooling. The actual cooling process is identical to that of the standard cooling section, but the extracted, cleaned and cooled air flows not only from above onto the module, but also from below.
Gradual cooling for energy saving
Rehm also offers an energy-saving cooling variant for the VisionXP+ convection soldering system: the air is extracted at several points rather than just one. This results in gradual cooling and offers significant energy saving potential.
Rehm CoolFlow: reduced energy usage with liquid nitrogen
Along with their partner Air Liquide, Rehm has developed a cooling system ("Rehm CoolFlow"), which uses the nitrogen used for inertia even more efficiently. The -196°C liquid nitrogen releases its energy in the cooling section, then evaporates and can then be used in its gaseous state for inerting the process atmosphere. The cooling water, which previously required high energy use for cooling, including cooling unit and refrigerant, is completely eliminated.
Suggested Items
Specially Developed for Laser Plastic Welding from LPKF
06/25/2025 | LPKFLPKF introduces TherMoPro, a thermographic analysis system specifically developed for laser plastic welding that transforms thermal data into concrete actionable insights. Through automated capture, evaluation, and interpretation of surface temperature patterns immediately after welding, the system provides unprecedented process transparency that correlates with product joining quality and long-term product stability.
Day 2: More Cutting-edge Insights at the EIPC Summer Conference
06/18/2025 | Pete Starkey, I-Connect007The European Institute for the PCB Community (EIPC) summer conference took place this year in Edinburgh, Scotland, June 3-4. This is the third of three articles on the conference. The other two cover Day 1’s sessions and the opening keynote speech. Below is a recap of the second day’s sessions.
Ventec Strengthens Commitment to Halogen-Free PCB Manufacturing in Europe
06/11/2025 | Ventec International GroupVentec International Group, the PCB materials innovator, manufacturer, supplier and one-stop shop for copper clad laminates, prepregs, as well as process consumables and PCB manufacturing equipment has established volume inventory of halogen-free FR4.1 and FR15.1 PCB materials at its European hub in Germany.
GEN3 Set to Host HATS²™ Technical Day at A.W. Technical Centre with Bob Neves
06/09/2025 | Gen3GEN3, a global leader in reliability testing and measurement solutions for the electronics industry, is excited to announce a dedicated HATS²™ Technical Day to be held at the A.W. Technical Centre in Farnborough, GEN3’s HQ. The event will showcase the HATS²™ (Highly Accelerated Thermal Shock) system with demos and presentations by Bob Neves, Chairman of RAS Inc. and creator of the HATS²™.
Rehm Thermal Systems Mexico: Ten Years of Growth and Innovation in an Emerging Market
06/03/2025 | Rehm Thermal SystemsOver ten years ago, Luis A. Garcia began his success story at Rehm Thermal Systems. On May 15, 2013, he initially joined as a member of the Rehm USA team.