-
- News
- Books
Featured Books
- smt007 Magazine
Latest Issues
Current IssueWhat's Your Sweet Spot?
Are you in a niche that’s growing or shrinking? Is it time to reassess and refocus? We spotlight companies thriving by redefining or reinforcing their niche. What are their insights?
Moving Forward With Confidence
In this issue, we focus on sales and quoting, workforce training, new IPC leadership in the U.S. and Canada, the effects of tariffs, CFX standards, and much more—all designed to provide perspective as you move through the cloud bank of today's shifting economic market.
Intelligent Test and Inspection
Are you ready to explore the cutting-edge advancements shaping the electronics manufacturing industry? The May 2025 issue of SMT007 Magazine is packed with insights, innovations, and expert perspectives that you won’t want to miss.
- Articles
- Columns
- Links
- Media kit
||| MENU - smt007 Magazine
The Meaning of (PCB) Life
July 28, 2021 | Bob Neves, Microtek ChinaEstimated reading time: 2 minutes
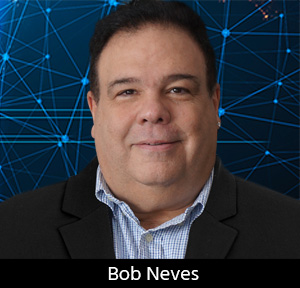
New products, new designs, but still the age-old question persists, “How long will it live and what will its quality of life be?” Assembled printed circuit boards (PCBAs) are a complex system of materials, components, and interconnections that all need to work as intended for the product to reliably operate during its expected life. All it takes is one piece of that complex system to fail and the product’s life span will disappoint.
To manage this disappointment in life—in this case reliability failure—the first step is to categorize the influence that each piece of this complex PCBA system has on the life of the product. In addition, as the PCBA is subjected to very high temperatures during component attachment, the influence that each piece has on life may change before and after the attachment process, so simulation of this attachment process prior to any life prediction testing is vital to understanding the true life expectancy of a PCBA.
Evaluating all the parts and systems in a PCBA system is an overwhelming task to say the least, so I tend to follow the Pareto principle when looking to pare down the list to something more manageable. The Pareto principle roughly states that 80% of consequences come from 20% of the causes. This nugget of wisdom came from Joseph M. Juran who studied the work of Vilfredo Pareto and ultimately published his Quality Control Handbook in 1951, which is still used today as a basis for management of quality and quality control.
The next step in the process is identifying the 20% that will cause most of a product’s life problems and subsequently focusing efforts on reducing the disappointment in life from these items. Active and passive components, PCBs, subsystems, connectors, wiring harnesses—the list goes on. Once you have identified a set of likely offenders, you will need to decide how to evaluate them for their effect on premature life failure.
Terms like “infant mortality,” “fatal anomaly,” “long-term reliability,” “Weibull analysis,” and “latent defects” are thrown around when speaking about product life. There are also a host of acronyms associated with this branch of faith-based prediction, most of which are so important that they have been bumped up from three- to four-letter acronyms: ESS (environmental stress screening), HATS (highly accelerated thermal shock), HAST (highly accelerated stress testing), HALT (highly accelerated life testing), HASS (highly accelerated stress screening), MTBF (mean time between failure) and burn-in (first on the scene, entrenched before someone came up with an appropriately long acronym). There is a whole branch of palm readers—I mean scientists and engineers—whose job it is to predict the life span of a product. You remember the part in your car, TV, or cellphone that dies a short time after the warranty expires? Well, these wizards (and witches) are the ones who predicted that fortune. How do you think they came up with the warranty terms in the first place?
To read this entire article, which appeared in the July 2021 issue of SMT007, click here.