-
- News
- Books
Featured Books
- smt007 Magazine
Latest Issues
Current IssueWhat's Your Sweet Spot?
Are you in a niche that’s growing or shrinking? Is it time to reassess and refocus? We spotlight companies thriving by redefining or reinforcing their niche. What are their insights?
Moving Forward With Confidence
In this issue, we focus on sales and quoting, workforce training, new IPC leadership in the U.S. and Canada, the effects of tariffs, CFX standards, and much more—all designed to provide perspective as you move through the cloud bank of today's shifting economic market.
Intelligent Test and Inspection
Are you ready to explore the cutting-edge advancements shaping the electronics manufacturing industry? The May 2025 issue of SMT007 Magazine is packed with insights, innovations, and expert perspectives that you won’t want to miss.
- Articles
- Columns
- Links
- Media kit
||| MENU - smt007 Magazine
Catching Up with the Latest at Datest
August 3, 2021 | Nolan Johnson, I-Connect007Estimated reading time: 3 minutes
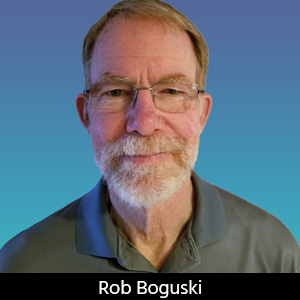
Nolan Johnson chats with Datest's Rob Boguski about the latest happenings at the Fremont, California testing and inspection service provider.
Nolan Johnson: This is our first chance to talk about Datest since last year’s SMTAI. How has business been?
Rob Boguski: It has been a busy few months, particularly since January. Like everybody, we’ve emerged from our cocoon of the last year and life is certainly starting to accelerate the pace of businesses faster—the degree of involvement, the types of projects we’re getting involved with, new customer activity is very vibrant right now. It seems like everybody is reinvigorated to some degree. Everyone in my immediate circle of colleagues is very busy right now. There’s a high demand for different products that allow for many different levels, market sectors, and segments that are all starting to take off. We’re the beneficiary to a large extent, because these being in most cases electronic products, they’ve got to be tested to some form or another. On the back end, we’re seeing increased demand for inspection and failure analysis services. More stuff breaks with increased volume. That’s good for business.
Things are not working as reliably as they should, or they’re being put under increased strain in the field due to this pent-up demand, and they’re not lasting. Their design life is being truncated because they’re being run flat out, and so things are being brought to us that don’t work. That’s what we do. We figure out why they don’t work, and hopefully, we can help out our engineering clients that way. Just this morning, a company we previously hadn’t done business with emailed me early, wanting to come in this very day to X-ray some valves that had failed in a hydraulic system. They wanted to isolate the source of the failure and it was a line down situation, so it really was imperative that they did that today.
Fortunately, we had a system available to accommodate, and I was on the phone with our operations manager, where he was describing to me what was going on, and we were CT scanning these products as we were speaking. Hopefully, by the end of the day, we’re going to at least have some idea of what’s going on and we can help this customer out and get them pointed in the direction of a solution.
Johnson: You mentioned pent-up demand. Is this a bunch of brand-new product starts, or are you seeing projects that were paused through the lockdowns?
Boguski: A lot of projects that were paused or put on the slow track, either due to financing or lack of availability of resources, supply chain problems—the things that we all read about, lack of components—are starting to come to fruition, getting the green light and transitioning from prototyping into the production stage. Maybe they were being done at a slower pace surreptitiously for the 14 months previous and suddenly things have opened up and they need to move fast to make a market window. Almost everything we’re hearing that is new is extremely urgent. I’ve taken on a handful of new customers in the past week and for every single new customer, the theme is the same: “I need something done right now. I need it in days, not in weeks. I need to obtain answers either to my problem or to get this product tested and get it out the door by the end of July.”
Johnson: What’s your take on this, Rob? Is this a board design/electronics design issue? Do the products you’re seeing need to be designed for more stress or more capability than they have been previously?
Boguski: Yes. Or they were hastily designed with little or no consideration for the manufacturing environment. Case in point, we’re working on a project now, basically refereeing a dispute between a bare board fabricator and a contract manufacturer. A bunch of boards got built, shipped to the field, and started failing. The OEM started tearing into them, found pinholes in solder, which in some cases had metastasized into voids and they claim these are the root cause of field failures. The OEM goes back to the assembly house, which points the finger at fab house. The fab house returns fire, pointing a finger at assembly house. Then we get the call: We’re going to give you a random sampling of boards; tell us what you see.
To read this entire conversation, which appeared in the August 2021 issue of SMT007 Magazine, click here.