-
- News
- Books
Featured Books
- smt007 Magazine
Latest Issues
Current IssueWhat's Your Sweet Spot?
Are you in a niche that’s growing or shrinking? Is it time to reassess and refocus? We spotlight companies thriving by redefining or reinforcing their niche. What are their insights?
Moving Forward With Confidence
In this issue, we focus on sales and quoting, workforce training, new IPC leadership in the U.S. and Canada, the effects of tariffs, CFX standards, and much more—all designed to provide perspective as you move through the cloud bank of today's shifting economic market.
Intelligent Test and Inspection
Are you ready to explore the cutting-edge advancements shaping the electronics manufacturing industry? The May 2025 issue of SMT007 Magazine is packed with insights, innovations, and expert perspectives that you won’t want to miss.
- Articles
- Columns
- Links
- Media kit
||| MENU - smt007 Magazine
Siemens Global Webinar: Data-Driven Manufacturing in the Electronics Industry
September 22, 2021 | Pete Starkey, I-Connect007Estimated reading time: 8 minutes
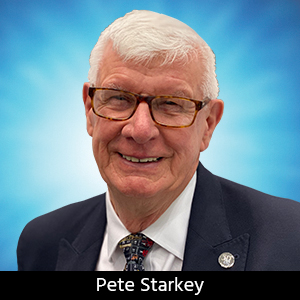
As a retired PCB manufacturer who grew up in the days of manual systems and hand-written batch production and inspection records, although we did have an electric typewriter and a calculating machine, I saw the introduction of computer-aided design and engineering, followed by a disjointed series of proprietary computerised production-planning, production-monitoring, and quality-control systems.
Looking at what is available now, exemplified by the fully integrated digital manufacturing solutions offered by Siemens, I recognise that data-driven manufacturing is the future, digitalisation is a must, and only smart usage of the digital twin information will open the doors to improvements and business success.
I had the opportunity to attend the second in the series of Siemens global webinars on data-driven manufacturing in the electronics industry, this time focused on data acquisition and analysis, discussing challenges and methodologies and detailing hardware and software solutions, exemplified by real-world illustrations of successful implementation.
I-Connect007 columnist and co-author of The Printed Circuit Assembler's Guide to... Smart Data: Using Data to Improve Manufacturing, Sagi Reuven, in his primary role as head of business development at Siemens Digital Industries Software, introduced and moderated the webinar.
Trends and Challenges in Manufacturing Execution Systems
Reuven referred briefly to the trends and challenges driving the implementation of software solutions in manufacturing execution systems (which he considered were already familiar topics in the industry), and he emphasised his aim to concentrate on discussing real examples and the innovation projects already in pilot phase.
He grouped these trends and challenges into four columns—delivering lot-size one, optimising material usage, personalised products, and compliance—explaining that the “compliance” column had been added because of a growing demand in customer requirement for long-term traceability, especially in medical and automotive sectors. The lot-size-one trend was characterised by high-mix production and the need for flexibility, especially in the light of present-day supply-chain challenges. These challenges further complicated procedures for optimisation of substantial material costs, currently estimated to be between 80–92% across the industry. Typical attributes of personalised products were the huge numbers of variants per product, together with the need to maintain productivity and quality whilst remaining profitable.
What solutions were available? Reuven commented that data-driven manufacturing could be a modular project, starting with a basic level of data acquisition, without even having any control, just collecting the data and pushing it up the levels to the internal MES system or shop-floor management system. The data could be moved up another level to a point-solution layer, typically for material management or analytics. Alternatively, Siemens could offer a fully integrated digital manufacturing solution known as the Opcenter Execution Electronics Suite, incorporating the MES system together with all the Valor applications: scheduling, materials management, data acquisition, analytics, and reporting.
Over the last two decades, the amount of data has grown exponentially. A PCB work order that resulted in 100 records 20 years ago might today generate billions of records and terabytes of data, and there could be a requirement to store this information for up to 15 years, mainly for purposes of compliance. Reuven discussed how this data could be used constructively, for example, to build a profile and start talking about the digital twin of the product, its process traceability, material traceability, and product quality; and the same for individual components, as well as a digital twin of the production line itself, with different levels of metrics: production performance for individual machines and the line as a whole, material WIP status etc.
Running the data through an analytics engine helped identify correlations and draw insights about production. The holistic approach gave the opportunity to close the loop from manufacturing back to engineering and design, and resulted in improvements in the process and the product. Realistically, he considered it might take a few more years before a achieving a full internet-of-things solution, but this was definitely in prospect. The data challenge was to convert “big data” into “smart data”, which would offer the benefits of:
- Improving asset utilisation
- Supporting manufacturing “what-if” analysis
- Identifying issues more quickly
- Driving quality improvement
- Increasing design-to-manufacturing efficiency
- Enabling predictive maintenance
He quoted actual examples of time-to-market gains, savings in set-up time and work instructions, enhanced operator efficiency and equipment utilisation, and zero-defect initiatives. And there were many instances where companies also saw reputational gains as significant benefits of digitalisation.
Concluding his overview, Reuven discussed the limitations of manual data collection involving operators and spreadsheets, and quoted cases where skewed data had seriously impacted investment decisions, or had given misleading information on true production capacities, actual asset utilisation figures and real bottlenecks.
Opcenter Execution Electronics Suite
The second presentation came from Frank Schaldach, manufacturing operations management industry manager electronics and semiconductor with Siemens Digital Industries Software, who was currently involved, along with Reuven, in leading the roll-out of the Opcenter Execution Electronics Suite full digital manufacturing solution to the electronics industry.
Schaldach discussed the details and business value of reports generated by the Opcenter Suite, which provided backward and forward end-to-end traceability through every stage of production from raw materials to finished goods; traceable by serial number, material, lot number or work order. Using as example the product traceability report for a PCB, he demonstrated the completeness and precision of information available and the versatility of the mechanism for tracing any detail considered necessary. For instance, in addition to the whole manufacturing history of that individual PCB, what other PCBs had been fabricated from the same material batch (for which all of its own history was readily accessible), and what other PCBs had been assembled on the same equipment (for which the complete production and performance history was again available), and with what components, and so on: page after page of clear traceability records, each logically and selectively accessible as required. The information was effective in supporting the fulfilment of compliance requirements, and particularly useful in determining root causes of failure and minimising the costs of product recalls.
He then considered the value of quality reports, commenting on how they also related to material optimisation and productivity improvement as well as enabling speedy root cause identification. Three examples he discussed were the trash cost report, the quality history KPI report and the defected materials dashboard, and he demonstrated how straightforwardly these could provide categorised and understandable information to assist in problem-solving.
Manufacturing process reports were valuable in providing the basis for fulfilling compliance requirements, and could also be used for root-cause investigation and improved productivity. Schaldach discussed the features, functions, and applications of reports based on serial number history, box-build by board identification or work order, and work in progress.
Reuven returned to describe a case history: A long-established Romanian company with an electronics assembly factory had relied on manual inventory management, production tracking, and quality tracking, with their reporting done mainly by Excel spreadsheets and not a lot of traceability data recorded. The company wanted to share more information between departments and with their customers. Their main focus was around the performance and traceability dashboard, to help improve their efficiency and to present an enhanced image to their customer. Initially, their chosen business solution was not a full-blown MES but a basic Valor IoT Box and Manufacturing Analytics, which gave them good business results for a relatively low investment. The system offered ease of configuration and customisation, with all-in-one information available at management level and immediate sharing to other departments and customers. Their primary focus was around performance and traceability dashboards, and they continued to improve efficiency and to run studies for new-product-introduction processes. Their principal business results had been an improvement in the quality of their products, a better understanding of every stage of their manufacturing process, and quicker reaction times. Their production efficiency improved as a consequence of automated processes of data mining, analytics and insights.
Innovations for Data-Driven Manufacturing
Sagi Reuven then handed over to Tovi Yadin, innovation solutions manager with Valor, specialist in data-driven manufacturing and currently focused on machine-to-machine applications to facilitate the next steps toward autonomous manufacturing. Yadin reviewed Siemens innovations for electronics data-driven manufacturing, and gave her perspective on the present and future of the industry.
She considered that the core concept of the Industry 4.0 revolution was that data enabled machines communicate with each other. Historically, if data had been available it primarily benefited operators and line managers by allowing them to improve their shop-floor activities. In an Industry 4.0 context, data would allow the machines, the lines, and the software to improve themselves interactively without the need for operator intervention.
Using a series of examples, she illustrated some of the advanced capabilities that had been introduced. Her first example was a new Valor application which set up the assembly line to automatically stop production and raise alerts following recurring errors, which would improve line quality and utilisation, and consequently protect profits. This application collected data in real-time and tracked failures, stopping production if a user-defined error threshold was exceeded, so that the operator could fix the problem immediately and maximise machine utilisation, yield and quality.
Her second example illustrated an unprecedented new level of component traceability that could identify 100% of counterfeit and malicious components in the production line. Traceability gaps were eliminated by the Valor-Cyborg solution which combined big-data technologies with artificial intelligence to identify counterfeit components on-line. Her third example described a new Valor application that automatically issued board-specific “do-not-process” instructions to placement and inspection equipment when X-out boards were present in multi-image panels, saving machine-time and wasted components. Siemens’ Innovation Team had also developed technological tools based on data analysis and artificial intelligence to improve the utilisation, productivity and material consumption of the pick-and-place process by reducing the frequency of pickup errors.
Yadin envisaged a future electronics manufacturing industry based on machine-to-machine connectivity and the increasing use of advanced machine learning and artificial intelligence technologies, recognising the fundamental value of data and unlocking the potential of digitalization.
Attending this webinar has been an enlightening experience, and I am grateful to Siemens for helping me to gain a basic understanding of the capability and versatility of its Opcenter Execution Electronics Suite.
To view the Siemens global webinar, click here.