-
- News
- Books
Featured Books
- smt007 Magazine
Latest Issues
Current IssueWhat's Your Sweet Spot?
Are you in a niche that’s growing or shrinking? Is it time to reassess and refocus? We spotlight companies thriving by redefining or reinforcing their niche. What are their insights?
Moving Forward With Confidence
In this issue, we focus on sales and quoting, workforce training, new IPC leadership in the U.S. and Canada, the effects of tariffs, CFX standards, and much more—all designed to provide perspective as you move through the cloud bank of today's shifting economic market.
Intelligent Test and Inspection
Are you ready to explore the cutting-edge advancements shaping the electronics manufacturing industry? The May 2025 issue of SMT007 Magazine is packed with insights, innovations, and expert perspectives that you won’t want to miss.
- Articles
- Columns
- Links
- Media kit
||| MENU - smt007 Magazine
Driving Lean Manufacturing with Digitalization
October 6, 2021 | Kobi Levi, Siemens Digital Industries Software, Sponsored ContentEstimated reading time: 9 minutes
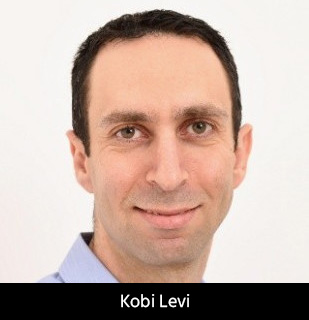
Reducing waste in the manufacturing process is always a challenge, especially when it comes to new product introductions (NPI). It is a key pain point for manufacturers, as waste leads to delays, unexpected costs, quality issues, and lost profit. Waste isn’t always about material that must be discarded—it can also include idle workers and equipment, unused material, and inefficient planning processes.
Lean manufacturing tackles the problem of waste in the manufacturing process, wherever it occurs. To consistently reduce waste and apply lean manufacturing principles, manufacturers need an IT system—including both PLM and MOM—that enables better collaboration, maintains, and utilizes organizational knowledge, monitors lean KPIs, and helps the organization achieve first-time-right design and production for all products.
First-time-right with the Digital Twin
PLM and MOM systems allow manufacturers to digitalize production and create digital twins of products, processes, and production lines. Using digital twins, manufacturers can conduct trial and error in a virtual environment and rectify any problems before they reach manufacturing. The virtual fixes save valuable time and resources like energy, machine time, and production materials. Importantly, they also advance the ultimate lean manufacturing goal—first-time-right manufacturing. When a manufacturer can produce a product right on the first attempt, production becomes much more efficient and predictable. This eventually leads to cost optimization, shorter time to market, and better resource utilization without reducing the quality of the products.
Digitalization of PCB Assembly NPI Process
Digitalization can also play an important role in making the PCB assembly NPI leaner for electronics manufacturing companies. Siemens PLM software has made this its mission, providing a suite of applications on the Teamcenter platform that help manufacturers build a digital twin for the entire product lifecycle, including both electronics and mechanics. Valor Process Preparation, in particular, allows manufacturers to digitalize the PCB assembly process as a one-stop shop and make it extremely efficient and lean.
Standardizing and Enhancing Design Data
Reading the Design Data
The first task of the PCB assembly process engineer is to read the design data. It sounds like a straightforward task, but when done manually, mistakes are common. Often, the design data of the wrong PCB is uploaded, or the engineer reads the wrong configuration of the PCB, or reads unreleased design data. Any one of these mistakes can result the wrong PCB being produced, forcing manufacturers to scrap an entire batch.
An EMS faces an additional challenge when reading PCB designs. Since their customers send PCB designs in different formats, the EMS must be able to read designs in multiple different formats. This is a technical challenge that can impact time to market and product quality. It takes time to convert the design data into the EMS IT system’s format and the conversion is susceptible to human error.
Digitalized solutions solve these challenges and ensure that the right design data is automatically delivered to the process engineer. These solutions also enable production in different sites according to logistic requirements such as component supply, production line availability and delivery destination. They also make it easy to convert design formats so EMSs can work with any data format their customers send.
Defining Physical Shapes of the PCB Components
The PCB design does not typically include the accurate geometry of the components assembled on the PCB. This poses a challenge for the assembly and test of the PCB plans, as it is impossible to create assembly work instructions and assembly programs for the SMT machines without knowing the exact shape of the assembled components. Therefore, before planning the PCB assembly process, the process engineer must first search different libraries to find the accurate shapes of all components. A digitalized solution with pre-existing part libraries can significantly mitigate this challenge, enabling the automated update of all PCB components with accurate geometrical representation in the digital environment. This accurate “digital twin” of the design results in better decision-making when planning the assembly process and supports first-time-right assembly while shifting the planning decisions left to an early stage of the process planning.
Page 1 of 3