-
- News
- Books
Featured Books
- smt007 Magazine
Latest Issues
Current IssueWhat's Your Sweet Spot?
Are you in a niche that’s growing or shrinking? Is it time to reassess and refocus? We spotlight companies thriving by redefining or reinforcing their niche. What are their insights?
Moving Forward With Confidence
In this issue, we focus on sales and quoting, workforce training, new IPC leadership in the U.S. and Canada, the effects of tariffs, CFX standards, and much more—all designed to provide perspective as you move through the cloud bank of today's shifting economic market.
Intelligent Test and Inspection
Are you ready to explore the cutting-edge advancements shaping the electronics manufacturing industry? The May 2025 issue of SMT007 Magazine is packed with insights, innovations, and expert perspectives that you won’t want to miss.
- Articles
- Columns
- Links
- Media kit
||| MENU - smt007 Magazine
Increase Production Yield by Investing in Leading-Edge Equipment
October 11, 2021 | Brent Fischthal, Koh Young AmericaEstimated reading time: 3 minutes
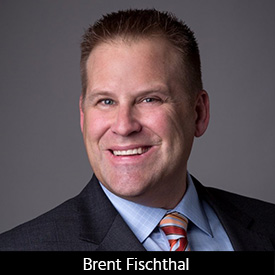
As we wind down 2021, we eagerly anticipate the new year, which should bring new opportunities. With the start of the new year, we often see new capital equipment budgets roll out, and production engineers and operations managers begin to evaluate how to best spend their newfound resources to improve the processes. There are multiple papers readily available from industry experts like Chrys Shea of Shea Engineering about the significance of solder paste inspection (SPI) equipment. Therein, you can find justification about why adding a solder paste inspection machine should be the first piece of inspection equipment considered. SPI will immediately reduce assembly defects.
Therefore, let us consider automated optical inspection (AOI). AOI technology has been available for decades, but only since the introduction and industry adoption of real 3D measurement has it emerged as a major area of focus to prevent defects and improve production yields in post pre-reflow and post-reflow positions. Yet, many manufacturers are using antiquated 2D or quasi-3D systems that increase false calls and escapes.
In the early days of optical inspection, SPI and AOI systems were based on 2D inspection technology. These 2D systems were looking at di?erent grey levels for solder joint and component detection. Most decisions were made by a “good/bad” comparison to reference images or “golden boards.” While many 2D AOI systems remain in use, the e?ort needed to keep this technology at a low level of escape and false-call rates can be exceptionally high. These antiquated 2D systems facilitate false calls and failure escapes. This is because the concept of comparing reference images is still the main technique applied in 2D systems. To help the situation, some equipment manufacturers have added additional cameras and projectors to create a “quasi 3D” or “2.5D” inspection technology, but it is still based on the same inadequate concept of comparison or color assessment.
Now, after the introduction of 3D AOI, a transition to true 3D measurement is taking place. The benefits are clear: rock-solid threshold and inspection tolerances that minimize escape and false-call rates with minimum debugging e?ort. If you are facing production quality challenges due to your old 2D AOI equipment, it may be time to upgrade.
Measurement-based Inspection
Process optimization is desired by every manufacturer, as well as equipment suppliers. However, it has been difficult to realize due to the limitation of two-dimensional (2D) imaging, which was the de facto standard for the past decades. Not only it is difficult for 2D automated optical inspection (AOI) systems to identify defects on curved and reflective solder joint, 2D AOI systems do not generate reliable data. Every aspect of the 2D inspection process relies on contrast, not quantitative measurement. As such, 2D AOI users must either scrap or repair defective boards, which increases costs and eliminates process improvement opportunities.
The introduction of 3D imaging to the inspection market solved some of the problems. By measuring components and solder joints, and then offering critical height information to the inspection algorithms, users could locate errors like pad overhang and insufficient soldering. However, the validity of the measurement data remained questionable as most of the 3D AOI systems use “blob detection” to find the component body; but, this technique is susceptible to external factors like board warpage and component proximity. Since finding the component body is the critical first step in the inspection process, it can negatively affect the whole inspection sequence if inaccurate.
To read this entire article, which appeared in the October 2021 issue of SMT007 Magazine, click here.
Be sure to check out Koh Young's I-007e Micro Webinar, Converting Process Data Into Intelligence, and download its companion eBook, The Printed Circuit Assembler’s Guide to...SMT Inspection, Today, Tomorrow and Beyond.