-
- News
- Books
Featured Books
- smt007 Magazine
Latest Issues
Current IssueSpotlight on India
We invite you on a virtual tour of India’s thriving ecosystem, guided by the Global Electronics Association’s India office staff, who share their insights into the region’s growth and opportunities.
Supply Chain Strategies
A successful brand is built on strong customer relationships—anchored by a well-orchestrated supply chain at its core. This month, we look at how managing your supply chain directly influences customer perception.
What's Your Sweet Spot?
Are you in a niche that’s growing or shrinking? Is it time to reassess and refocus? We spotlight companies thriving by redefining or reinforcing their niche. What are their insights?
- Articles
- Columns
- Links
- Media kit
||| MENU - smt007 Magazine
Estimated reading time: 5 minutes
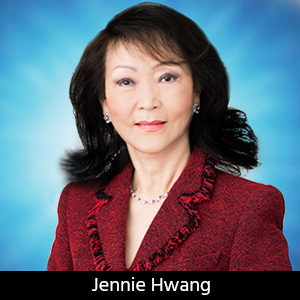
SMT Perspectives and Prospects: Reliability Primer—A Pragmatic SMT Perspective
Manufacturers and customers alike embrace a product’s reliability as the priority. Accordingly, if I say “reliability” is a relative term, would you respond with “Why is it relative?” Well, when we look at the reliability, be it associated with a physical product or virtual service, there is a set of performance expectations from the users or the customers. Take a smartphone or a car as an example; a manufacturer provides the product warranty with a specified timeline and other specificities. If the product does not perform within the warranty time, the manufacturer or the authorized distributor will fix the problem free-of-charge, although the user (the customer) prefers not to experience any inconvenient return or repair. By the same token, if the product encounters a problem outside the warranty, it is the customer’s luck—or out of luck, such as if a new car sadly crashes and the warranty is not honored.
Another materiality worth noting is that a literally “perfect” product is hard to come by, if ever. This can be vividly illustrated by the continued rollout of new models of smartphones since its debut approximately 25 years ago; every new model offers additional performances that are useful and enjoyable to use. And every new model of the smartphones has approached another level of perfection and reliable performance.
What does this mean to us? Is perfect the enemy of the good?
What is Reliability?
Reliability, in reference to the Oxford Languages dictionary, is defined as the quality of being trustworthy or of performing consistently well; trustworthiness is doing what the system is expected or designed to do.
A product’s reliability is an operational reliability, which can be practically defined as a product performing its expected functions for a designated period under an anticipated set of service conditions. A product should be designed and built not necessarily for the maximum reliability, rather for the operational reliability that is subject to practical requirements and desirability, such as the targeted time-to-market, the acceptable cost to manufacture, the overall manufacturability, and the total cost of ownership.
Is Cost a Factor?
The total cost of ownership covers the full cycle of making a product from procurement to production to reliable service during a product’s life span. Factors such as production yield, defects, rework, a set of product functions, and the targeted reliability add up to a product’s total cost.
An absolute reliability is not always the isolated pursuit as reliability does bear a cost. A qualitative relationship between the system cost and the level of system reliability for the pre-shipment and the post-shipment stages can be illustrated in Figure 1.
Within the realm of surface mount technology (SMT), the assessment of the cost requires one to consider the total cost of ownership. This comprises:
- Solder material cost per unit weight
- Process operational cost
- Cost of components
- Cost of PCB
- Equipment capital expenditure and depreciation
- Production yield and defects
- Cost of rework, if any
- Product reliability
Accordingly, a viable product is the result of a tradeoff and a balance among the performance, manufacturability, cost, and business terms to deliver the expected reliability.
How Does SMT Operation Affect Reliability?
In the SMT manufacturing operation, the main players of reliability include the PCB bare board, all components before assembly operation, all components after assembly operation, solder interconnections, and the manufacturability. The resulting system’s reliability hinges on the quality, practicality, compatibility, and reliability of each of the players, and the interplay among the players.
On the PCB, the solderability and planarity of surface finish and the PCB internal structure integrity before reflow/wave and other process steps, the PCB internal integrity after reflow/wave/rework, and other process steps are key parameters to watch for. In particular, PCB vulnerability to high temperature excursions escalates with the level of PCB complexity (e.g., higher number of layers, larger PCB size, thicker PCB) increases. Being free of degradation after high temperature processing, which may lead to production defects and/or product failure, such as the result of pad-cratering, pad-lifting, or de-lamination, must be assured.
On solder interconnections, the initial solder alloy selected to use is equally important to the solder joint integrity resulting from the manufacturing-related factors. In combination, both dictate the quality and reliability of the resulting solder interconnections. With respect to solder alloy, four fundamental correlations are worthwhile noting:
- The alloy composition determines the process temperature required.
- The alloy’s compositional makeup dominates the microstructure, which in turn reflects on the solder joint behavior during its service life.
- The microstructure and its evolution dictate failure mechanisms.
- An intrinsically inferior alloy cannot deliver a superior performance, i.e., the maximum performance is limited by the intrinsic properties of an alloy.
From an SMT reliability perspective, the goal in selecting an optimal solder joint material is to deliver the plausible metallurgical properties and the anticipated behavior while not requiring an elevated process temperature, i.e., rendering the process temperature as close to that of SnPb eutectic alloy. To accomplish this goal under the established manufacturing infrastructure, a lead-free composition must resort to the metallurgy of a quaternary alloy (not doping elements); I have presented this scientific predication in my professional development courses at various international events and numerous locales spanning the last 25 years.
How Does Manufacturability Play a Role?
Is manufacturability a critical element of the product’s reliability?
The answer is a resounding affirmation; reliability and manufacturability are closely linked. To have a sound manufacturability, four essential practices should be observed:
- An adequate process window (e.g., reflow profile setting).
- A sufficient material performance latitude (e.g., solder paste wetting ability).
- Compatibility between process and material (e.g., reflow profile being in sync with properties of solder paste).
- Process control.
Each of the process steps must deliver an adequate process window and each of the materials selected should possess an adequate performance latitude. This is particularly true in the reflow step—a narrow process window is expected to marginalize the process, which often causes higher defect rates on the production floor and/or product reliability issues during service.
Closing Thoughts
To ensure the target reliability, a holistic approach should be exercised to plan for reliability, to design for reliability, to select materials for reliability, to select components for reliability, and to manufacture for reliability. Additionally, utilizing the knowledge in known failure sources or mechanisms coupled with practicing the know-how to prevent likely failure processes from occurring further enhance a product’s reliability.
After all, the Second Law of Thermodynamics and the metallurgical Dislocation Theory do not change. In a nutshell, the golden rule is to integrate three best practices:
- Deliberately and systematically prevent likely known failure causes.
- Diligently set up a robust manufacturing operation.
- Prudently utilize the profound scientific and engineering principles to take care of the unknowns.
Presentation
Dr. Hwang will deliver a professional development course, “Solder Joint Reliability—Principle and Practice” from 9 a.m. to noon November 1; and a course on “Reliability of Electronics—Role of Intermetallic Compounds” from 2 to 5 p.m. November 1, at the SMTA International Conference.
This column originally appeared in the October 2021 issue of SMT007 Magazine.
More Columns from SMT Perspectives and Prospects
SMT Perspectives and Prospects: Warren Buffett’s Perpetual Wisdom, Part 2SMT Perspectives and Prospects: Warren Buffett’s Perpetual Wisdom, Part 1
SMT Perspectives and Prospects: Artificial Intelligence, Part 5: Brain, Mind, Intelligence
SMT Perspectives and Prospects: Artificial Intelligence, Part 4—Prompt Engineering
SMT Perspectives and Prospects: The AI Era, Part 3: LLMs, SLMs, and Foundation Models
SMT Perspectives and Prospects: A Dose of Wisdom
SMT Prospects and Perspectives: AI Opportunities, Challenges, and Possibilities, Part 1
SMT Perspectives and Prospects: Critical Materials—A Compelling Case, Part 3