-
- News
- Books
Featured Books
- pcb007 Magazine
Latest Issues
Current IssueInventing the Future with SEL
Two years after launching its state-of-the-art PCB facility, SEL shares lessons in vision, execution, and innovation, plus insights from industry icons and technology leaders shaping the future of PCB fabrication.
Sales: From Pitch to PO
From the first cold call to finally receiving that first purchase order, the July PCB007 Magazine breaks down some critical parts of the sales stack. To up your sales game, read on!
The Hole Truth: Via Integrity in an HDI World
From the drilled hole to registration across multiple sequential lamination cycles, to the quality of your copper plating, via reliability in an HDI world is becoming an ever-greater challenge. This month we look at “The Hole Truth,” from creating the “perfect” via to how you can assure via quality and reliability, the first time, every time.
- Articles
- Columns
- Links
- Media kit
||| MENU - pcb007 Magazine
Estimated reading time: 4 minutes
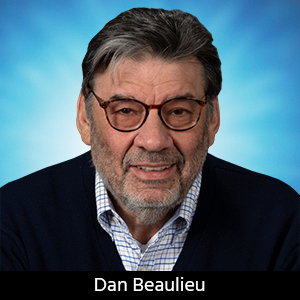
It's Only Common Sense: Together We Can Figure This Out
If we’re lucky, the components have left Asia and are waiting to be unloaded to the correct West Coast ports where, hopefully, someone can bring them to where they need to be via trains, planes, or trucks.
Hopefully, they are not still sitting in China.
Even less hopefully, they are even being fabricated at all, since China is having its own set of problems, not the least of which are severe power shortages.
These are the challenges we are facing in North America. Then, we make the issues even more challenging by not adapting to meet these challenges.
PCBs are not being put on order yet because the customers do not have the components. The assemblers are waiting to have their entire BOM before they order the boards.
The customers want the boards really fast so they can move their inventory, ship assembled product, invoice that product, and finally get paid for all that inventory they have been holding for so long.
But many times, when the CMs finally do get their complete component sets and order the boards, they want them expedited because they wanted them yesterday. But the board fabricators cannot turn around the boards quickly because they have to wait for those laminates that are on the same ships as the components.
Such is the supply chain as we know it today. It’s a chain filled with missing links that are frankly screwing everything up.
Why don’t we sit down and think about this for a minute? We can overcome many of these delays by actually working together and performing some of these actions concurrently rather than consecutively.
Here are some pretty good ideas for overcoming some of these challenges:
- The OEMs should work closely with their designers and engineers to make sure they select components, laminates, and other materials that are more easily acquired than the more esoteric harder-to-find ones.
- The OEMs and their engineers should be willing to accept and make intelligent substitutions when the needs arise. This is not time to be a stickler and wait forever for the right, precise parts that you want. If other parts or other laminates will work, then use them. They have to be willing to use other parts and laminates even if they are not spec’d in.
- Contract manufacturers must deal with it when it comes to asking their customers for changes and substitutions. I know that the very idea of doing this is terrifying, but it is necessary at this time.
- The OEMs and CMs need to order the boards early, even if they do not have the complete component set. That way the PCB fabricators can order the laminate and eat up that lead time while their customers are waiting for components and then get the boards built exactly when their customers need them. That’s not hard and there is not extra cost since they will not be invoiced until the boards are shipped. In fact, there can be a savings since ordering the boards in advance can cut down those expediate fees.
- This is a tough one, but since we are all in this together, the CMs should charge their customers a small carrying fee for holding the components they have already purchased and are sitting there while they wait for the rest of the critical components to arrive. It does not have to be an exorbitant fee, just something that will ease some of the financial burden of holding components for so long before they finally get paid for the finished product, which could be as long as a half-year or more.
- The key here is cooperation. Say it with me: “We are all in this together.” This means that if we are going to not only survive but even thrive in these difficult days we must work together—designers, PCB fabricators, assemblers and OEMs should all be working together to find a way. PCB shops should be helping one another out with laminates, processes, and equipment sharing. For example, if a PCB shop cannot meet a customer’s needs then help that customer find the right solution, suggest another PCB company who can provide that solution. Doing this for one another will work in the long run and reflects the true meaning of, say it with me again, “We are all in this together!”
- Finally, we should all be open and honest with one another. Telling one another the truth about when those critical parts and laminates will be shipped and received. This is key.
To me, this is how we will get through this. If some of you have other ideas and suggestions on how we can all work together so meet and solve these challenges, please share them. I’d love to hear from you.
It’s only common sense.
Dan Beaulieu is president of D.B. Management Group.
More Columns from It's Only Common Sense
It’s Only Common Sense: Why Failure Is an Opportunity for GrowthIt’s Only Common Sense: Stop Chasing New Customers and Start Keeping the Ones You Have
It’s Only Common Sense: Sales as a Team Sport
It’s Only Common Sense: How to Win Back Lost Customers
It’s Only Common Sense: Knowing When to Walk Away
It’s Only Common Sense: Customer Service Is Sales in Disguise
It’s Only Common Sense: Your Guide to Better Time Management
It’s Only Common Sense: Selling to Today's Generation of Buyers