-
- News
- Books
Featured Books
- pcb007 Magazine
Latest Issues
Current IssueInventing the Future with SEL
Two years after launching its state-of-the-art PCB facility, SEL shares lessons in vision, execution, and innovation, plus insights from industry icons and technology leaders shaping the future of PCB fabrication.
Sales: From Pitch to PO
From the first cold call to finally receiving that first purchase order, the July PCB007 Magazine breaks down some critical parts of the sales stack. To up your sales game, read on!
The Hole Truth: Via Integrity in an HDI World
From the drilled hole to registration across multiple sequential lamination cycles, to the quality of your copper plating, via reliability in an HDI world is becoming an ever-greater challenge. This month we look at “The Hole Truth,” from creating the “perfect” via to how you can assure via quality and reliability, the first time, every time.
- Articles
- Columns
- Links
- Media kit
||| MENU - pcb007 Magazine
Estimated reading time: 5 minutes
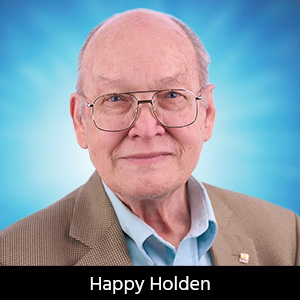
Contact Columnist Form
Happy's Tech Talk #2: Induction Lamination
Multilayers have been around about as long as the printed circuit. The industry has always used heated hydraulic lamination presses to produce these multilayers, with the introduction of vacuum assist in the 1980s. But recently, with the encouragement of GreenSource Fabrication, induction lamination has been perfected by Chemplate Materials of Spain. Chemplate had introduced the use of induction-pinning by optical alignment of innerlayers for multilayer stackup in the early 2000s. This was to go with another innovative way to laminate innerlayers together—the Italian CEDAL resistance-foil vacuum-press, which had some early adopters.
The induction vacuum lamination press (InduBondR X-Press) from Chemplate (Figure 1) is a very compact machine. That stems from its innovative use of magnetic flux to induce heating in the stainless-steel caul plates of the multilayer stackup vs. electric, steam, or hot-oil heating of the press platens.
In the October 2019 edition of PCB007 Magazine1, Victor Lazaro Gallego explained, “The novelty of this new technology, however, is that the thermal energy (heat) to cure the resin composites is produced directly at each of the stainless-steel separator plates that are between each multilayer panel in the press stacks. This thermal energy is transferred at the same time—with the same temperature magnitude and without any thermal conduction delays—to every panel of the lamination press stack. As the energy is induced very homogenously, the heat distribution has the highest uniformity possible in every position and direction of the press stack (X-, Y-, and Z-axes). Therefore, all the layers of laminates inside the press reach the same temperature at the same time; there are no thermal transfer delays. Because the heat is produced only at each stainless-steel separator plate of the stack, the technology can achieve extremely high temperatures and very rapid ramp-up rates with very high energy efficiency.”
Principle of Operation
Electromagnetism is generated when an electric current move through an electrical coil, as is defined by the Biot-Savart Law2. A magnetic field generated on the inside of the coil and looping around the coil perpendicular to the current in the coil is associated with the electric current in the coil.
This phenomenon also works in reverse. When a magnetic field is created by an electric current moving in a coil, an electric current can be made to flow and can induce electric currents in a secondary coil, if the magnetic field is placed in proper alignment to the primary coil.
For a multilayer stackup, the properly aligned stainless-steel caul-plate is working as a one turn coil in a short circuit for the induced currents (Figure 2). The induced magnetic field converts such energy on each stainless-steel separator plate (induced electric energy) into thermal energy (heat) by the eddy current loss theory3.
Saving Energy, Time, and Money
Not having hot, massive platens to heat up and be maintained at high temperatures means that the energy usage is going to be minimized (reported to be ~10% of a hot press) and insulation materials will not be not required, since the separator plates themselves are the source of heat. A dummy panel with the same materials and physical properties as the laminate is embedded with a temperature sensor to track the temperature of the stack in real-time (Figure 3).
Figure 3: The InduBond X-press schematic cross-section view with constructions. (Source: Chemplate)
To better illustrate the efficiency of this new technology, Chemplate took thermography on one of the platens from conventional press technology, and another thermography of the new magnetic press technology (Figure 4). The left side shows the hot platen heat distribution where the platen surface and the sides are hot while the center (press stack) is cooler and needs more time to transfer the heat through the press stack materials. The right side shows that platens are at almost ambient room temperature while the center of the press stack is hot and uniform in temperature.
Energy Efficiency
In the article by Gallego, he provides a detailed analysis of how the induction process requires lower energy, more uniformly distributed and at a faster rate than does conventional press technology. A stackup mass of M2 (4 kg) and M3 (4 kg) heated from room temperature, 25°C (77°F) to 220°C (430°F) with induction energy requires only 702 K-joules, while a hot press with 70 kg platens will require 12,987 K-joules, nearly 18.5 times more energy. With two hot platens, more hot platens will increase the energy load.
The heat transfer is so efficient and uniform that 30 multilayers can be applied to a single opening, vs. the need for multiple daylight openings with smaller stack in conventional lamination (Figure 4).
Profile Programming
The lamination press profile is normally composed of the combination of three different profiles in a unique timeline: temperature, pressure, and vacuum (see controls in Figure 1).
The process engineer or operator creates a temperature profile following what the laminate or prepreg manufacturer recommends on the datasheet of the material. Once this profile is transferred to the InduBond system, the computer, control, temperature sensors, and power driver work together to make the real temperature of the material track the programmed temperature profile very precisely. The software does the same for all other settings, such as vacuum, hydraulic pressure, lamination pressure, and all other process parameters. All the data during the lamination process is logged in a database and associated with a dedicated work order.
Once the heating section of the cycle is over, the vacuum chamber is pressurized. The developed cooling system creates a specific loop of airflow with a specific ?T that crosses through the edges of the press stack separator plates. When the cold air touches the separator stainless steel, energy is exchanged. In other words, the air takes heat from the plates increasing the air temperature while the separator plates become a bit cooler. The air is then pulled by the blowers and conducted to a water/air exchanger that cools down the air again before the blowers push it back to pass through the press stack again. The system recirculates the air inside the chamber.
Summary
Table 1 provides a comparison of electromagnetic inductance lamination with conventional external heating lamination technologies.
References
-
Multilayer Press Technology Using Magnetism to Produce Lamination Heat, by Victor Gallego, PCB007 Magazine, October 2019.
-
Biot-Savart Law, gsu.edu.
-
Eddy Current Loss, circuitglobe.com.
This column originally appeared in the November 2021 issue of PCB007 Magazine.
More Columns from Happy’s Tech Talk
Happy’s Tech Talk #42: Applying Density Equations to UHDI DesignHappy’s Tech Talk #41: Sustainability and Circularity for Electronics Manufacturing
Happy’s Tech Talk #40: Factors in PTH Reliability—Hole Voids
Happy’s Tech Talk #39: PCBs Replace Motor Windings
Happy’s Tech Talk #38: Novel Metallization for UHDI
Happy’s Tech Talk #37: New Ultra HDI Materials
Happy’s Tech Talk #36: The LEGO Principle of Optical Assembly
Happy’s Tech Talk #35: Yields March to Design Rules