RealTime with... American Standard Circuits: Thermal Management
December 16, 2021 | Pete Starkey, I-Connect007Estimated reading time: 3 minutes
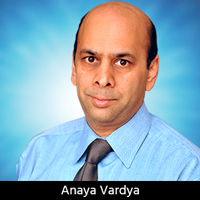
In the third of a series of three RealTime with... American Standard Circuits intervews, I-Connect007 managing editor Nolan Johnson received knowledgeable and informative answers from Anaya Vardya, John Bushie, and Dave Lackey of American Standard Circuits to his questions on the topic of thermal management.
Anaya Vardya began by clarifying the terminology, describing thermal conductivity as a material property defining how quickly heat was transmitted through a piece of that material, whereas thermal management was about analysing the entire system, trying to understand how much heat was being generated, and using appropriate techniques to dissipate that heat as efficiently as possible. On printed circuit boards, straightforward solutions like thermal vias and heavy copper weights could be used for dispersing heat from packages. He invited Dave Lackey and John Bushie to discuss some of the more esoteric techniques.
Johnson asked Lackey to explain the difference between insulated metal substrates and metal-clad PCBs. There was basically none; both design structures involved bonding the PCB to some sort of metal substrate. A simple example was a single-sided circuit board bonded to an aluminium plate with a thermally conductive adhesive material, such as was commonly used to dissipate heat from LEDs. For additional capability, a double-sided PCB with plated through-holes could be used, fabricated on a substrate of FR-4 or thermally conductive laminate, and bonded to an aluminium plate with thermally conductive prepreg.
Another option was to bond circuits on both sides of a metal core, usually aluminium or copper. The two circuits could operate independently or be interconnected by plated-through-holes drilled through insulating plugs in the metal core. Lackey discussed several alternative metal-backed and metal-core alternatives.
Johnson was interested to learn whether multiple functions could be achieved. Bushie picked up this query. In general, with higher levels of integration and more power per unit area, more attention was paid to thermal management using a variety of techniques and materials, combining multiple functions as well as dealing with the heat. Bushie commented on the increasing convergence of RF and digital circuitry in the same design, together with the growing need for thermal management. People were starting to integrate metal cores into these designs, to decrease the overall package size. His example was a multi-function PCB with the control circuitry on one side of the structure and RF circuitry on the other side. Low-loss RF materials, high-speed digital materials, thermally conductive materials, and metal cores were integrated to increase the functional density of the structure. With flexible circuitry being progressively incorporated to minimise connector real-estate and increase reliability by eliminating cables and connectors, all these materials were coming together into a multifunctional circuit board, and what may have been two, three, or four discrete circuit boards could be combined into one smaller package with a higher level of functionality and a variety of circuit structures.
Johnson remarked that with all these dynamics in play—metals, materials, thermal management—designers were faced with difficult choices, maybe for the first time, often with limited experience. He asked Bushie what advice he would offer.
“This starts to sound like an old song...get your fabricator involved!” Bushie responded. “There’s a wealth of knowledge and applications engineering experience at your fabricator; we’re here to help. At the end of the day, we want to help you design something that we can make—rapidly, reliably, and functioning as you wanted it. Feel free to utilise us.”
In 12 minutes, this RealTime with... ASC video combined a primer in thermal management, an indication of how complex a topic it could turn out to be, and a comforting assurance that there is an abundance of support and assistance available to guide the designer through the maze of material selection and structural possibilities, provided that the fabricator is consulted at the beginning of the process rather than expected to sort out the deficiencies of an inferior design when it is presented for manufacture. I enjoyed the experience!
Pete Starkey is an I-Connect007 technical editor.
Visit I-007eBooks to download your copies of American Standard Circuits’ micro eBooks today:
- The Printed Circuit Designer’s Guide to… Fundamentals of RF/ Microwave PCBs
- The Printed Circuit Designer's Guide to... Flex and Rigid-Flex Fundamentals
- The Printed Circuit Designer’s Guide to …Thermal Management: A Fabricator’s Perspective
Suggested Items
The Evolution of Picosecond Laser Drilling
06/19/2025 | Marcy LaRont, PCB007 MagazineIs it hard to imagine a single laser pulse reduced not only from nanoseconds to picoseconds in its pulse duration, but even to femtoseconds? Well, buckle up because it seems we are there. In this interview, Dr. Stefan Rung, technical director of laser machines at Schmoll Maschinen GmbH, traces the technology trajectory of the laser drill from the CO2 laser to cutting-edge picosecond and hybrid laser drilling systems, highlighting the benefits and limitations of each method, and demonstrating how laser innovations are shaping the future of PCB fabrication.
Day 2: More Cutting-edge Insights at the EIPC Summer Conference
06/18/2025 | Pete Starkey, I-Connect007The European Institute for the PCB Community (EIPC) summer conference took place this year in Edinburgh, Scotland, June 3-4. This is the third of three articles on the conference. The other two cover Day 1’s sessions and the opening keynote speech. Below is a recap of the second day’s sessions.
Day 1: Cutting Edge Insights at the EIPC Summer Conference
06/17/2025 | Pete Starkey, I-Connect007The European Institute for the PCB Community (EIPC) Summer Conference took place this year in Edinburgh, Scotland, June 3-4. This is the second of three articles on the conference. The other two cover the keynote speeches and Day 2 of the technical conference. Below is a recap of the first day’s sessions.
Preventing Surface Prep Defects and Ensuring Reliability
06/10/2025 | Marcy LaRont, PCB007 MagazineIn printed circuit board (PCB) fabrication, surface preparation is a critical process that ensures strong adhesion, reliable plating, and long-term product performance. Without proper surface treatment, manufacturers may encounter defects such as delamination, poor solder mask adhesion, and plating failures. This article examines key surface preparation techniques, common defects resulting from improper processes, and real-world case studies that illustrate best practices.
RF PCB Design Tips and Tricks
05/08/2025 | Cherie Litson, EPTAC MIT CID/CID+There are many great books, videos, and information online about designing PCBs for RF circuits. A few of my favorite RF sources are Hans Rosenberg, Stephen Chavez, and Rick Hartley, but there are many more. These PCB design engineers have a very good perspective on what it takes to take an RF design from schematic concept to PCB layout.