-
- News
- Books
Featured Books
- pcb007 Magazine
Latest Issues
Current IssueInventing the Future with SEL
Two years after launching its state-of-the-art PCB facility, SEL shares lessons in vision, execution, and innovation, plus insights from industry icons and technology leaders shaping the future of PCB fabrication.
Sales: From Pitch to PO
From the first cold call to finally receiving that first purchase order, the July PCB007 Magazine breaks down some critical parts of the sales stack. To up your sales game, read on!
The Hole Truth: Via Integrity in an HDI World
From the drilled hole to registration across multiple sequential lamination cycles, to the quality of your copper plating, via reliability in an HDI world is becoming an ever-greater challenge. This month we look at “The Hole Truth,” from creating the “perfect” via to how you can assure via quality and reliability, the first time, every time.
- Articles
- Columns
- Links
- Media kit
||| MENU - pcb007 Magazine
Estimated reading time: 6 minutes
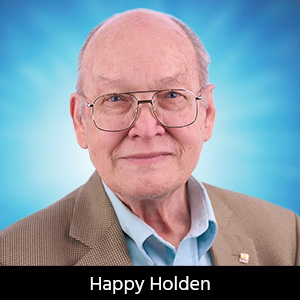
Contact Columnist Form
Happy's Tech Talk #3: Photonic Soldering
Printed electronics (PE) continues to be a growing technology. But one of its advantages, as well as a drawback, is that low-cost substrates, like paper, cannot take the temperature of solder paste reflow. Also, the inks need to be cured. One current way to cure the printed inks is with ultraviolet radiation curing, such as that used with solder mask or legend inks.
One innovation is the curing or annealing of printed inks with flash tubes, which produce a high-intensity, broad-spectrum white light as seen in Figure 1.1 You might be familiar with the technology from photography, as electronic flash or strobes. But these, on the other hand, are much larger and much higher in power. You have probably noticed from photography that these electronic flashes produce heat. But this heat is limited to the surface only, so that the inks can be cured or annealed but the substrate remains cool.
Inks cured to the temperature at which they become conductive using IR ovens requires substrates that can withstand these temperatures, like polyimides, ceramics, and epoxy fiberglass. The flash tube’s white light is not drying with temperature; it is drying with the high energy density of electromagnetic radiation (ER). The ER rays penetrate deep into the layer to be dried and excite the molecules there.
The absorption of the energy happens in a few tenths of a second. The molecular activation vaporizes the solvent or water. Because the radiation energy penetrates deep into the layer, it couples to the pigments and dries them from the inside out, and the undesirable effects on the surface such as bubble formation or blistering do not occur. In addition, ER light can be dosed and applied in a very targeted manner, right to the point.
With this innovative technology, highly conductive patterns, components (resistors/capacitors) and insulators can be cured on substrates like papers, fabrics, or plastics, all in less than a few hundred milliseconds.2 Printing technologies as well as ink types are detailed in Chapter 11 of Flexible Circuit Technology, 4th Edition.3
Photonic Soldering and Sintering
Table 1 provides an outline of different selective soldering techniques organized by how the thermal load is delivered. In these conventional cases, the exposure is confined to the heating area to ensure lower thermal load on the temperature-sensitive parts of the device. Since the heating medium is confined and will need to be moved from one area to another, the speed of processing with these techniques is typically slow.
Light-generated (ER) heating, as in laser soldering, can also be performed by flash tubes, but with the advantage of soldering components not in the line-of-sight. The first of these new soldering systems is PulseForge, developed by NovaCentrix.
With the use of 500-volt power supplies of 30 to 40 KW capability attached to banks of high-voltage storage capacitors and controlled by high-voltage circuits, specially designed flash tubes can now perform the standard lead-free reflow in just seconds and with power usage just 10% of standard reflow ovens.
Figure 2 shows that light-absorbing materials will heat during the light pulse, and cool immediately when the light is removed. Although this is possible to solder with just one pulse, the superior process is to use a pulse-train of pulses (with differing pulse duration and power) so as not to overheat the substrate.
Thermal Profile
The photonic soldering process builds on the process of using high-intensity flashes of broad-spectrum light to heat up a multi-layered stack in a non-equilibrium process. This process was developed as part of enhancing the manufacturability of flexible hybrid electronics (FHE) by sintering metal particle-based inks into conductive traces.
The photonic soldering tools rely on extremely high average power delivery for a xenon gas-filled flash lamp. As such, flash lamps must be water-cooled to prevent runaway heating and detrimental damage to the system under high-duty use. Additionally, the flash lamp system needs to have digital controls to adjust for soldering of different-sized components under various thermal conditions.
SAC-305 (Indium 8.9HF, type 4) solder paste was manually stencil-printed on the copper contact pads. Wet thickness of the applied solder paste was roughly 75 µm. Sulfur-tolerant chip resistors in 0603 packages from Rohm Semiconductors (part number SFR03) were used as the main component (Figure 3).
Areas which absorb parts of the spectrum more efficiently convert the light energy to thermal energy more effectively than other areas and result in a localized temperature increase. The temperature profile of the material being processed can be controlled by varying the timing of the pulses (pulse length and delay between subsequent pulses). The temperature reached can be above the rated temperature of constituent parts of the device stack without damaging them, in part because the heating is noticeably short, and the device stack will revert to ambient conditions soon after the light illumination has stopped.
The soldering process (Figure 3) shows the ideal trade-off between light power density and flash durations. The soldering is accomplished from one to four seconds depending on power density. Power settings from P1 to P9 will induce reflow from 4.5 to 8 seconds, with the shortest at P9 of 0.5 seconds.
Spatial Selectivity
The photonic soldering process is unique and provides a soldering process for a given material system (substrate, conducting track, solder, and component) that cannot be duplicated in a normal reflow oven. The average power is a function of the energy of a single light pulse (depends on the voltage to which capacitor banks are charged and the length of time for which they are discharged) and the frequency at which light pulses are incident on the material system. Average power is the critical control over the temperature ramp rate achievable for the device stack. While certain device structures can be soldered with extremely high ramp rate, others require a slower ramp rate to preserve device structure and prevent uncontrollable outgassing. The temperature range can be controlled by spatial selectivity for:
- Thermally-sensitive substrates like LED arrays on PET
- Thermally-sensitive components like batteries or displays using an aluminum mask with laser-cut openings
- Thermally-sensitive regions like the reflow under a BGA with conductive heating
- Thermally-sensitive solder joints like SAC305 reflow in 0.375 seconds
- Reliability-sensitive lead-free solder joints where the short heating time minimizes intermetallics
- When low voids are required,
For the same structure, the peak temperatures can be manipulated either by increasing the ramp rate, exposure time, or a combination of both (Figure 4). Like standard reflow mechanism, each change provides a different opportunity in optimizing the solder joint quality. For the explored device structure, at an average incident power density of 16 W/cm2, reflow of the solder can be observed starting at 1.5 seconds but will improve the joint quality up to three seconds as reflected through improved fillet shape and intermetallic formation. At five seconds of exposure, we start to observe mechanical failure and buckling of the flex circuit. Figure 5 shows an interior of the photonic soldering equipment. This equipment (Figure 6) comes in a batch and conveyorized unit. A complete automated assembly line of paste-inspection-placement-soldering would be only 21 feet long and have a processing time of only three to four minutes.
Summary
This new soldering process can accommodate a substrate up to 300 x 400 mm with R2R possible. The new opportunities now possible are:
- Use high-temperature solders for comparable quality
- SAC-305, SnSb, etc.
- Use of temperature-sensitive substrates for lower costsSolder multiple sized components at once
- PET, TPU, PVC, PPE, PEI, PVF, PEN, etc.
- Potential for R2R handling
- Achieve comparable results to reflow ovens but much faster
- Works equally as well with FR-4 and other traditional boards but with a smaller footprint
- Allows soldering on aluminum
- Will work with no direct line-of-sight
- Provides soldering on curved surfaces
- Provides flexible/alternative product design options
- No thermal stress on stacked microvias
- Lower energy requirements
- Selective control of soldering parameters
- Optional N2 processing area
References
- “Use of Flash Lamps to Achieve Non-Equilibrium Soldering and Assembly Utilizing Conventional SAC Alloys,” by Vahid Akhavan, SMTA-International 2020 Proceedings #567, Chicago, Sept. 2020.
- “PulseForge Flash Lamp Soldering using Conventional Soldering Alloys,” by Rick Larson, SMTA Boston/Nutmeg Webinar, Sept. 14, 2021.
- Flexible Circuit Technology, 4th Edition, by Joseph Fjelstad.
- “Photonic Soldering Temperature Sensitive Components with High Temperature Solder Alloys,” Vahid Akhavan, #950, Proceedings of the 2021 SMTAI Conference, Minneapolis, Minnesota.
This column originally appeared in the December 2021 issue of PCB007 Magazine.
More Columns from Happy’s Tech Talk
Happy’s Tech Talk #42: Applying Density Equations to UHDI DesignHappy’s Tech Talk #41: Sustainability and Circularity for Electronics Manufacturing
Happy’s Tech Talk #40: Factors in PTH Reliability—Hole Voids
Happy’s Tech Talk #39: PCBs Replace Motor Windings
Happy’s Tech Talk #38: Novel Metallization for UHDI
Happy’s Tech Talk #37: New Ultra HDI Materials
Happy’s Tech Talk #36: The LEGO Principle of Optical Assembly
Happy’s Tech Talk #35: Yields March to Design Rules