-
-
News
News Highlights
- Books
Featured Books
- pcb007 Magazine
Latest Issues
Current IssueThe Hole Truth: Via Integrity in an HDI World
From the drilled hole to registration across multiple sequential lamination cycles, to the quality of your copper plating, via reliability in an HDI world is becoming an ever-greater challenge. This month we look at “The Hole Truth,” from creating the “perfect” via to how you can assure via quality and reliability, the first time, every time.
In Pursuit of Perfection: Defect Reduction
For bare PCB board fabrication, defect reduction is a critical aspect of a company's bottom line profitability. In this issue, we examine how imaging, etching, and plating processes can provide information and insight into reducing defects and increasing yields.
Voices of the Industry
We take the pulse of the PCB industry by sharing insights from leading fabricators and suppliers in this month's issue. We've gathered their thoughts on the new U.S. administration, spending, the war in Ukraine, and their most pressing needs. It’s an eye-opening and enlightening look behind the curtain.
- Articles
- Columns
- Links
- Media kit
||| MENU - pcb007 Magazine
The Materials Connection
March 16, 2022 | Nolan Johnson, I-Connect007Estimated reading time: 2 minutes
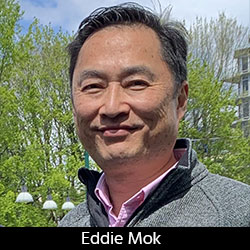
Recently, Eddie Mok, product innovation development AVP at WUS, talked with us at length about the state of the materials market from the perspective of a fabricator. In this excerpt from the conversation, Eddie details some example interactions between what materials, design, and manufacturing bring to the ultimate goal of meeting your design specifications and manufacturing costs. It is clear from this conversation that materials and technology are increasingly interconnected.
Nolan Johnson: Eddie, what’s your background?
Eddie Mok: I’ve been with WUS for 16 years, and before that I was at Nelco for 15 years. I’m still working with materials, but I’m applying it now. While materials are changing, there’s room for more. And, because of emerging advanced technology, such as VeCS and others in development, that’s where we realize that we still need all the material manufacturers to offer our customers innovative PCB solutions, plus we need different versions of the material to support the new fabrication methods. And yet, material alone is not enough.
Johnson: VeCS is a great example of innovative developments in fab. Besides additive technologies, of course. Happy Holden has been saying, “This is the next thing. This is the thing that’s going to replace HDI. This gives a lot of capability to designers.”
Mok: I’ve been saying something similar to customers, “Imagine when HDI came along 25 years ago and people said, “What is that? It’s too expensive. It doesn’t work.” Over time and refinement, HDI established itself as a key technology. Now, hopefully, VeCS is another type of interconnect solution that causes the next paradigm shift. We seem to be getting a lot of traction.
There’s another approach called a 3DMD stackup risk analysis tool, which is also a good example. These are standard/routine solutions at WUS. Signal integrity, rougher or smoother copper, better material— that’s pretty routine, as you say, with respect to material selection—but what we want to offer is crosstalk mitigation, improved shielding, and so on by innovative interconnect solutions. The advanced capability, value engineering cost, material performance, and stackup risk—it’s all there and of interest to today’s designers and fabricators.
I get to talk a lot about material, but because of the advanced capabilities requirements, those conversations lead us in many different directions. For example, when you exhaust standard plated through-hole (PTH) back drill technology, you have to go to HDI build-up with multiple lamination designs, or change your design to more costly structures like buried or blind via structures.
Johnson: Eddie, this is a symbiotic situation, isn’t it? You have advanced techniques driving materials and materials driving advanced techniques.
Mok: Yes, so many things are happening. These are where most of our activities are. We’re constantly looking at different class 8 material (ultra-super low loss grade), for example.
Johnson: This is for your long-tail legacy work?
Mok: Yes. But that’s also where we can’t separate material with technology. You can’t buy a Ferrari and equip it with budget tires. Customers today will share that they plan to rely on the material to minimize insertion loss. But I make sure to ask them, “What about your shielding? What about your crosstalk? That can’t be done by material alone; the interconnect structure needs to help with this.”
To read this entire conversation, which appeared in the March 2022 issue of PCB007 Magazine, click here.
Suggested Items
The Evolution of Picosecond Laser Drilling
06/19/2025 | Marcy LaRont, PCB007 MagazineIs it hard to imagine a single laser pulse reduced not only from nanoseconds to picoseconds in its pulse duration, but even to femtoseconds? Well, buckle up because it seems we are there. In this interview, Dr. Stefan Rung, technical director of laser machines at Schmoll Maschinen GmbH, traces the technology trajectory of the laser drill from the CO2 laser to cutting-edge picosecond and hybrid laser drilling systems, highlighting the benefits and limitations of each method, and demonstrating how laser innovations are shaping the future of PCB fabrication.
Day 2: More Cutting-edge Insights at the EIPC Summer Conference
06/18/2025 | Pete Starkey, I-Connect007The European Institute for the PCB Community (EIPC) summer conference took place this year in Edinburgh, Scotland, June 3-4. This is the third of three articles on the conference. The other two cover Day 1’s sessions and the opening keynote speech. Below is a recap of the second day’s sessions.
Day 1: Cutting Edge Insights at the EIPC Summer Conference
06/17/2025 | Pete Starkey, I-Connect007The European Institute for the PCB Community (EIPC) Summer Conference took place this year in Edinburgh, Scotland, June 3-4. This is the second of three articles on the conference. The other two cover the keynote speeches and Day 2 of the technical conference. Below is a recap of the first day’s sessions.
Preventing Surface Prep Defects and Ensuring Reliability
06/10/2025 | Marcy LaRont, PCB007 MagazineIn printed circuit board (PCB) fabrication, surface preparation is a critical process that ensures strong adhesion, reliable plating, and long-term product performance. Without proper surface treatment, manufacturers may encounter defects such as delamination, poor solder mask adhesion, and plating failures. This article examines key surface preparation techniques, common defects resulting from improper processes, and real-world case studies that illustrate best practices.
RF PCB Design Tips and Tricks
05/08/2025 | Cherie Litson, EPTAC MIT CID/CID+There are many great books, videos, and information online about designing PCBs for RF circuits. A few of my favorite RF sources are Hans Rosenberg, Stephen Chavez, and Rick Hartley, but there are many more. These PCB design engineers have a very good perspective on what it takes to take an RF design from schematic concept to PCB layout.