-
-
News
News Highlights
- Books
Featured Books
- pcb007 Magazine
Latest Issues
Current IssueThe Hole Truth: Via Integrity in an HDI World
From the drilled hole to registration across multiple sequential lamination cycles, to the quality of your copper plating, via reliability in an HDI world is becoming an ever-greater challenge. This month we look at “The Hole Truth,” from creating the “perfect” via to how you can assure via quality and reliability, the first time, every time.
In Pursuit of Perfection: Defect Reduction
For bare PCB board fabrication, defect reduction is a critical aspect of a company's bottom line profitability. In this issue, we examine how imaging, etching, and plating processes can provide information and insight into reducing defects and increasing yields.
Voices of the Industry
We take the pulse of the PCB industry by sharing insights from leading fabricators and suppliers in this month's issue. We've gathered their thoughts on the new U.S. administration, spending, the war in Ukraine, and their most pressing needs. It’s an eye-opening and enlightening look behind the curtain.
- Articles
- Columns
- Links
- Media kit
||| MENU - pcb007 Magazine
An Inside Look at an Indian PCB Manufacturer
March 24, 2022 | Dan Beaulieu, D.B. Management GroupEstimated reading time: 10 minutes
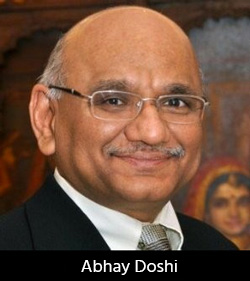
As a student of the printed circuit board industry, I am always interested in learning more about companies all over the world. When I connected with Abhay Doshi, managing director of Fine-Line Circuits Ltd. in India, I welcomed the opportunity to learn more about him, his company, and the Indian PCB business as a whole—it was all that, and so much more. Here’s what I learned.
Dan Beaulieu: Abhay, thanks for talking with me. I truly appreciate it.
Abhay Doshi: No problem, Dan, I am looking forward to it as well.
Beaulieu: Tell me about your company, when and why was it started. In other words, what is the Fine-Line India story?
Doshi: The decision to start the company was in 1989. We set up the facility with the equipment and the team in 1990, started production in 1991, and by 1992 we were listed on the Bombay Stock Exchange.
Beaulieu: Who was involved in starting the company?
Doshi: The company was started by my family, the Doshi family, in 1989. But we were not alone, we benefitted greatly from three gentlemen who have played a key role since the first beginning in 1989. They are Vijay Kumbhani, G. Sudarsanam and Joy Chacko, to whom we are perpetually grateful. We are also very proud of our great team of strong and competent managers who I would have to say have been the pillars of our business from the very beginning.
Beaulieu: What was the plan when you started the company?
Doshi: Originally, we needed to bring more foreign money into India at that time and we thought that one way to do it was to increase our exports to other countries which would also give us as we call it here “a government tail wind.” I had a background in electronics from my time in the United States where I had received an MBA from Berkeley and had worked with a company called Maxtor, a disk drive manufacturer in San Jose. So, with that experience I thought that an electronics company would be the right fit for exporting products to other parts of the world.
We also knew that we always wanted to build and manufacture products, and I have to say, that having lived and worked globally gave us global ambitions.
Beaulieu: That’s interesting as well as logical. What was the vision for the company when you started it? What was the “why” for founding Fine-Line India?
Doshi: We believed that the electronic component industry would always thrive and so believed that this would create a bright future for us. We chose printed circuit boards because, in many ways, it is the most essential component and unlikely to go obsolete. It all starts with the board; without the board where will the components go? We felt that there would be a global demand for PCBs and, as always, we had that global vision. So, we set up our PCB facility in India’s foremost export zone, Seepz, in Mumbai. We sold our first boards to a Florida-based audio company in 1991.
Beaulieu: And you have been there ever since?
Doshi: Yes, and we have grown periodically, adding adjacent space to the facility as needed.
Beaulieu: I can see that you have grown steadily since then.
Doshi: Yes. We have always strived to be the very best in the industry. In fact, we have some goals of doing business such as:
- Competing in the global arena.
- Providing uncompromising quality.
- Having the best processes.
- Using the very best materials.
- Offering service standards that exceed all businesses, even the hospitality business.
- Providing crystal clear communication.
- Acting on our fervent desire to always underpromise and overdeliver.
Beaulieu: Your last point is something I always say as well. Please talk a little bit about being a family business. What is that like?Page 1 of 2
Suggested Items
The Evolution of Picosecond Laser Drilling
06/19/2025 | Marcy LaRont, PCB007 MagazineIs it hard to imagine a single laser pulse reduced not only from nanoseconds to picoseconds in its pulse duration, but even to femtoseconds? Well, buckle up because it seems we are there. In this interview, Dr. Stefan Rung, technical director of laser machines at Schmoll Maschinen GmbH, traces the technology trajectory of the laser drill from the CO2 laser to cutting-edge picosecond and hybrid laser drilling systems, highlighting the benefits and limitations of each method, and demonstrating how laser innovations are shaping the future of PCB fabrication.
Day 2: More Cutting-edge Insights at the EIPC Summer Conference
06/18/2025 | Pete Starkey, I-Connect007The European Institute for the PCB Community (EIPC) summer conference took place this year in Edinburgh, Scotland, June 3-4. This is the third of three articles on the conference. The other two cover Day 1’s sessions and the opening keynote speech. Below is a recap of the second day’s sessions.
Day 1: Cutting Edge Insights at the EIPC Summer Conference
06/17/2025 | Pete Starkey, I-Connect007The European Institute for the PCB Community (EIPC) Summer Conference took place this year in Edinburgh, Scotland, June 3-4. This is the second of three articles on the conference. The other two cover the keynote speeches and Day 2 of the technical conference. Below is a recap of the first day’s sessions.
Preventing Surface Prep Defects and Ensuring Reliability
06/10/2025 | Marcy LaRont, PCB007 MagazineIn printed circuit board (PCB) fabrication, surface preparation is a critical process that ensures strong adhesion, reliable plating, and long-term product performance. Without proper surface treatment, manufacturers may encounter defects such as delamination, poor solder mask adhesion, and plating failures. This article examines key surface preparation techniques, common defects resulting from improper processes, and real-world case studies that illustrate best practices.
RF PCB Design Tips and Tricks
05/08/2025 | Cherie Litson, EPTAC MIT CID/CID+There are many great books, videos, and information online about designing PCBs for RF circuits. A few of my favorite RF sources are Hans Rosenberg, Stephen Chavez, and Rick Hartley, but there are many more. These PCB design engineers have a very good perspective on what it takes to take an RF design from schematic concept to PCB layout.