-
- News
- Books
Featured Books
- pcb007 Magazine
Latest Issues
Current IssueSales: From Pitch to PO
From the first cold call to finally receiving that first purchase order, the July PCB007 Magazine breaks down some critical parts of the sales stack. To up your sales game, read on!
The Hole Truth: Via Integrity in an HDI World
From the drilled hole to registration across multiple sequential lamination cycles, to the quality of your copper plating, via reliability in an HDI world is becoming an ever-greater challenge. This month we look at “The Hole Truth,” from creating the “perfect” via to how you can assure via quality and reliability, the first time, every time.
In Pursuit of Perfection: Defect Reduction
For bare PCB board fabrication, defect reduction is a critical aspect of a company's bottom line profitability. In this issue, we examine how imaging, etching, and plating processes can provide information and insight into reducing defects and increasing yields.
- Articles
- Columns
- Links
- Media kit
||| MENU - pcb007 Magazine
Estimated reading time: 7 minutes
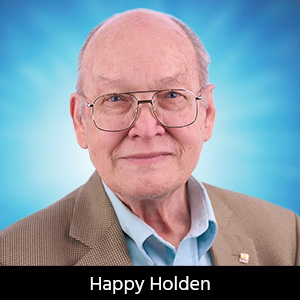
Contact Columnist Form
Happy's Tech Talk #7: Next Generation Application Specific Modules
Introduction
In 1965, Gordon Moore predicted that the number of transistors that could be packaged into a square inch of space would double every year for the near future.1 Although his projection was later revised to every 18 months, “Moore’s Law” has withstood the test of time for five decades. Today, we are beginning to see obstacles to this type of exponential growth due to the inherent limits associated with silicon lithography, packaging of the devices, and component placement on PCBs.
A new electronics packaging method known as application specific electronics package (ASEP)2 has been developed for applications in the growing electric vehicle (EV) market. The technology enables the integration of PCBs, connectors, and high-current conductors, as well as active and passive components, into a single device. ASEP assemblies can have multilayer circuitry and three-dimensional features. They can be inherently hermetically sealed, manufactured with thermally conductive resins that are effective in dissipating heat, and designed in such a way to benefit from the high conductivity of metal to carry high currents and heat, making the process an ideal solution for assemblies that must withstand elevated temperatures, high currents, and harsh environments.
ASEP Manufacturing
New and smarter ways of manufacturing electronics, as well as better ways to dissipate the heat being generated, must be developed for the electronics industry to continue a robust growth trajectory. ASEP is an additive
manufacturing process that builds up the conductive patterns on the surface of the plastic substrate, as opposed to etching away the copper on a PCB.
Thermoplastic ASEP substrates can also be remelted and reused. Figure 1 shows the basic process steps for ASEP manufacturing. A list of the process steps is as follows:
- Stamp metal carrier
- Insert mold plastic substrate
- Lasers modify the surface
- Inkjet print nanoparticle conductors
- Sinter to make the traces conductive
- Electroplate with Cu and additional metals
- Inkjet print solder mask
- Dispense or screen solder paste
- Pick and place components and reflow
- Singulate
- Place into final assembly housing
The novel ASEP is small enough to offer the modularity that EVs will need to function effectively. The example illustrated in Figure 2 has both a microprocessor and network, along with high-voltage and high-power devices needed to control the new EV motors.
High current and high voltage, accompanied by the heat generated by the power devices, are becoming a significant challenge in the automotive, commercial vehicle, and industrial equipment industries. The ASEP module is 58% smaller and 22% lighter with 25% improvement in current capacity at 110°C than a printed circuit board. Typically, power control electronics have been made with “thick copper” PCBs, where copper traces are between 75 and 200 microns thick. Even with these copper thicknesses, they have not been very efficient in conducting high current as well as high voltages while managing the heat when compared to thicker stamped Cu alloys which may be up to several millimeters thick.
The ASEP process starts with a stamped metal carrier which is over-molded with a high temperature substrate. A nanoparticle ink is used to print the patterns and then the traces are electroplated with conventional metals commonly used in the PCB industry (Figure 2). A solder mask is applied and then components are reflowed onto the ASEP assembly.
The stamped metal carrier within the ASEP assembly serves multiple crucial functions in the manufacture of the product. The substrate is a way to carry the ASEP assembly through the manufacturing process steps as well as the electrical contact for the connector features of the ASEP assembly. In addition, the substrate serves as a method to transfer the heat generated by the components placed onto the ASEP assembly and provides a path to carry high current that would otherwise be impossible to carry within a conventional PCB assembly.
For higher density electronic packages, a two-sided reel-to-reel manufactured polyimide flexible circuit either replaces or is integrated with the stamped metal carrier, creating up to five layers of circuitry. This type of ASEP packaging would be used to design miniaturized consumer electronics, sensors, medical devices, and small wearable devices. For high temperature applications, a thermally conductive substrate such as a liquid crystal polymer (LCP) is used; it effectively becomes a heat sink or spreader, reducing the temperatures of the heat-generating components.
After the stamped metal carrier has been over-molded with an LCP substrate, a laser is used to define the circuit patterns on the surfaces of the substrate. Since all the 3D features such as vias, recesses, or cavities have been molded into the substrate, the laser must be able to image the pattern in three dimensions. After the patterns have been laser marked, an inkjet printer deposits a thin conductive layer of metal onto the traces that were defined by the laser.
ASEP Attributes, Features, and Performance
By integrating the functionality of a PCB, connector, and thermal management features, ASEP combines the functions into a single device which will be smaller, lighter, and more efficient. Because the process is fully additive, new SAP processes will be able to provide fine traces and spaces. Advantages are that ASEP applications can be made to be inherently hermetically sealed. The combination of these advantages should result in very cost-effective electronic solutions.
Figure 3 shows an ASEP package without components. The package, called ASEP microPDB (micro power distribution box), adds additional power switching and circuit protection to the vehicle’s wiring architecture. The two high-current electrical paths for the field effect transistor (FET) in the lower bottom corner of the device are extensions of the actual metal contacts. Therefore, the FET (in Figure 4) is soldered directly to the 800-micron thick Cu alloy; the resulting electrical and thermal path has been optimized. This reduces the resistance in the system (reduces heat generated) and reduces the resistance in the thermal path to remove the heat from the device very efficiently. Furthermore, the ASEP material used for the application can be a thermally conductive plastic (such as LCP) which spreads the heat generated by the FET. In effect, the ASEP material itself can be the heat sink or spreader, making it possible to reduce the temperature of the heat-generating devices.
The ASEP microPDB is a power control device that looks very much like an automotive connector (Figure 4) but within it a microprocessor and FET provide local interconnect network (LIN) control and high-current solid-state switching that are highly reliable, self-protecting, and cost effective in comparison with a current microPDB containing a relay and fuses (as seen in Figure 5). The microprocessor provides LIN control which eliminates the need to run control lines to each device.
Electrical, Thermal, and Mechanical Testing
Three main tests were performed to evaluate the electrical, thermal, and mechanical performance of the ASEP microPDB. First, temperature rise testing was performed on the package. The ASEP microPDB was powered with 12 volts from 0 amps to shutdown in 5A intervals and 30-minute intervals. Thermocouples were attached to the microprocessor and the FET to measure the temperatures. Tests were conducted at both 85°C and 110°C ambient. According to specification, the temperature rise should not exceed 55°C above the ambient temperature. In addition to the temperature rise test, both thermal shock and vibration tests were performed according to USCAR 2 revision 6 specification.3
The results show that the ASEP microPDB can carry 50 amps of current at 110°C ambient. The package shuts down at higher currents as the temperature rises more than 55°C above ambient. In addition to a thermal test, the ASEP assembly met all the requirements of the vibration and thermal shock tests.
Table 1 provides a comparison between the size and weight of a PCB microPDB design currently in production and the ASEP microPDB design. The ASEP microPDB is 58% smaller and 22% lighter with an improved current capability at higher temperatures.
Conclusion
ASEP is a design and manufacturing process that allows the industry to take advantage of the latest injection moldable plastics along with the proven ability of conductive metal frames to remove heat, carry high currents, and to provide reliable electrical interconnects.
The technology is ideal for a modular approach to control in electric vehicles where the control is distributed by its network but there is a need for high current or high voltage while providing cooling for a long-lived, reliable system control.
References
- “Progress in digital integrated electronics,” by G.E. Moore, Digest of the 1975 International Electron Devices Meeting, pp. 11–13. Washington, D.C.
- “ASEP (Application Specific Electronics Package), a Next Generation Electronics Manufacturing Technology,” by Victor Zaderej and Richard Fitzpatrick, Molex; Babak Afraei, Ford Motor Company, Proceedings of SMTA International, October 2018, Rosemont, Illinois.
- Performance Specification for Automotive Electrical Connector Systems, USCAR-2 revision 6.
This column originally appeared in the April 2022 issue of PCB007 Magazine.
Happy Holden has worked in printed circuit technology since 1970 with Hewlett-Packard,?NanYa?Westwood, Merix, Foxconn, and Gentex. He is currently a contributing technical editor with I-Connect007, and the author?of? Automation and Advanced Procedures in PCB Fabrication, and 24 Essential Skills for Engineers. To contact Holden or read past columns, click here.
More Columns from Happy’s Tech Talk
Happy’s Tech Talk #40: Factors in PTH Reliability—Hole VoidsHappy’s Tech Talk #39: PCBs Replace Motor Windings
Happy’s Tech Talk #38: Novel Metallization for UHDI
Happy’s Tech Talk #37: New Ultra HDI Materials
Happy’s Tech Talk #36: The LEGO Principle of Optical Assembly
Happy’s Tech Talk #35: Yields March to Design Rules
Happy’s Tech Talk #34: Producibility and Other Pseudo-metrics
Happy’s Tech Talk #33: Wet Process Management and Control