-
-
News
News Highlights
- Books
Featured Books
- pcb007 Magazine
Latest Issues
Current IssueThe Hole Truth: Via Integrity in an HDI World
From the drilled hole to registration across multiple sequential lamination cycles, to the quality of your copper plating, via reliability in an HDI world is becoming an ever-greater challenge. This month we look at “The Hole Truth,” from creating the “perfect” via to how you can assure via quality and reliability, the first time, every time.
In Pursuit of Perfection: Defect Reduction
For bare PCB board fabrication, defect reduction is a critical aspect of a company's bottom line profitability. In this issue, we examine how imaging, etching, and plating processes can provide information and insight into reducing defects and increasing yields.
Voices of the Industry
We take the pulse of the PCB industry by sharing insights from leading fabricators and suppliers in this month's issue. We've gathered their thoughts on the new U.S. administration, spending, the war in Ukraine, and their most pressing needs. It’s an eye-opening and enlightening look behind the curtain.
- Articles
- Columns
- Links
- Media kit
||| MENU - pcb007 Magazine
Additive Manufacturing Requires Additive Design Techniques
May 9, 2022 | Luca Gautero, SUSS MicroTecEstimated reading time: 2 minutes
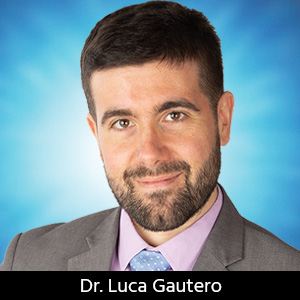
Although I am not a designer by trade, I want to share my thoughts on what additive manufacturing means for designers, especially how it relates to solder mask. I feel the following topics are the most important to address.
1. Definition of Solder Mask
By its nature, the definition provided by any EDA tool is a negative one; the CAM vector files specify what goes away from an assumed continuous surface. Until now, solder mask has always presented itself as subtractive. SUSS MicroTec developed a front end, JETxSMFE, that can operate at the CAM station to smooth out manufacturing. The software understands all of this, managing the details correctly on the incoming files.
2. The Advantage of Inkjet Solder Mask
One advantage of inkjet solder mask is to avoid any filling of holes or vias. Another way, maybe an annoyance to some, is to say that “tenting” is not possible. Still, the consensus is that solder mask-free vias improve a board’s reliability (Figure 1). The JETxSMFE removes solder mask at declared holes. Undeclared drills, which might still exist depending on the manufacturing convention on the production floor, will result in ink on the print table. This is not a big issue as a scraper easily removes excess solder mask, and alternatively, replacing the table or its liner (if present) gets the job done. However, both solutions lead to a small downtime. Long story short, if you want friends on the shop floor, be sure to have all the drills in your design.
3. The Dam Dogma
These small solder mask traces on laminate are supposed to separate two nearby copper pads. Such a pattern indicates the non-solder mask defined (NSMD) pad design choice. However, this choice involves several constraints, and these create an artificial need for narrow dams. From my earlier example, this time with numbers: Imagine two pads, 200 µm apart, nothing extreme. What is the maximum size of a dam between these two? Assuming that LDI technology is used, the dam size results from applying the state-of-the-art constraint of the technology. This 200 µm pitch decreases by the laser beam width plus the registration accuracy twice—one for each pad. Therefore, it quickly comes down to 100 µm. Any more challenging a pad distance will also make it harder to define a dam.
From this reasoning, the many requests to create 50 µm dams or less with traditional technology seem legitimate. So, what do we do with inkjet printing? Does it join the race to the last micrometer?
To find out the answers, continue reading this article in the April 2022 issue of Design007 Magazine.
Suggested Items
Driving Innovation: Direct Imaging vs. Conventional Exposure
07/01/2025 | Simon Khesin -- Column: Driving InnovationMy first camera used Kodak film. I even experimented with developing photos in the bathroom, though I usually dropped the film off at a Kodak center and received the prints two weeks later, only to discover that some images were out of focus or poorly framed. Today, every smartphone contains a high-quality camera capable of producing stunning images instantly.
Hands-On Demos Now Available for Apollo Seiko’s EF and AF Selective Soldering Lines
06/30/2025 | Apollo SeikoApollo Seiko, a leading innovator in soldering technology, is excited to spotlight its expanded lineup of EF and AF Series Selective Soldering Systems, now available for live demonstrations in its newly dedicated demo room.
Indium Corporation Expert to Present on Automotive and Industrial Solder Bonding Solutions at Global Electronics Association Workshop
06/26/2025 | IndiumIndium Corporation Principal Engineer, Advanced Materials, Andy Mackie, Ph.D., MSc, will deliver a technical presentation on innovative solder bonding solutions for automotive and industrial applications at the Global Electronics A
Fresh PCB Concepts: Assembly Challenges with Micro Components and Standard Solder Mask Practices
06/26/2025 | Team NCAB -- Column: Fresh PCB ConceptsMicro components have redefined what is possible in PCB design. With package sizes like 01005 and 0201 becoming more common in high-density layouts, designers are now expected to pack more performance into smaller spaces than ever before. While these advancements support miniaturization and functionality, they introduce new assembly challenges, particularly with traditional solder mask and legend application processes.
Knocking Down the Bone Pile: Tin Whisker Mitigation in Aerospace Applications, Part 3
06/25/2025 | Nash Bell -- Column: Knocking Down the Bone PileTin whiskers are slender, hair-like metallic growths that can develop on the surface of tin-plated electronic components. Typically measuring a few micrometers in diameter and growing several millimeters in length, they form through an electrochemical process influenced by environmental factors such as temperature variations, mechanical or compressive stress, and the aging of solder alloys.