-
-
News
News Highlights
- Books
Featured Books
- pcb007 Magazine
Latest Issues
Current IssueThe Hole Truth: Via Integrity in an HDI World
From the drilled hole to registration across multiple sequential lamination cycles, to the quality of your copper plating, via reliability in an HDI world is becoming an ever-greater challenge. This month we look at “The Hole Truth,” from creating the “perfect” via to how you can assure via quality and reliability, the first time, every time.
In Pursuit of Perfection: Defect Reduction
For bare PCB board fabrication, defect reduction is a critical aspect of a company's bottom line profitability. In this issue, we examine how imaging, etching, and plating processes can provide information and insight into reducing defects and increasing yields.
Voices of the Industry
We take the pulse of the PCB industry by sharing insights from leading fabricators and suppliers in this month's issue. We've gathered their thoughts on the new U.S. administration, spending, the war in Ukraine, and their most pressing needs. It’s an eye-opening and enlightening look behind the curtain.
- Articles
- Columns
- Links
- Media kit
||| MENU - pcb007 Magazine
Exploring High Density With Axiom
May 6, 2022 | I-Connect007 Editorial TeamEstimated reading time: 3 minutes
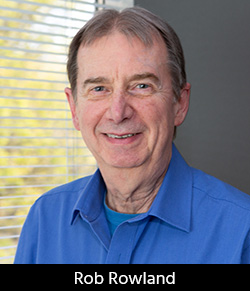
Nolan Johnson and Barry Matties talk with Axiom’s Rob Rowland and Kevin Bennett about the current high-density challenges facing EMS manufacturing. In this interview, Bennett and Rowland zero in on component packaging and feeder technology as critical areas in need of improvement.
Nolan Johnson: Rob, please introduce us to Axiom.
Rob Rowland: Axiom has been an EMS provider for about 30 years. We primarily focus on military, aerospace, space products, and any other high-reliability application type of customers, building the more complex, high-density type of boards. Kevin has been doing placement for over 20 years, both as a machine programmer and a process engineer. We probably handle a wider diversity of unique components than many companies doing board build. Our board sizes range from what you would call a memory module size, up to boards in the 18-by-20-inch size range, so we handle a large variety of different sizes.
Johnson: Is it fair to assume that it’s a mostly high-mix, low-volume setup?
Rowland: Yes. Our expertise is the higher mix, lower volume, with a typical run in the 30- to 50-board range. We have a couple of runs where we’re building in the hundreds, and occasionally into the thousands, but it’s usually jobs fewer than 100 boards. One interesting aspect when talking about placement machines is that most companies in the U.S. are dealing with higher mix, lower volume.
It’s fair to say there’s a big distinction between what you need to do for different production mixes. As I talk with my peers in the industry, one of our biggest challenges for the higher mix, lower volume placement is component packaging.
Packaging—Tape, Reels, and Tubes... Oh My!
Barry Matties: When we talk about packaging, do you mean part of the components?
Rowland: In this case, we’re specifically talking about tape and reel vs. matrix tray vs. tubes. The ideal scenario if you’re running high volumes is to buy full-size reels. When you’re in the high-mix business, you’re typically dealing with much shorter strips of tape, and not all the machines on the market are well-designed to deal with that. It’s a major challenge for domestic companies, and one that the placement industry has not stepped up to address as much as I would like. We had to develop a process that enables us to deal with shorter strips of tape; it’s typically one of our bigger headaches from a board build standpoint.
Johnson: Is that sort of packaging challenge worse when you’re dealing with very small components or is it consistent across the board?
Kevin Bennett: It’s worse when you’re dealing with smaller components, because there are different methods for loading them onto the placement machine. The components are presented in the pockets of the carrier tape with cover tape over the top of each pocket to keep them from falling out. When you have a short strip of tape, there needs to be enough carrier tape length for the feeder to advance correctly. In that case you must prep the strip with an extra length of cover tape, so the mechanism that peels the cover tape back will expose the component for the nozzle to pick from.
If you’re placing short strips of tape on a matrix tray platform, the entire length of cover tape needs to be peeled back before attempting to pick. If the short strip contains small components, a slight bump could cause all the components to come out of the carrier tape with potential loss due to attrition.
To read this entire conversation, which appeared in the May 2022 issue of SMT007 Magazine, click here.
Suggested Items
I-Connect007 Editor’s Choice: Five Must-Reads for the Week
06/27/2025 | Nolan Johnson, I-Connect007While news outside our industry keeps our attention occupied, the big news inside the industry is the rechristening of IPC as the Global Electronics Association. My must-reads begins with Marcy LaRont’s exclusive and informative interview with Dr. John Mitchell, president and CEO of the Global Electronics Association. For designers, have we finally reached the point in time where autorouters will fulfill their potential?
Knocking Down the Bone Pile: Tin Whisker Mitigation in Aerospace Applications, Part 3
06/25/2025 | Nash Bell -- Column: Knocking Down the Bone PileTin whiskers are slender, hair-like metallic growths that can develop on the surface of tin-plated electronic components. Typically measuring a few micrometers in diameter and growing several millimeters in length, they form through an electrochemical process influenced by environmental factors such as temperature variations, mechanical or compressive stress, and the aging of solder alloys.
RTX, the Singapore Economic Development Board Sign MOU Outlining 10-year Growth Roadmap
06/20/2025 | RTXRTX and the Singapore Economic Development Board (EDB) have signed a Memorandum of Understanding (MoU) which outlines a 10-year roadmap to further long-term strategic collaboration in Singapore.
Indra Signs Agreement with AXISCADES to Boost Production of Cutting-Edge Systems in India
06/18/2025 | PRNewswireParis Air Show -- Indra and the Indian technology company AXISCADES have signed an agreement to collaborate on the production of solutions for the aerospace and defense markets.
GKN Aerospace Delivers First High Voltage EWIS System for Clean Aviation’s SWITCH Project
06/16/2025 | GKN AerospaceGKN Aerospace has completed and delivered the first high voltage Electrical Wiring Interconnection System (EWIS) for the Clean Aviation SWITCH project.