PCB Technologies’ InPack to Focus on Miniaturization, Packaging
May 16, 2022 | Andy Shaughnessy, Design007 MagazineEstimated reading time: 11 minutes
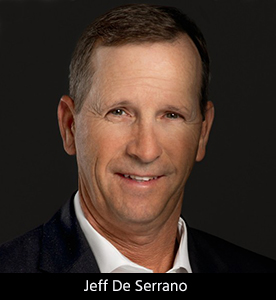
I recently spoke with PCB Technologies’ Jeff De Serrano, Yaniv Maydar, and Alon Menache about their new venture, InPack. They explain their plans to focus on advanced packaging, miniaturization, and other high-end technology, with much faster time to market, and they offer a view of the global market as well.
Andy Shaughnessy: Jeff, nice to talk with you again. Why don’t you start by telling us about InPack?
Jeff De Serrano: This new company is called InPack, a subsidiary of PCB Technologies focusing on SiP (system in packaging), organic substrates, microelectronic assembly, and advanced packaging. We have spent $15.7 million in equipment and software purchases. The equipment we purchased consists of new lamination equipment, advanced registration system and software, high-end microelectronics assembly equipment, and advanced packaging equipment. We will take the 40 years of experience that we have in printed circuit boards from PCB Technologies and incorporate the new company right in the middle of our factory. We have hired a talented engineering team for InPack. Yaniv is running it all for us.
The goal is to help customers from design concept to production utilizing miniaturization and/or double technology. For example, if you have a chipset that’s one inch by one inch, and you need to be able to double the technology inside the same form factor, we can help them. Utilizing our team of engineers, and our abilities to produce organic substrates with 20-micron lines and 25-micron spacing, we can help them achieve their goal. We can also help them with thermal constraints by removing heat from the product if necessary, utilizing thermal coin technology within the substrate. That’s one example of miniaturization—doubling the output in the same form factor size. The second type of miniaturization is taking a one-inch-by-one-inch chip and then reducing it to maybe a half-inch by half-inch with thermal properties that can reduce heat and so forth.
Yaniv Maydar: We invested millions of dollars in equipment, mainly for the processes of assembly, but also for the substrate manufacturing. The technology is basically called a substrate-like PCB or PCB-like substrate. It means that we use the same subtractive processes, but we can go to the PPI resolutions of 20 microns using processes almost identical to the PCB industry or the regular PCB industry, but with a bit more innovative processes that we internally designed. The substrate is defined not only by the resolution, but by the heat dissipation capabilities. We have a process that is enabling us to insert coins, which enables very high heat dissipation. It’s mainly focused for sensors, but not only.
Also, the CTE is not affected by using those inserts. They are very identical to the CTE of the laminates that we use for the substrates. Basically, you get the quality of heat dissipation that you would get from an interposer of silicone by using an organic substrate with inserts.
Shaughnessy: That sounds interesting.
Maydar: It’s actually unique. The thing is that everything could be customized to the customer’s request. It’s one of the ideas that we have. We understand that in the high-mix, low-volume processes, you need to be flexible with the solutions you give, one more thing, we added to the process having the quality of adding copper pillars and any other interconnection capabilities, which are enabling the customer to solve CTE mismatches that he has between substrate and PCB or dyed and substrate. What is called in the industry first and second level reliability issues.
We have identified the main problems that you usually have when using organic substrates. We can solve the main problem, which was interconnection problems. We are adding processes that enable the customer to solve interconnection, thermal and reliability problems. I would say organic substrate solutions in the past were not able to do that. Currently, you must go through ceramic substrates or silicon interposers or sometimes even silicon carbide by interposers. These are very exotic processes, time consuming, and very expensive.
De Serrano: We feel we are the only ones in this market segment doing this process. This was developed and designed by the team that we have in Israel. We don’t know anybody else in the world that’s doing this sort of processing dissipating the heat, and added copper features that extend out through the packaging (copper pillars).
Shaughnessy: And this is all under the banner of InPack?
De Serrano: Yes, InPack is a subsidiary of PCB Technologies, and it is located inside of PCB Technologies factory in Israel. Yaniv has a full design team on staff dedicated to SIP. The goal is to work with customers at the very beginning of their design, this is the best way to help solve problems. However, we can take what they have and do a workaround. We are very proud of our lead time which is time to market. Right now, the competition probably takes anywhere from 18–24 months to get something to the customer. We are very nimble. We can mix them all together if we need to, and the time to market for our customers is around six months. For the customer, at the end of the day, time to market’s going to be expedited from 24 months to six months and they have working product. We all know that first to the market gets most of the revenues.
Maydar: The design process is an all-in-one process, because you can design the PCB board, the substrates, and the packaging solution at the same location. The design rules that you use are under the same roof. You are not moving from subcontractors to subcontractor when solving your problem.
De Serrano: Correct. We can design the printed circuit board, design the packaging, and deliver a finished product. The whole thing under one roof, thus the phrase “all in one.”
Alon Menache: Integration is the key factor here. This is tailor-made. It’s not an off-the-shelf product; it’s a customized product. This is dedicated to specific requirements based on the customer needs, engineer needs, or specification. This is what we are coming for in terms of the IP or any technical performance, which might be delivered out of this product.
Shaughnessy: With InPack, do you engage with the customer? Let’s say they have the board, they have the basic fab set up, but they just need to use you for the heat dissipation. Is it configurable like that?
Maydar: Yeah, it is. You can slice it up anyway you want to use the process. We are very flexible.
Shaughnessy: Very cool.
De Serrano: They’ve already designed their package, but they need the substrate board to come into play. We can jump in at this point and really help them design the substrate for any problems they might have, like thermal dissipation concerns. That’s where Yaniv’s team comes in. The customer says, “We designed this chip, it is powerful but we don’t know how to get the heat out anymore.” Yaniv’s design team will help them design a substrate board with a coin in it or whatever it needs to draw the heat out the backside.
This is another reason why it is important to have the microelectronics assembly in the same facility: the teams collaborate for best results. We purchased the best of the best assembly equipment and advanced packaging equipment, so everything is in one location.
Maydar: Exactly. Also, the assembly processes that we have designed are unique. It enables you to customize the process, which enables you to have a package-on-package solution tailor made or customized for your applications. It’s not a certain design process that you must buy in a certain fabrication or packaging company. You can design the assembly process to your needs. For example, if you want to have an antenna on package, you can do that. If you want to have a filter on package, you can do that.
Menache: The flexibility is also a key factor here because we have wide range of equipment and tools to cover the advanced packaging processes available right now.
De Serrano: But you know, Andy, the key for customers is the time to market and flexibility. When you go across the water to the big guys, and let’s say it’s a defense and aerospace company, they don’t buy millions of these. They buy hundreds of thousands. So, when they get in line over there, they must pick a specific production line, for example, A, B, C, and D with defined processes. With us, you don’t have to do that. The difference about us is the flexibility of being nimble for our customers.
We’re really going to kick it off at the IMS show in June. We will having meetings with a lot of key players in the defense and aerospace, the sensor market, and commercialized markets segments as well. We have a DFM team on staff at the show to do meetings, answer questions, and go over some design rules. We will have four people from Israel and four from the U.S. at the show.
Shaughnessy: Now, at IPC APEX EXPO you mentioned that the new company would be a much faster operation than the existing operation in Israel, correct?
De Serrano: Yes. For the InPack division, we spent a lot of money and have a separate team for this business unit. The PCB shop is doing well and growing; we specialize in RF, especially rigid-flex, defense, and aerospace markets. The big goal is launching InPack at IMS. We want to kick this thing off and make sure people understand what we’re able to do, and the investment we put into this market segment. We are serious and see a lot of potential. We will have the team there to be able to talk the talk.
Shaughnessy: How is it set up? Is InPack a separate entity?
De Serrano: It’s under the umbrella of PCB Technologies, but we can’t go standalone by ourselves yet. Eventually we believe this business model will exceed the printed circuit board model. When that happens, then we might break them apart.
Yaniv came from this industry and now we’re blessed to have him on our team. He was on the other side, so he understands the customer needs because he was one. The design team is the other part of it. The team knowing when a customer says, “My chip is blowing up all the time because we can’t get the heat out”; they know exactly what to do.
Shaughnessy: Well, it sounds like the automotive guys would be interested in this too. We talk to them and they’re having problems.
De Serrano: Yes, you are correct, however the automotive market is just about high volume and cost. We are going to stay focused right now in the RF and sensor markets for now unless they approach us themselves.
The medical market is another area we will be focused on as well. They are talking about making MRI units and so forth that can be put in a truck and taken to your house because of COVID. How are they going to do this? They must miniaturize everything.
Shaughnessy: And it’s high mix, low volume. That’s your wheelhouse for this.
De Serrano: Right. We’re not going to do a million per month, but hundreds of thousands, yes. Yaniv’s got it, and the team’s got it.
Shaughnessy: Well, it sounds like you are in a good spot as far as the market goes.
De Serrano: If we can do the right job marketing the product and getting in front of the correct people it will sell itself. We must make sure the team does a great job getting it in front of the right people.
Shaughnessy: How many people are we talking about on the InPack team?
Maydar: We’re talking about the design team that contains 10 people dealing with design processes, thermal design, and electrical design.
De Serrano: We built the team before we did anything else, because if we go out and market, then suddenly we’ve got to hire people to do it, we’re going to be in trouble. We’ve got to be able to produce when you come to us. We are just kicking it off, and we do have talks going on right now for some serious programs. Yaniv’s team can handle several programs at one time with the staffing we have already. We expect to handle 12 new design-to-spec and 24 build-to-print jobs per year with the team we have now.
Shaughnessy: Well, it sounds like a fun venture.
De Serrano: Yes. Something new to present to the market, an “all in one” solution. We are very focused on strategic marketing so we can get some early wins on the books. We already have a couple of new customers in the works right now. Everywhere we present this “all in one” solution the customers are very interested.
Shaughnessy: Tell us a little about the organic substrates that you guys are working with.
Maydar: The stability in the design is much greater when you use organic substrates because you can play with laminates, CTE, or thermal dissipation properties. You have endless flexibility, for example, using a silicon interposer. With an interposer you are stuck with a 2.5 CTE and you need to match it to a certain substrate after that.
We’re working with a few defense companies in Israel on sensors—mainly transmit-receive sensors in various of sizes with a very high thermal dissipation requirement. Right now, we are mainly working with the largest Israeli defense companies, like IAI and Elbit.
Shaughnessy: Thank you all for speaking with me.
De Serrano: Thank you Andy. We look forward to our next interview.
Suggested Items
RF PCB Design Tips and Tricks
05/08/2025 | Cherie Litson, EPTAC MIT CID/CID+There are many great books, videos, and information online about designing PCBs for RF circuits. A few of my favorite RF sources are Hans Rosenberg, Stephen Chavez, and Rick Hartley, but there are many more. These PCB design engineers have a very good perspective on what it takes to take an RF design from schematic concept to PCB layout.
Trouble in Your Tank: Causes of Plating Voids, Pre-electroless Copper
05/09/2025 | Michael Carano -- Column: Trouble in Your TankIn the business of printed circuit fabrication, yield-reducing and costly defects can easily catch even the most seasoned engineers and production personnel off guard. In this month’s column, I’ll investigate copper plating voids with their genesis in the pre-plating process steps.
Elephantech: For a Greener Tomorrow
04/16/2025 | Marcy LaRont, PCB007 MagazineNobuhiko Okamoto is the global sales and marketing manager for Elephantech Inc., a Japanese startup with a vision to make electronics more sustainable. The company is developing a metal inkjet technology that can print directly on the substrate and then give it a copper thickness by plating. In this interview, he discusses this novel technology's environmental advantages, as well as its potential benefits for the PCB manufacturing and semiconductor packaging segments.
Trouble in Your Tank: Organic Addition Agents in Electrolytic Copper Plating
04/15/2025 | Michael Carano -- Column: Trouble in Your TankThere are numerous factors at play in the science of electroplating or, as most often called, electrolytic plating. One critical element is the use of organic addition agents and their role in copper plating. The function and use of these chemical compounds will be explored in more detail.
IDTechEx Highlights Recyclable Materials for PCBs
04/10/2025 | IDTechExConventional printed circuit board (PCB) manufacturing is wasteful, harmful to the environment and energy intensive. This can be mitigated by the implementation of new recyclable materials and technologies, which have the potential to revolutionize electronics manufacturing.