-
- News
- Books
Featured Books
- pcb007 Magazine
Latest Issues
Current IssueSales: From Pitch to PO
From the first cold call to finally receiving that first purchase order, the July PCB007 Magazine breaks down some critical parts of the sales stack. To up your sales game, read on!
The Hole Truth: Via Integrity in an HDI World
From the drilled hole to registration across multiple sequential lamination cycles, to the quality of your copper plating, via reliability in an HDI world is becoming an ever-greater challenge. This month we look at “The Hole Truth,” from creating the “perfect” via to how you can assure via quality and reliability, the first time, every time.
In Pursuit of Perfection: Defect Reduction
For bare PCB board fabrication, defect reduction is a critical aspect of a company's bottom line profitability. In this issue, we examine how imaging, etching, and plating processes can provide information and insight into reducing defects and increasing yields.
- Articles
- Columns
- Links
- Media kit
||| MENU - pcb007 Magazine
Estimated reading time: 4 minutes
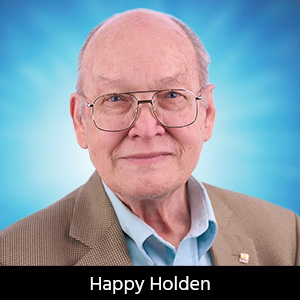
Contact Columnist Form
Happy's Tech Talk #8: Copper Etchant Regeneration
Copper has become a valuable metal, and with the growth of EV has come higher currents needed in PCB resulting in increased weight of copper in PCBs. This creates the need for increased copper etching and consumption of copper etchants.
Alkaline ammonium chloride and acidic cupric chloride remain the most used etchants with various peroxide-sulfurics as micro-etches. Still in use, but in much smaller applications, are ferric chloride, alkaline ammonium sulfate, alkaline cupric chloride, and sodium persulfate.1,2
Any ammonium compounds in rinse water complicate water treatment as they will chelate any metals in the final effluent and make it more expensive to treat.
Etchant Regeneration Techniques
Karl Dietz wrote on this topic several times in his Tech Talk Series. No less than eight columns were devoted to etching chemistry, but only one went into details about chemical regeneration (TT#92). The etching Tech Talk columns were:
- TT#92: Etchant Recycling (CircuiTree, May 2003)
- TT#112: Ammoniacal Etching (Part A) (CircuiTree, January 2005)
- TT#113: Ammoniacal Etching (Part B) (CircuiTree, January 2005)
- TT#119: Fine Lines in High Yield (CircuiTree, August 2005)
- TT#151: Ferric Chloride Etching of Copper (the PCB Magazine, April 2008)
- TT#158: Fine Line Etching Revisited, Part A (the PCB Magazine November 2008)
- TT#159: Fine Line Etching Revisited, Part B (the PCB Magazine, December 2008)
- TT#160: Fine Line Etching Revisited, Part C (the PCB Magazine, January 2009)
Liquid-Liquid Extraction
Liquid-liquid extraction (LLE) or Liquid ion-exchange has been used for metal recovery from mining for many years. But in the early 1970s, a new organic extractant was developed out of wheat by General Mills. This new metal chelating agent is 7-ethyl-undeca-2,4-dione, trademarked by General Mills as LIX64N and LIX65N. This organic is dissolved and mixed with kerosene (~20% dissolution) and has an extremely high affinity for copper and zinc.3
The unique feature of these compounds with respect to metal chelating is that, in the extraction step, the base metal is capable of being loaded to the exclusion of ammonia or chlorides, thereby resulting in essentially a zero carryover of ammonia/chlorides to the stripping step. Moreover, in the stripping step the extractant does not form a salt with the acid present and hence can be recycled directly to the extraction stage without the necessity of further treatment.
The extraction and regeneration process are shown in Figure 1.4
Figure 2 is a diagram of a mixer-separator unit that shows the mixing and separating chamber where the organic phase is less dense and floats on the aqueous phase to extract the copper into the organic phase. Other unit operations equipment used for LLE are sieve tray and bubble-cap towers, but the mixer-separator is the simplest and easiest to maintain.
Figure 3 shows diagrams of an LLE system for printed circuit etching of either alkaline or acid types of etchants with copper recovery. Many of these have been installed over the years. Figure 3a is the mixer-separator unit that strips the copper out of the etchant. In Figure 3b, another mixer-separator unit can strip the copper into the acid electrolyte, whereas in Figure 3c, the copper is plated out as sheets from the copper sulphate electrolyte. Figure 3d is the final mixer-separator that removes copper from the etcher’s rinse water and returns it to the cascade etcher rinses while the organic phase is combined with the etchant extract. All streams are 100% recycled.
Figure 4 shows a typical industrial mixer-separator drawing used for etchant regeneration. Six separate mixer-separators are contained in this one unit. Many times, more than one unit is used for the extraction stage and for the stripping stage, as seen in Figure 1. Figure 5 shows an actual copper recovery unit installed in a printed circuit fabrication facility.5
Conclusion
When the LLE extraction and recovery unit was first designed in 1974 by Hewlett-Packard’s PCB Group for its alkaline etching system in Palo Alto, California, no others were in use. Today, more than 100 units have been installed around the world recovering copper and regenerating their PCB etchants. One of the most recent, installed at Whelen’s GreenSource Fabrication in New Hampshire, recovers over $375,000 in copper every year.
This puts the chemical and water recovery system into a profit generator for the facility. Their daily water use for the 100-panel per hour facility is less than what is used by their toilets.
References
- “Improved Inner Layer Etching by Simultaneous Cupric Regeneration and Copper Recovery System,” by Paul Watson, ILS Conference, Leeds, UK, 1999.
- CEMCO Etchant Regeneration Brochure for Cupric Chloride, 2 Relay Rd. Waterlooville, Hampshire UK, 1999.
- Liquid Ion Exchange in Metal Recovery and Recycling, by Lawrence V. Gallacher.
- “New Horizons in Metal Removal And Recovery,” by W. Daniel Ernt, P.E., American Institute of Chemical Engineers Annual Technical Meeting, April 17, 1990.
- The MecerTM System Brochure for PCB etchant recycling and copper recovery, Sigmametallextrakton AB, Datavagen 51, Sweden.
This column originally appeared in the May 2022 issue of PCB007 Magazine.
Happy Holden has worked in printed circuit technology since 1970 with Hewlett-Packard,?NanYa?Westwood, Merix, Foxconn, and Gentex. He is currently a contributing technical editor with I-Connect007, and the author?of?Automation and Advanced Procedures in PCB Fabrication, and?24 Essential Skills for Engineers.
More Columns from Happy’s Tech Talk
Happy’s Tech Talk #40: Factors in PTH Reliability—Hole VoidsHappy’s Tech Talk #39: PCBs Replace Motor Windings
Happy’s Tech Talk #38: Novel Metallization for UHDI
Happy’s Tech Talk #37: New Ultra HDI Materials
Happy’s Tech Talk #36: The LEGO Principle of Optical Assembly
Happy’s Tech Talk #35: Yields March to Design Rules
Happy’s Tech Talk #34: Producibility and Other Pseudo-metrics
Happy’s Tech Talk #33: Wet Process Management and Control