EIPC Summer Conference 2022: Day 2 Review
June 29, 2022 | Pete Starkey, I-Connect007Estimated reading time: 11 minutes
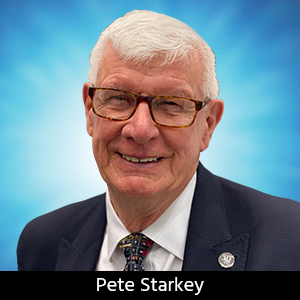
Örebro, Sweden on June 15 brought a bright and early start to Day 2 of the EIPC Summer Conference for those who had enjoyed the previous evening’s networking dinner, but had resisted the temptation to over-indulge or to carry on their long-awaited catch-up conversations with old friends into the small hours. All but a few were in their seats for 9 a.m., awake and attentive for Session 4 of the conference, on the theme of new process technologies, moderated by Martyn Gaudion, CEO of Polar Instruments.
As digital technologies continue to change the shape of electronics manufacturing, Dr. Kai Keller, director of business development with Notion Systems in Germany, put a perspective on the realities of additive digital processes with his reference to the Gartner Hype Cycle, the graphical depiction of a common pattern that arises with each new technological innovation. Beginning with a technology trigger, the curve rises rapidly through a peak of inflated expectation before promptly declining into a trough of disillusionment from which it progresses steadily up a slope of enlightenment and matures toward a plateau of productivity.
Commenting that manufacturing electronics is a wasteful undertaking, particularly regarding the consumption of enormous volumes of water, Dr. Keller set out to explore the potential for additive functional manufacturing of full electronic devices, taking as an example the inkjet printing of OLEDs from its origins in 2004 to the mass production of high resolution OLED monitors in 2021. “It might take long, but additive production processes will prevail in the end, simply because they make sense,” he said.
The focus of his presentation was the inkjet printing of solder mask on PCBs, and again he reviewed the history of its development from 2003 to the present day, when the technology is well proven and market adoption of inkjet solder mask is ongoing.
Keller outlined the principles of the process, discussed data preparation and full workflow integration, and reviewed the results. As well as high repeatability, the benefits of digital inkjet solder mask included no mask in holes, no mask on pads, adjustable thickness, and small and reliable solder dams. He went into detail on their natural bump profile: their wider base gave improved adhesion, with no undercut areas to trap chemicals or dirt. And he showed many real examples illustrating precise dimensional control.
The development team at Notion Systems continues to work on increasing the digital additive process window, and has realised more than 40 different additive production processes for conductives, dielectrics, resists, adhesives, active layers, optics, and coatings.
Novel nickel-free surface finishes for next-generation PCB technologies was the topic of the presentation from Dr. Kunal Shah, president and chief scientist at LiloTree in the United States.
Dr Shah remarked that high frequency PCBs was one of the fasted growing areas in the electronics industry and that a novel approach in surface finish was essential to obtain optimum performance and better reliability of electronic assemblies.
Although electroless nickel/immersion gold (ENIG) was currently the most widely used finish for high-end PCBs, it was not optimal for 5G frequencies because of high insertion loss due to the nickel layer. ENIG could also suffer from hyper-corrosion issues and brittle solder joint failures.
Current alternatives for 5G PCBs included direct immersion gold, electroless palladium immersion gold, and electroless palladium autocatalytic gold, although there were still concerns in terms of higher insertion loss and brittle solder joints. Higher thicknesses of precious metals were not cost-effective and not eco-friendly.
Shah described a novel nickel-free surface finish, with 50 nanometres of cyanide-free gold on copper treated with a nano-engineered barrier layer. The finish was characterised by robust solder joints with thin and distinct intermetallics. It was cost effective because of its significantly lower precious metal thickness than current alternatives. The new finish used a simple plating set-up of four process tanks and four rinse tanks.
The insertion loss of the nickel-free finish was almost identical to that of bare copper over the 0–100GHz frequency range, there was negligible change in contact resistance through six reflow cycles and the nano-engineered barrier layer prevented diffusion of copper into gold, leaving the surface corrosion-free. The process was cyanide-free, halogen-free, and RoHS and REACH compliant. As well as low insertion loss, it enabled robust solder joints with no brittle intermetallic failures.Page 1 of 3
Testimonial
"We’re proud to call I-Connect007 a trusted partner. Their innovative approach and industry insight made our podcast collaboration a success by connecting us with the right audience and delivering real results."
Julia McCaffrey - NCAB GroupSuggested Items
Indium Corporation Promotes Two Leaders in EMEA (Europe, Middle East, and Africa) Markets
08/05/2025 | Indium CorporationWith its commitment to innovation and growth through employee development, Indium Corporation today announced the promotions of Andy Seager to Associate Director, Continental Sales (EMEA), and Karthik Vijay to Senior Technical Manager (EMEA). These advancements reflect their contributions to the company’s continued innovative efforts with customers across Europe, the Middle East, and Africa (EMEA).
MacDermid Alpha Electronics Solutions Unveils Unified Global Website to Deepen Customer, Talent, and Stakeholder Engagement
07/31/2025 | MacDermid Alpha Electronics SolutionsMacDermid Alpha Electronics Solutions, the electronics business of Elements Solutions Inc, today launched macdermidalpha.com - a unified global website built to deepen digital engagement. The launch marks a significant milestone in the business’ ongoing commitment to delivering more meaningful, interactive, and impactful experiences for its customers, talent, and stakeholders worldwide.
KOKI to Showcase Analytical Services and New HF1200 Solder Paste at SMTA Guadalajara 2025
07/31/2025 | KOKIKOKI, a global leader in advanced soldering materials and process optimization services, will exhibit at the SMTA Guadalajara Expo & Tech Forum, taking place September 17 & 18, 2025 at Expo Guadalajara, Salón Jalisco Halls D & E in Guadalajara, Mexico.
Weller Tools Supports Future Talent with Exclusive Donation to SMTA Michigan Student Soldering Competition
07/23/2025 | Weller ToolsWeller Tools, the industry leader in hand soldering solutions, is proud to announce its support of the upcoming SMTA Michigan Expo & Tech Forum by donating a limited-edition 80th Anniversary Black Soldering Set to the event’s student soldering competition.
Koh Young Appoints Tom Hattori as President of Koh Young Japan
07/21/2025 | Koh YoungKoh Young Technology, the global leader in True 3D measurement-based inspection solutions, announced the appointment of Tom Hattori as President of Koh Young Japan (JKY).