Excerpt Chapter 5: 'The Printed Circuit Designer’s Guide to... Thermal Management with Insulated Metal Substrates, Vol. 2'
August 9, 2022 | Didier Mauve and Robert Art, VentecEstimated reading time: 2 minutes
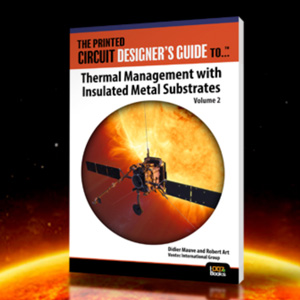
Chapter 5: Boosting Thermal Performance with Multilayer IMS
In The Printed Circuit Designer’s Guide to... Thermal Management with Insulated Metal Substrates (Vol. 1), the authors briefly discussed the issues around combining multiple layers of copper foil, dielectric, and substrate materials and the design opportunities given by the latest generation of thermally conductive thin cores and prepregs.
The latest thermally conductive materials, prepregs, and cores allow designers to reconsider the thermal management approach. They can offer a simple and ready-to-use solution to address thermal issues on existing multilayer boards.
Through necessity, the industry has already come up with many solutions over the years, such as thermal vias, thermal coins, and inserts. All these existing solutions require either the use of thick copper foil and/or the use of heavy copper coins, thus leading to an inevitable inflation in cost and weight. We can now analyze alternative designs made possible by the arrival of multilayered IMS. The following application examples illustrate the concept and the main benefits of multilayered IMS.
Figure 5.1: Single-sided single layer.
The PCB design with insulated metal substrates is by no means limited to single-sided and single-layered circuits (Figure 5.1), although these are predominantly the types of circuits used in LED-lighting and power electronics applications.
There are several versatile ways to take advantage of IMS’s enhanced thermal properties in situations that demand various other attributes such as physical formability or compliance, an intricate shape or small dimensions, or a complex circuit layout that would be fulfilled with a multilayered PCB if it weren’t for the thermal issues.
If a formable grade of laminate (such as, for example, aluminum 5052 with a thin, non-reinforced dielectric) is specified, a single-sided circuit can be post-formed into three-dimensional shapes. This may help to design a circuit board that must fit inside a small or unusually shaped enclosure, or to cram more electronic circuitry within a limited space, or maybe ease assembly of a product if there is only minimal access to install electronic circuit boards. The aluminum layer is machined to reduce its thickness in the bend area.
Figure 5.2: Single-sided double layer.
Also, it is possible to build insulated metal substrates into multilayered IMS structures (Figure 5.2) with thermally conductive laminates and prepregs using plated-through holes for Z-axis interconnection.
In situations where the metal base is not an option, but the component temperature needs to be reduced, an alternative construction may be necessary; the thermal conductive cores and prepreg may be combined to create the entire board or may be used in a hybrid construction combining conventional FR-4 and thermal conductive cores or prepreg.
To continue reading this chapter, download your copy of this book from the I-007eBooks library today!
Suggested Items
Trump Copper Tariffs Spark Concern
07/10/2025 | I-Connect007 Editorial TeamPresident Donald Trump stated on July 8 that he plans to impose a 50% tariff on copper imports, sparking concern in a global industry whose output is critical to electric vehicles, military hardware, semiconductors, and a wide range of consumer goods. According to Yahoo Finance, copper futures climbed over 2% following tariff confirmation.
Happy’s Tech Talk #40: Factors in PTH Reliability—Hole Voids
07/09/2025 | Happy Holden -- Column: Happy’s Tech TalkWhen we consider via reliability, the major contributing factors are typically processing deviations. These can be subtle and not always visible. One particularly insightful column was by Mike Carano, “Causes of Plating Voids, Pre-electroless Copper,” where he outlined some of the possible causes of hole defects for both plated through-hole (PTH) and blind vias.
Trouble in Your Tank: Can You Drill the Perfect Hole?
07/07/2025 | Michael Carano -- Column: Trouble in Your TankIn the movie “Friday Night Lights,” the head football coach (played by Billy Bob Thornton) addresses his high school football team on a hot day in August in West Texas. He asks his players one question: “Can you be perfect?” That is an interesting question, in football and the printed circuit board fabrication world, where being perfect is somewhat elusive. When it comes to mechanical drilling and via formation, can you drill the perfect hole time after time?
The Evolution of Picosecond Laser Drilling
06/19/2025 | Marcy LaRont, PCB007 MagazineIs it hard to imagine a single laser pulse reduced not only from nanoseconds to picoseconds in its pulse duration, but even to femtoseconds? Well, buckle up because it seems we are there. In this interview, Dr. Stefan Rung, technical director of laser machines at Schmoll Maschinen GmbH, traces the technology trajectory of the laser drill from the CO2 laser to cutting-edge picosecond and hybrid laser drilling systems, highlighting the benefits and limitations of each method, and demonstrating how laser innovations are shaping the future of PCB fabrication.
Day 2: More Cutting-edge Insights at the EIPC Summer Conference
06/18/2025 | Pete Starkey, I-Connect007The European Institute for the PCB Community (EIPC) summer conference took place this year in Edinburgh, Scotland, June 3-4. This is the third of three articles on the conference. The other two cover Day 1’s sessions and the opening keynote speech. Below is a recap of the second day’s sessions.