Estimated reading time: 5 minutes
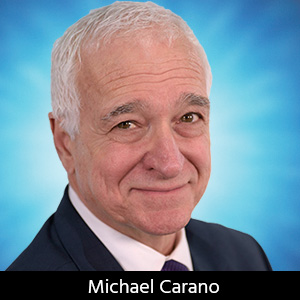
Contact Columnist Form
Trouble in Your Tank: Can You Drill the Perfect Hole?
In the movie “Friday Night Lights,” the head football coach (played by Billy Bob Thornton) addresses his high school football team on a hot day in August in West Texas. He asks his players one question: “Can you be perfect?” That is an interesting question, in football and the printed circuit board fabrication world, where being perfect is somewhat elusive. When it comes to mechanical drilling and via formation, can you drill the perfect hole time after time?
Over these many years, I’ve learned that you cannot fix poorly drilled vias with good plating, and you cannot make perfectly drilled vias more reliable with poor plating.
Via formation is followed by desmear and metallization. The quality of the through-hole drilling process (and by inference the quality of the drilled through-hole) or lack thereof will also impact the desmear and metallization processes. While drilling equipment, tools, and methods have been continually improved over the years, the fabricator must adhere to strict guidelines with respect to maintenance of the equipment, quality of the drill bits, the drilling operation parameters, and the proper selection and use of entry and back-up materials. When simple maintenance of drill equipment and drill bits is lacking, drilled hole-wall quality deteriorates. This leads to defects in the plated through-hole (PTH) that are not attributable to the plating processes, such as electroless copper.
Drilling Basics
Through-holes are formed by the cutting action of drill bits in numerically controlled drilling machines. Figure 1 shows a five-head drilling machine.
There are multiple factors to consider when mechanically drilling plated through-holes and blind and buried vias (assuming mechanical drilling will be used on a few applications for blind/buried vias). These include the drill machine, drill bits, entry and back-up materials, drilling parameters, stack heights, etc. In addition, the type of resin that makes up the circuit board, along with glass weave style and content, will play a role in drilling via quality. This will be the subject of a future column.
First, Figure 2 depicts what can happen when the drilling operation is not in control.
Note the gouges in the resin and the torn-out glass bundles. When a drilled hole such as this makes its way to the PTH process, the ability of the electroless copper or direct metallization chemistries to properly deposit in these drill gouges is compromised. Even if the PTH metallization is successful, subsequent electrodeposition of copper will yield areas where the copper thickness is too thin (thus violating copper thickness requirements), and potentially have a situation where the plated copper folds over. In the latter case, the copper cannot level due to the drill gouge. This leaves a very thin area and leads to the potential for a blow hole during assembly or an open in the PTH. This is precisely why many finished bare boards successfully pass in-circuit test only to exhibit some interrelated non-conforming defect after assembly (Figure 3).
Certainly, it is possible that there may be issues with the wave solder flux, but we can assume that’s not the case here. Note the areas of thin copper plating, small voids, and rough hole walls. All these issues will contribute to the potential for the occurrence of blow holes. While it is possible that thin copper-plated deposits and voids can be attributed to the plating processes, these issues can also be directly related to poor hole drilling conditions. That is why the adage “Garbage in, garbage out” applies here. One cannot expect plating chemistries to defy physics and Faraday’s Law and always make up for poor hole wall conditions (Figure 2).
Drilling and Basic Definitions
Drilling conditions depend on the drilling machine, brand of drill bit, drill bit design, type of spindle, stack height, PCB material, amount of copper to be drilled, drill aspect ratio, entry and backup materials, etc. Hole wall quality, drilling accuracy, and the potential for drill bit breakage are results of the combined effect of all drilling parameters.
Let’s review a few very key drilling parameters and their definitions:
- Feed rate: The speed of a drill bit toward and through the circuit board stack to be drilled. The feed rate is measured in meters per minute (m/minutes) or inches per minute (IPM). It’s one of the key parameters of chip load.
- Spindle speed: The rotational rate (RPM) of the drill spindle. It is the other key parameter of chip load.
- Chip load: The depth or distance through a stack that a drill bit travels for each revolution it turns. Chip load is typically measured in mils or inches per revolution (IPR), or micrometer per revolution (μm/rev).
To calculate chip load, use the following equation:
So, chip load in inches per minute is determined by feed rate of the drill spindle divided by the rotational rate of the spindle. One may also calculate chip load in mils of feed divided by the RPM of the spindle.
Variation in the feed rate and chip loads affects hole wall quality. On the positive side, low feed rates will improve hole positional accuracy. On the negative side, low feed rates will cause excessive heat, resulting in resin smear and nail heading (of the inner layer copper). Low feed rates may also cause glass fiber damage, resulting in wicking at plating or fiber removal. On the positive side, high feed rates will reduce resin smear. On the negative side, high feed rates create burrs, hole wall roughness, and debris in the holes.
According to standard drilling guidelines, smaller-diameter holes and thicker boards require lower chip loads. In a future column, I will present more in-depth information on drilling and its ramifications for PTH quality and reliability.
Materials to be Drilled
One must also consider the materials used to construct the circuit board. The drill bits eventually wear out, leading to poorly drilled vias. Some higher-performance materials, such as ceramic-filled, lead to faster drill bit wear out. Wear and tear on the bits leads to increased drill smear and rougher hole walls, not to mention additional heat generation. One must understand that in this scenario, the drill hit count must be reduced.
Summary
It has been suggested that producing high-quality, high-reliability printed circuit boards requires strict adherence to processing guidelines and vigilance in understanding and executing the principles of troubleshooting. A thorough understanding of each process step is critical in minimizing or eliminating non-conforming defects—the ones that cost the fabricator money and can lead to lost customers. Each process must be deeply understood on its own merits. Mechanical drilling is one such process. Yes, it is possible to be perfect.
This column originally appeared in the June 2025 issue of PCB007 Magazine.
More Columns from Trouble in Your Tank
Trouble in Your Tank: Yield Improvement and ReliabilityTrouble in Your Tank: Causes of Plating Voids, Pre-electroless Copper
Trouble in Your Tank: Organic Addition Agents in Electrolytic Copper Plating
Trouble in Your Tank: Interconnect Defect—The Three Degrees of Separation
Trouble in Your Tank: Things You Can Do for Better Wet Process Control
Trouble in Your Tank: Processes to Support IC Substrates and Advanced Packaging, Part 5
Trouble in Your Tank: Materials for PWB Fabrication—Drillability and Metallization
Trouble in Your Tank: Supporting IC Substrates and Advanced Packaging, Part 5