-
- News
- Books
Featured Books
- pcb007 Magazine
Latest Issues
Current IssueSales: From Pitch to PO
From the first cold call to finally receiving that first purchase order, the July PCB007 Magazine breaks down some critical parts of the sales stack. To up your sales game, read on!
The Hole Truth: Via Integrity in an HDI World
From the drilled hole to registration across multiple sequential lamination cycles, to the quality of your copper plating, via reliability in an HDI world is becoming an ever-greater challenge. This month we look at “The Hole Truth,” from creating the “perfect” via to how you can assure via quality and reliability, the first time, every time.
In Pursuit of Perfection: Defect Reduction
For bare PCB board fabrication, defect reduction is a critical aspect of a company's bottom line profitability. In this issue, we examine how imaging, etching, and plating processes can provide information and insight into reducing defects and increasing yields.
- Articles
- Columns
- Links
- Media kit
||| MENU - pcb007 Magazine
Estimated reading time: 5 minutes
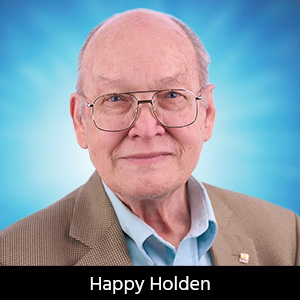
Contact Columnist Form
Happy's Tech Talk #11: An Update on Inkjet Technologies
Ever since the first inkjet printer appeared from Hewlett-Packard in 1980, engineers have been trying to use it in printed circuit manufacturing. The first successful application was by HP’s PCB engineers in 1983, who created an inkjet printer mechanism to serialize each PCB with a unique S/N for traceability. They used one of the UV inks HP had developed and that worked well on circuit boards but was not suited for use on paper.
Introduction
Karl Dietz wrote on this topic when it first began to appear as a method of solder mask application and legend printing to replace screen printing. Some of his columns1 discussed the methods of inkjet printing, elements of the three types of inks (thermal, ultra-violet, and phase-change), and the print-heads used by seven current machines on the market. Today, the applications, head technologies, software and inks/pastes have been improved significantly. Inkjet is one of the technologies used in printed electronics.
Inkjet Printing
An industrial inkjet printer has four important elements, as seen in Figure 1:
- The printhead(s)
- The ink or paste
- The print module-ink preparation or curing
- System for CAM data preparation and head/substrate positioning
Figure 1: Inkjet system breakdown into four elements. (Source: Dow Electronics Materials)
Inkjet printing technology produces droplets of the ink contained in the fluid channel, with diameters ranging from 10 to 150 ?m, which approximately correspond to the diameter of the nozzle (Figure 2). The volume of the droplets is in the picoliter range. Inkjet printing is suitable for electronics manufacturing due to the following reasons:
- It is a non-contact process that selectively deposits a wide range of materials onto a wide range of substrates in a drop-by-drop manner
- The shop floor space requirements, the initial investment, and the time to get an inkjet printing setup running are lower than most other printing technologies
- It is suitable for a wide range of production scales, from prototyping to large-scale industrial production
- Ink consumption and material waste are minimal
- It is flexible regarding its positioning within a process chain
- It can produce patterned thin films. It should be mentioned however, that manufacturing of highly complex integrated circuits (ICs) has exclusively been performed by specialized techniques deviating from standard inkjet technologies.2
Figure 2: Simplification of inkjet printing process3.
Inkjet Printheads
The printhead is the heart of the inkjet printer. In addition to the original thermal thin-film printhead of HP’s, there is also the piezo-electric head that makes up most of the additive-type of inkjet printing. Now comes the piezo-acoustic head and the continuous laser-assisted system (LIFT), as seen in Figure 3.
Figure 3: Laser induced forward transfer (LIFT) system4 and new piezo-acoustic head5.
These new technologies extend the number of inks that can use inkjet printing. The capability of a head is a function of the droplet size, its overlap, and the frequency the head can achieve, now 80 kHz. This permits resolution of 5,000 dpi and resulting minimum copper line widths of 40 to 70 microns.
To improve both speed and density, inkjetting has taken a page from the DMD micro-mirrors exposure book and now uses multiple inkjet heads to achieve this performance. Figure 4 shows a test vehicle from the Center for Microsystems Technology (CMST) of Ghent University and IMEC with etched traces down to 40 microns.
Figure 5 illustrates this etching/plating resist capability on a Samsung panel with the Samsung printhead using five pl-256 nozzles.
Figure 5: Another example of a production inner layer, before and after etching of 75/75-micron traces and spaces3.
Ink or Pastes
There were numerous challenges with ink formulation, including adhesion, curing, and especially spreading after jetting. Figure 4 illustrates the difference between general inkjet printing on paper vs. inkjet printing on a PCB.
Ink Preparation/Curing
In addition to jetting the ink, the system may have to prepare the ink (by melting a hot-melt ink) or by curing a UV ink.
System Software and Positioning
The additional system activities may include positioning of the inkjet heads and, particularly, the preparation of the CAM information to drive the inkjet heads and substrate positioning. Table 1 illustrates the printing time for a 75/75-micron traces on a 460 mm x 610 mm panel using only one head vs. 15 heads.
The sensitivity of print time vs. number of heads is seen in Figure 6.
For advanced systems, large panel throughput can be:
- 17.0" x 22.8": 17 seconds
- 20.0" x 24.0": 27 seconds
- 24.0" x 30.7": 31 seconds
Applications
The advantages of inkjet printing as a method of solder masking and legend printing are well established. As an etch resist for inner layer etching it has an advantage down to
The market for inkjet printheads will grow to $3.3 billion by 2024 (Figure 7).
Conclusion
From its simple beginnings as a quiet way to print on plain paper, inkjetting has grown up. This is because the head technology is being modified to use a much greater variety of materials to jet. Here are 12 applications of inkjet technology, and the list is growing:
- Antenna: For example, wireless, mobile phones, IIoT, mil/space, CB
- Membrane switch: Keypads
- Capacitors, resistors, and inductors
- Shielding: For example, RFI and EMI
- Sensors and precision interconnects
- Photovoltaic (solar cells)
- RFID inlays/tags and Smart cards, e-passport/ID cards
- Electroluminescence, touch panels and other displays
- Automotive and telecom
- Medical and diagnostic devices
- Heater circuits
- Replacement of gold plating on switches
Figure 7: Prediction of the growth of inkjet printhead sales for consumer, industrial, and graphics printing. (Source: YOLE Development3)
As it competes with dry film photoresists, inkjet technology still has some significant challenges for the machine manufacturers to overcome, including making sharp corners (drops will always produce a curve), getting track edges as smooth and straight as possible, replicating standard industry practices such as tenting, and ensuring printhead maintenance programs to avoid nozzle blockages, But it’s on its way.
References
- Columns by Karl Dietz in The PCB Magazine: Tech Talk #73, October 2001; Tech Talk #137, February 2007.
- “Digital and Environmental Circuit Board Manufacturing Based on Continuous Laser Assisted Deposition,” Ralph Birnbaum, et al, IPC APEX 2022.
- “The Use of Inkjet Printing Technology for Fabricating Electronic Circuits—The Promise and the Practical,” by Thomas Sutter and Brian Amos, IPC APEX EXPO 2012.
- “Customizable Capacitive Sensor System Using Printed Electronics on Window Glass,” by Jan Frohlich, et al, SMTA Pan Pacific Symposium 2020.
- “Inkjet Printing for Printed Electronics,” by Ashlok Sridhar, Fraunhofer Research Institute for Electronic Nano Systems (ENAS), Material Matters, Volume 6 Article 1, 2019.
Happy Holden has worked in printed circuit technology since 1970 with Hewlett-Packard, NanYa Westwood, Merix, Foxconn, and Gentex. He is currently a contributing technical editor with I-Connect007, and the author of Automation and Advanced Procedures in PCB Fabrication, and 24 Essential Skills for Engineers.
This column originally appeared in the August 2022 issue of PCB007 Magazine.
More Columns from Happy’s Tech Talk
Happy’s Tech Talk #40: Factors in PTH Reliability—Hole VoidsHappy’s Tech Talk #39: PCBs Replace Motor Windings
Happy’s Tech Talk #38: Novel Metallization for UHDI
Happy’s Tech Talk #37: New Ultra HDI Materials
Happy’s Tech Talk #36: The LEGO Principle of Optical Assembly
Happy’s Tech Talk #35: Yields March to Design Rules
Happy’s Tech Talk #34: Producibility and Other Pseudo-metrics
Happy’s Tech Talk #33: Wet Process Management and Control