-
- News
- Books
Featured Books
- pcb007 Magazine
Latest Issues
Current IssueInventing the Future with SEL
Two years after launching its state-of-the-art PCB facility, SEL shares lessons in vision, execution, and innovation, plus insights from industry icons and technology leaders shaping the future of PCB fabrication.
Sales: From Pitch to PO
From the first cold call to finally receiving that first purchase order, the July PCB007 Magazine breaks down some critical parts of the sales stack. To up your sales game, read on!
The Hole Truth: Via Integrity in an HDI World
From the drilled hole to registration across multiple sequential lamination cycles, to the quality of your copper plating, via reliability in an HDI world is becoming an ever-greater challenge. This month we look at “The Hole Truth,” from creating the “perfect” via to how you can assure via quality and reliability, the first time, every time.
- Articles
- Columns
- Links
- Media kit
||| MENU - pcb007 Magazine
Estimated reading time: 5 minutes
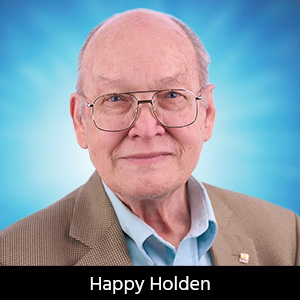
Contact Columnist Form
Happy’s Tech Talk #12: Nano-Cu Paste for Microvias
Complex build-up HDI technologies continue to expand in applications. Copper electroplating of vias has been perfected but the process is yet another electroplating solution to maintain and can sometimes be a lengthy process. Current conductive paste fills are not as conductive as solid copper but provide reduced cycle time, are still highly conductive, and are cost effective.
Introduction
Karl Dietz wrote on this topic several times in his Tech Talk series. No less than five separate columns were devoted to nanotechnology and conductive via-fill. The via-fill Tech Talk columns are titled:
- “The Dilemma of Innovation” (CircuiTree, October 2000)
- “Processes For HDI” (CircuiTree, December 2000)
- “Via Fill” (The PCB Magazine, July 2006)
- “Nano-particles in Electronics” (The PCB Magazine, October 2008)
- “Conductive Pastes and Inks” (The PCB Magazine, May 2011)
Metallizing Pastes
The metal-filled pastes have been around a long time. First used in the early 1960s for conductive jumpers and to connect double-sided non-plated through-hole (PTH) printed circuit boards with silver inks, their use has expanded over the years. An innovation came about in the mid-1980s with ORMET’s development of the transient liquid phase sintering (TLPS) conductive pastes that would sinter into a solid metal structure. This was used for conductive traces, board-to-board multilayering, and inner layer fabrication, as seen in Figure 1.
Many of the metallized pastes were originally used as via connections in the Japanese HDI process created in the early 2000s, such as ALIVH (any layer internal via hole), B2IT, or PALUP. These pastes used conductive particles and were different from nano-technology pastes or TLPS pastes.
The advantages of these newer pastes were:
- Improved reliability (avoidance of trapped air or liquids)
- Improved planarity of multilayer structures (for more reliable surface mount or improve photolithography)
- Higher interconnect density (e.g., via in pad vs. dog bone designs)
- Better thermal management
- Enable stacked microvia structures
Fabrication Process
The via filling process (Figure 2) is quite common today. Automatic equipment is available as well as simple prototyping apparatus. Screen printing or inkjet is now the most common method.
Material Properties
The silver-laden conductive pastes have been around since the early 1960s. The introduction of nanotechnologies has revolutionized these conductive pastes. The Holy Grail of conductive pastes has been copper-based or carbon-nanotube based. But even the best nanoparticle pastes exhibit a bulk resistivity more than 20 times that of bulk plated copper. The latest to be developed is a nano-copper particle that is coated to prevent oxidation, allowing air handling of the paste. By mixing the nanoparticles with micron-sized copper particles, resistivities of only six times that of bulk copper have been achieved2.
Transient Liquid Phase Sintering Pastes
The most electrically and thermally conductive metallic pastes are those that are TLPS. These are metallic pastes that combine small particles of solder materials (many nanoparticles) with small particles of solderable metals in a fluxing polymer binder. After sintering and during lamination of the subassembly cores or blind vias into a single PCB, the solder particles melt, wet the solderable particles, and form an interconnected metallic mesh. The metallic mesh formed has a melting point higher than the original solder alloys and is therefore stable through subsequent thermal excursions such as lead-free assembly operations. The solder particles also wet to the copper caps on the PTHs, the caps become permanently metallurgically bonded to the metal mesh of the sintered paste interconnect, and deliver a continuous and robust thermal and electrical conduction through sintered metal joints. Table 1 shows the testing of this type of paste.
Via Filling Experiments
Even though the resistivity of these nano-pastes is higher than bulk plated copper, the ideal application is for filling blind vias, as they are small and less sensitive to the resistivity. Table 2 shows the results of tests conducted on 125 um (0.005") diameter blind vias of various depths drilled into different substrates and subsequently filled with the nano-copper conductive pates and sintered. The samples were both etched into pads and left as copper-clad panel-plated specimens. Sintering was conducted either by an 808 nm diode laser, photonic flash tube (BB flash) or baked at a reduced temperature in a reducing environment.
In other studies, copper paste was used as a filling material for through-silicon vias (TSV), through-glass vias (TGV), and organic substrates. Non-through-holes with diameters of 10-60 mm and depths of 90-150 mm formed in the substrate surface layer were filled with the Cu paste, as well as through-holes with diameters of 30-300 mm for Si and glass, and 140-3000 mm for the organic substrates. All the pastes were sintered, and the results are seen in Table 34. The process is seen in Figure 3 using a vacuum frame and press plate to fill the vias.
Sintering
Sintering refers to a process where a mixture of particles is fused together, usually thermally. Sintering mixtures can be used as structures, dielectrics, and conductors. Conductive sintering products have been used in electronics for some time with ceramic thick-film technology (cermet). Cermets require high temperatures (>800°C) for sintering while conductive pastes based on polymers sinter at much lower temperatures (5 that will sinter the conductors without heating the substrate.
Conclusion
When considering the process of filling blind-vias or through-hole vias with plating, the new conductive copper-based TLPS pastes are faster, nearly as conductive, and possibly lower in cost than the plating process. In addition, the use of photonic soldering/sintering makes these conductive pastes practical on lower cost substrates such as paper, plastic films, or other organic materials not suitable for immersion in acid plating baths.
References
- Tatsuta, all4-pcb.us.
- “Nano-Copper Paste for Solid Copper Via Fill,” by Sujatha Ramanujan, IPC APEX EXPO 2015.
- “PTH Core-to-Core Interconnect Using Sintered Conductive Pastes,” by Michael Matthews, et al, IPC APEX EXPO 2012.
- “Cu Conductive Paste as Via Filling Materials for Through Silicon Via and Through Glass Via,” SMTA International, Nov. 15, 2021.
- “Photonic Soldering,” by Happy Holden, PCB007 Magazine, December 2021.
Happy Holden has worked in printed circuit technology since 1970 with Hewlett-Packard,?NanYa?Westwood, Merix, Foxconn, and Gentex. He is currently a contributing technical editor with I-Connect007, and the author?of?Automation and Advanced Procedures in PCB Fabrication, and?24 Essential Skills for Engineers.?
This column originally appeared in the September 2022 issue of PCB007 Magazine.
More Columns from Happy’s Tech Talk
Happy’s Tech Talk #42: Applying Density Equations to UHDI DesignHappy’s Tech Talk #41: Sustainability and Circularity for Electronics Manufacturing
Happy’s Tech Talk #40: Factors in PTH Reliability—Hole Voids
Happy’s Tech Talk #39: PCBs Replace Motor Windings
Happy’s Tech Talk #38: Novel Metallization for UHDI
Happy’s Tech Talk #37: New Ultra HDI Materials
Happy’s Tech Talk #36: The LEGO Principle of Optical Assembly
Happy’s Tech Talk #35: Yields March to Design Rules