-
- News
- Books
Featured Books
- pcb007 Magazine
Latest Issues
Current IssueInventing the Future with SEL
Two years after launching its state-of-the-art PCB facility, SEL shares lessons in vision, execution, and innovation, plus insights from industry icons and technology leaders shaping the future of PCB fabrication.
Sales: From Pitch to PO
From the first cold call to finally receiving that first purchase order, the July PCB007 Magazine breaks down some critical parts of the sales stack. To up your sales game, read on!
The Hole Truth: Via Integrity in an HDI World
From the drilled hole to registration across multiple sequential lamination cycles, to the quality of your copper plating, via reliability in an HDI world is becoming an ever-greater challenge. This month we look at “The Hole Truth,” from creating the “perfect” via to how you can assure via quality and reliability, the first time, every time.
- Articles
- Columns
- Links
- Media kit
||| MENU - pcb007 Magazine
Victory Giant Technology to Showcase Carbon Footprint Calculator at PCB West 2022
October 3, 2022 | Victory Giant TechnologyEstimated reading time: 1 minute
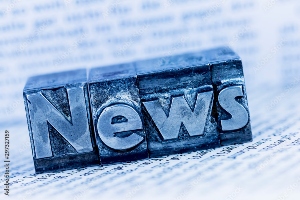
Victory Giant Technology, the fastest growing publicly traded PCB fabricator in China today announced they will showcase a new software tool for calculating total carbon emissions for any PCB design.
VGT’s Executive VP & CTO George Dudnikov commented, “VGT has been addressing the reduction of Green House Gases (GHG) and improved Sustainability of the PCB process since 2011. Through the continued focus on process automation and electricity/water conservation efforts, the company has saved 106,624,100 Kwh of electricity and reduced carbon emissions by 37,507 tons of CO2 through Jan 2021. Our data collection and process monitoring methods have been certified to GB/T 23331-2020, ISO 50001-2018, and RB/T-101-2013 standards.” The company has been recognized by the Chinese Government as a leading “ Green Manufacturer”.
We were asked by several large OEM customers if we could develop a method to quantify the environmental impact of specific PCB part numbers so that they could use the information to optimize and reduce the carbon emissions of their PCBs in support of their corporate Sustainability Initiatives. We had the data for key PCB processes but needed a way to add material ( laminate, copper foil, and prepreg ) contributions and effects of special processes like sequential lamination, VIPPO, HDI, etc. Tools available on the market were too generic and could not support the process complexity of an advanced PCB design. As we had experience with several PCB stackup tools, we saw a natural opportunity for a joint development project to develop a CFP Calculator.”
Visitors to the Victory Giant Technology Booth 303 will be able to obtain the following information:
- Meet with representatives from VGT to review Sustainability accomplishments and get a demo of the CFP Calculator tool.
- Arrange for a free Carbon Footprint analysis of any design based on Gerber data.
- Review VGT’s other capabilities for advanced HDI and High-Speed PCBs
Testimonial
"We’re proud to call I-Connect007 a trusted partner. Their innovative approach and industry insight made our podcast collaboration a success by connecting us with the right audience and delivering real results."
Julia McCaffrey - NCAB GroupSuggested Items
50% Copper Tariffs, 100% Chip Uncertainty, and a Truce
08/19/2025 | Andy Shaughnessy, I-Connect007If you’re like me, tariffs were not on your radar screen until a few months ago, but now political rhetoric has turned to presidential action. Tariffs are front-page news with major developments coming directly from the Oval Office. These are not typical times. President Donald Trump campaigned on tariff reform, and he’s now busy revamping America’s tariff policy.
Global PCB Connections: Understanding the General Fabrication Process—A Designer’s Hidden Advantage
08/14/2025 | Markus Voeltz -- Column: Global PCB ConnectionsDesigners don’t need to become fabricators, but understanding the basics of PCB fabrication can save you time, money, and frustration. The more you understand what’s happening on the shop floor, the better you’ll be able to prevent downstream issues. As you move into more advanced designs like HDI, flex circuits, stacked vias, and embedded components, this foundational knowledge becomes even more critical. Remember: the fabricator is your partner.
MKS’ Atotech to Participate in IPCA Electronics Expo 2025
08/11/2025 | AtotechMKS Inc., a global provider of enabling technologies that transform our world, announced that its strategic brands ESI® (laser systems) and Atotech® (process chemicals, equipment, software, and services) will showcase their latest range of leading manufacturing solutions for printed circuit board (PCB) and package substrate manufacturing at the upcoming 17th IPCA Show to be held at Pragati Maidan, New Delhi from August 21-23, 2025.
MKS Showcases Next-generation PCB Manufacturing Solutions at the Thailand Electronics Circuit Asia 2025
08/06/2025 | MKS Instruments, Inc.MKS Inc, a global provider of enabling technologies that transform our world, today announced its participation in Thailand Electronics Circuit Asia 2025 (THECA 2025), taking place August 20–22 at BITEC in Bangkok.
Point2 Technology, Foxconn Interconnect Technology Partner to Revolutionize AI Cluster Scalability with Terabit-Speed Interconnect
08/06/2025 | BUSINESS WIREPoint2 Technology, a leading provider of ultra-low-power, low-latency mixed-signal SoC solutions for multi-terabit interconnect, and Foxconn Interconnect Technology (FIT), a global leader in precision interconnect solutions, have signed a Memorandum of Understanding (MOU) to accelerate the commercialization of next-generation Active RF Cable (ARC) and Near Pluggable e-Tube (NPE) solutions.