-
- News
- Books
Featured Books
- pcb007 Magazine
Latest Issues
Current IssueInventing the Future with SEL
Two years after launching its state-of-the-art PCB facility, SEL shares lessons in vision, execution, and innovation, plus insights from industry icons and technology leaders shaping the future of PCB fabrication.
Sales: From Pitch to PO
From the first cold call to finally receiving that first purchase order, the July PCB007 Magazine breaks down some critical parts of the sales stack. To up your sales game, read on!
The Hole Truth: Via Integrity in an HDI World
From the drilled hole to registration across multiple sequential lamination cycles, to the quality of your copper plating, via reliability in an HDI world is becoming an ever-greater challenge. This month we look at “The Hole Truth,” from creating the “perfect” via to how you can assure via quality and reliability, the first time, every time.
- Articles
- Columns
- Links
- Media kit
||| MENU - pcb007 Magazine
Estimated reading time: 7 minutes
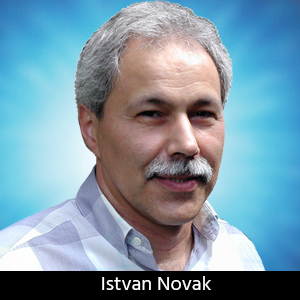
Quiet Power: Noise Mitigation in Power Planes
Inductive kick has been a well-known phenomenon in the electronics industry from very early on. First associated with motors, AC mains transformers and mechanical relays, people noticed large voltage spikes when the current-carrying circuit was opened. Later, as more sophisticated electronic circuits emerged, the same thing was noticed any time current was changing through an inductor, or for that matter, through any inductance, whether it was an intentionally placed discrete inductor piece or just the parasitic inductance associated with a current path. This phenomenon is captured by the third Maxwell equation, which describes Faraday’s Law1. In its simple form we know this rule from signal integrity as it describes the Dv ground bounce as a function of the dI/dt rate of change of current through an inductance of L:
In today’s electronics, the components are held and connected by printed circuit boards, which have been around for several decades. The front and back side of a small printed circuit board I designed, etched and populated in the late 1960s, are shown in Figure 1.
It was the audio amplifier for a battery-powered portable radio using all germanium transistors. The printed circuit board dielectric was unreinforced, fairly brittle, and to connect all components it was enough to use copper traces only on the back side of the board. The power and ground nets were carried by the wider etches near the two edges of the board. Being an analog audio amplifier using low-frequency transistors with a transit frequency in the order of a megahertz, the circuit did not create high-frequency or high-speed noise, and to carry power around simple traces with no special high-frequency bypassing was sufficient. Though the L inductance of the widely-spaced power and ground traces must have been very high, possibly in the tens of nHs, the noise across it was low because the dI/dt rate of current change was even smaller.
Fast-forward about 50 years; Figure 2 shows the front and back of a CPU module from the late 2010s2. I designed the power distribution network for this board that consumed hundreds of watts, had 20+ layers, and used several hundred bypass capacitors. The board had multiple solid ground layers and multiple power planes for the high-current supply rails. The power and ground planes in close proximity produced very low inductance in the tens of picohenries range, which was necessary to counter the high dI/dt of the chip.
Large power planes provide not only lower inductance, but they are also necessary to keep the DC voltage drop low. However, power planes come with some downsides as they produce resonances that can interfere with both the power delivery, or most likely, with our high-speed signaling. We know that signal traces will resonate if we don’t terminate them properly. Even with proper terminations at the ends, additional reactances along the signaling channel can create quarter-wave or half-wave resonances3. Traces are one-dimensional transmission lines, exhibiting a series of modal resonances associated with their length. Traces are one-dimensional, because we must keep the trace width and dielectric separation much smaller than the shortest wavelength of interest. In contrast, planes are two-dimensional resonators and rectangular plane pairs exhibit modal resonances both along their length and width4,5. As an illustration, Figure 3 shows a simulated impedance surface created by the standing-wave pattern on a 2:1 aspect ratio rectangular plane pair.
Depending on the resonance frequencies and the functionality of our circuit on the board, the standing waves and resonances can create issues in any of our major disciplines: signal integrity, power integrity, or electromagnetic compatibility. At locations and frequencies where the impedance is high, a signal via going through the power-ground plane cavity will introduce a dip in the trace’s transfer function (S21), which could be a signal-integrity problem. At the same locations and frequencies, power noise will be higher and if at those frequencies there is sufficient excitation energy from our circuit, the conducted noise can create power integrity issues and the circuit potentially could also radiate enough to create electromagnetic compatibility issues.
If we determine that the resonances could impose a risk to the operation of our circuit, we have a few options to deal with it. One possibility is to push the resonance frequencies high enough that our high-speed signals or power noise from our circuit will not excite them. Since we often use power planes to feed multiple electronic devices on our boards, this possible solution depends on how many devices we need to feed and what are our constraints for their placement. If this mitigation does not work, we must find a way to suppress the modal resonances. One “easy” solution is if the density of our bypass capacitors becomes so high that eventually the cumulative impedance of bypass capacitors become dominant at the resonance frequencies.
While this is a practical possibility and may often happen in very dense and physically small applications, large boards may require too many components to make this a viable option. Another alternative is to use power-ground plane pairs on thin enough laminates that naturally will suppress modal resonances. As it was explained and documented6, the natural attenuation of a power-plane pair increases with decreasing dielectric thickness. With medium and large size boards, a dielectric thickness of 25 mm (1 mil) or less greatly suppresses the resonances. As an illustration, Figure 4 shows measured transfer impedance plots on the same board design manufactured with different dielectric thickness values.
However, laminates thinner than 75 mm (3 mils) come with a price premium, and we also need to consider the usual stackup requirements calling for symmetry. This means we cannot just use one thin laminate layer, we need to use them in pairs in the stackup, even if the circuit would otherwise require only one. Also, in case only a smaller portion of a larger board would require the suppression of plane resonances, we will end up with the same thin laminate horizontally everywhere on the board, also where you don’t really need it. In those applications we can consider another potential solution: terminating the planes7, just as we reduce trace resonances by connecting the proper termination resistance to both ends. Since planes do not have well-defined “ends,” as traces do, we need to connect termination components along their periphery. Power-plane pairs, except for a few special shapes, do not have a specific characteristic impedance and therefore we need to rely on approximations, such as this approximation of a rectangular plane pair with X and Y horizontal dimensions:
Where
Zp is the approximate characteristic impedance of the plane pair in ohms
er is the relative dielectric constant of the laminate
h and P are the laminate thickness and periphery in arbitrary, but identical units
With typical plane sizes and laminate thickness values we use today, the impedance comes out in the tens to hundreds of milliohms range. We need to match this impedance with a number of termination elements, placed around the plane periphery. The number of elements depends on our frequency of interest. We need to make sure that up to the highest frequency of interest, often chosen as the tenth harmonic in the modal resonance series, the phase difference between adjacent termination components is much less than 90 degrees. As a result, we typically end up with a centimeter or so spacing. We then take the P periphery of plane shape and divide by the spacing between adjacent elements and it gives us the N number of terminations. Each termination resistor has to have an N*Zp value; many times it comes out as a few ohms. We also add a small series capacitor in series to each termination resistor to avoid shorting the power-ground plane pair with the termination resistance.
Terminating power planes was an attractive and viable solution a couple of decades ago when computer systems still had a lot of single-ended signaling and fewer supply rails with larger planes. In these days it still could be a viable alternative if system constraints prevent us from placing bypass capacitors to their optimum location. An example of plane termination on a recent computer board in volume production was described in a paper presented at DesignCon in 20218. In this case, the very high density of memory sockets ruled out the placement of bypass capacitors next to the power pins of memory sockets. The simulated and measured impedance of that supply rail is reproduced in Figure 5. Note the logarithmic vertical scale; using the proper termination components, the peak impedance was reduced by at least a factor of two.
Conclusion
Power planes provide a convenient means to connect multiple loads to a single power rail, but they introduce a series of modal resonances. The resonances can be suppressed by many bypass capacitors, or by using sufficiently thin dielectrics or by placing termination components along the plane periphery.
References
- For an introductory overview and summary, see for instance, https://byjus.com/physics/maxwells-equations.
- “Is Power Integrity the Next Black Magic?” Keynote webinar talk at E-learning By Cadence, April 12, 2021.
- “Those Pesky Half-Wave Resonances,” by Gustavo Blando, Signal Integrity Journal, Oct. 19, 2021.
- “Microstrip antenna technology,” by K.R. Carver and J.W. Mink, IEEE Transactions on Antennas and Propagation, AP-29, 1981, pp. 2-24.
- Frequency Domain Characterization of Power Distribution Networks, Artech House, July 2007, ISBN-13: 978-1-59693-200-5.
- “SUN’s Experience with Thin and Ultra-Thin Laminates for Power Distribution Applications,” DesignCon 2006, Santa Clara, CA, Feb. 6–9, 2006.
- “Distributed Matched Bypassing for Power Distribution Network,” IEEE Tr. CPMT, August 2002.
- “Impact of Power Plane Termination on System Noise,” DesignCon 2021, San Jose, CA, Aug. 16–18, 2021.
This column originally appeared in the October 2022 issue of Design007 Magazine.
More Columns from Quiet Power
Quiet Power: An Evolution in PCB Design CostsQuiet Power: The Effect on SI and PI Board Performance
Quiet Power: 3D Effects in Power Distribution Networks
Quiet Power: Uncompensated DC Drop in Power Distribution Networks
Quiet Power: Ask the Experts—PDN Filters
Quiet Power: Friends and Enemies in Power Distribution
Quiet Power: Be Aware of Default Values in Circuit Simulators
Quiet Power: Do You Really Need That Ferrite Bead in the PDN?