SMT Tooling, PSA: 'Perfect Marriage of Innovation and Product'
October 26, 2022 | Nolan Johnson, I-Connect007Estimated reading time: 4 minutes
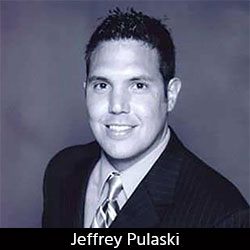
Jeffrey Pulaski describes the recent partnership between SMT Tooling and PSA, which brings SMT Tooling’s innovation and PSA’s manufacturing capabilities together. Pulaski also shares news on product development, and what visitors to SMTA International can expect to see in SMT Tooling’s floor presence.
AUDIO INTERVIEW TRANSCRIPT:
Nolan Johnson: Joining me for this conversation is Jeffrey Pulaski. He is a project manager at SMT Tooling. Jeffrey, thanks for joining me.
Jeffrey Pulaski: Nolan, thank you. It’s a pleasure to be here with you.
Johnson: It’s been in the news recently that SMT Tooling and Production Systems Automation, Incorporated, PSA has joined forces in some fashion. Can you talk to us about that?
Pulaski: Production Systems Automation is owned by Michael McHale, and it deals mainly with automation, machinery, and robotics. We have a contract in the DoD with some drone work, contract work. Now one of the divisions is SMT Tooling, and that came about through Michael and Charlie Moncavage’s relationship.
Johnson: I presume then that there are some market conditions or developments that are helping fuel this partnership. What might those be?
Pulaski: Michael’s interest is always pretty broad. He’s an entrepreneur. And him and Charlie’s relationship is very fruitful for them both. Charlie has been the previous inventor of Grid-lok and Quick-tool, and now his latest rendition of the board support that started this venture is Matrix, so that’s what we’re producing. The market called for tighter tolerances with the way that industry is going with pin placement and tighter tolerance is required. The retooling of Charlie’s invention and the development of Matrix has been a perfect marriage. PSA’s facilities—we have three, one in western Pennsylvania in Lawrence; the main one in Duryea, which is northeast Pennsylvania; then down in Aston toward Philadelphia—we have over 80 plus engineers in house manufacturing facilities and fabrication facilities throughout our campus.
Johnson: So, how do the core competencies for the two companies benefit each other?
Pulaski: So, with Charlie’s innovation of the tooling and Michael’s extensive knowledge of manufacturing and automation, equipment, and fabrication, as the two merged together, it just was a perfect marriage of innovation and product. We’re going to take Charlie’s invention to the next level. We could control the quality of the products put out better. We have elaborate inspection stations and the fabrication portion of PSA, along with its connections throughout the industry is a great place for SMT Tooling to get a lot of traction in the industry.
Johnson: For those who aren’t maybe that familiar with your product, you’ve mentioned, let’s talk a little bit more about that.
Pulaski: Sure. Matrix is a module that is pin-driven. It’s an under-board support for PCBs surface mount tool. This is a revised rendition of the previous invention that Charlie had, Quick-tool, made better. I should say maintenance-free, the production is better, the tolerances are better, pin placement is tighter. So, along with the updates coming through the industry with the PCBs and the tighter tolerance is required for support. Matrix provides that, which no other company can. We right now produce 12-inch, 15-inch, 18-inch, up to 24-inch, but we could do custom sizes. We had produced one as big as 48 inches, which was unprecedented in the industry.
Johnson: Who would be a target user for the Matrix product? There must be some applications for which this just shines.
Pulaski: Yes, of course. Solder paste printers, pick and place machines. Anyone that’s in the PCB production industry that has those machines within their facility, we could help support.
Johnson: What makes the SMT Tooling products and your processes so unique in the industry?
Pulaski: Well, it goes back to that relationship with Michael and Charlie. PSA’s well-established within the automation community and robotics. We have an extensive machine shop, inspection stations. All the work is done in-house. It’s all American made. Charlie’s device is all built within our facility at SMT Tooling. There’s very little outsourcing. Everything is produced right within our facility, so we could control exactly how this is built and inspected; it just makes for a better product.
Johnson: Will you be present at SMTA International in the beginning of November?
Pulaski: Yes, we will. Well, we’re looking forward to that show. We just came from a Long Island show yesterday, and our product was very well received. Along with Matrix, we are planning on launching our own version of a screen printer called the Marksman. It’s a tabletop semi-automatic screen printer targeting the $10,000 to $12,000 price range for low production run, high quality. It entails integrated vision and alignment systems. It’s preconfigured to accept Matrix, which kind of ties the two products together. We’re really excited about this. There’s a lot of innovation that is put into this, and we believe it’s going to offer a lot to the customer, the end user. We will have Matrix at the show and SMTAI coming up here shortly.
Johnson: Thank you for taking the time to talk with us today.
Pulaski: Thank you. My pleasure.
Suggested Items
Geena Bowen Joins Electra Polymers as Inkjet LaboratoryTechnician
02/24/2025 | Electra Polymers LtdElectra Polymers Ltd, a global leader in specialty materials for the PCB industry, is delighted to welcome Geena Bowen to its inkjet development team as an Inkjet focused laboratory technician. Geena brings a strong scientific background with a distinction in MSc Biomedicine and a First-Class BSc (Hons) in Biomedical Science further enhancing Electra’s capabilities in advancing sustainable PCB solutions.
AIM to Highlight REL61™, W20, and Ultrafine Paste Offerings at Productronica China
02/19/2025 | AIMAIM Solder, a leading global manufacturer of solder assembly materials for the electronics industry, is pleased to announce its participation in the upcoming Productronica China, taking place March 26-28 at the Shanghai New International Expo Center.
EIPC 2025 Winter Conference, Day 1: From Manufacturing to Sustainability
02/19/2025 | Pete Starkey, I-Connect007The EIPC 2025 Winter Conference, Feb. 4-5, in Luxembourg City, featured keynotes and two days conference proceedings. This is my report of the first day’s conference proceedings. The keynote session and second-day conference proceedings are reported separately.
SolderKing Doubles Facility to Meet Growing Demand
02/18/2025 | SolderKingSolderKing, a leading UK manufacturer of soldering materials, has expanded its operations by doubling its facility. The move follows a significant rise in export sales throughout 2024 and reinforces the company’s position as a key supplier of regulatory-compliant soldering solutions across the UK and Europe.
Electra Polymers Ltd Becomes Primary Inkjet Soldermask Supplier for TLT PCB, an Affiliated Teltonika Company
02/18/2025 | Electra Polymers LtdElectra Polymers Ltd, a global leader in inkjet materials for the PCB industry, is proud to announce a new partnership with high-tech design and manufacturing company TLT PCB, an affiliated company of Teltonika, becoming the primary supplier of inkjet soldermask for TLT PCB’s new manufacturing facility in Vilnius, Lithuania.