Estimated reading time: 4 minutes
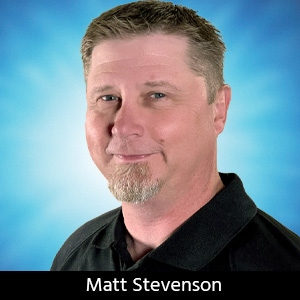
Connect the Dots: Five Best Practices for Designing Flex and Rigid-flex PCBs
Flex and rigid-flex PCBs represent exciting technology for designers. Suddenly, boards no longer need to exist along one plane—or along a flat plane at all. Designs can now conform to specific shapes or be bent during use, and this opens new possibilities for applications with space constraints or flexibility requirements.
Built using materials that can bend, a flex PCB is usually constructed with materials like polyimide and polyester film. These PCBs have many properties that designers might find useful beyond their flexibility. They have improved resistance to both vibration and movement. They are also significantly thinner and lighter than traditional rigid PCBs.
Flex PCBs do have some drawbacks, however. They can be more expensive to manufacture, and extra care needs to be taken for large or heavy components that may not be able to handle the flex. When these drawbacks seem problematic, rigid-flex PCBs are probably the best way to go.
Rigid-flex PCBs combine traditional rigid PCBs with flexible connectors. This approach offers better durability and mechanical stability compared to flex PCBs. While designs may lose some of the versatility of flex PCBs, combining traditional rigid PCBs and flexible elements brings the best of both approaches.
Five Best Practices for Designing Flex and Rigid-flex Circuits
Of course, adapting to these new materials requires learning about their capabilities and restrictions, as well as learning a new set of design rules and best practices. Here are five best practices to get you started on your first flex or rigid-flex PCB design.
Before exploring these best practices, consider whether your PCB will be used in a static flex application—that is, it just needs to flex once during installation—or if it will be in a dynamic flex application. This important distinction can impact your design decisions.
1. Use curved paths for your flex traces.
Sharp angles can cause weak points in your traces across flex PCB segments. They tend to concentrate mechanical stress along the angles, so if you use curved paths for flex points, you will avoid cracking and weakening connections. This is particularly important in dynamic flex applications, where traces and conductors are subjected to repeated bending.
2. Use fillets to connect your traces to pads.
A widened fillet can help reduce stress at connection points between traces and pads, greatly increasing the robustness of your design. Teardrop and rounded trace designs can reduce stress concentration points and prevent potential cracking or peeling around connections.
3. Make allowances for the coverlayer.
Unlike rigid PCBs, flex PCBs require an additional coverlayer to protect circuits and maintain flexibility. It is important that the coverlayer leaves room for various features of the PCB and for the interaction between the coverlayer and the flex board.
First, the coverlayer needs to be drilled to create access to the pad for soldering. However, it is important that the adhesive isn't squeezed out onto the pads. To accommodate for this, coverlayer drill holes need to be 0.005–0.010" larger than the land area.
In addition, this same allowance needs to be made for clearance holes in the coverlayer around through-holes in the flex PCB.
4. Layout considerations to be made for conductors and traces in dynamic flex areas.
Conductors need to be evenly staggered across areas of the board that will see regular flexing. If the circuit is repeatedly flexed perpendicular to the conductors, stress will occur in the same location. This will cause any isolated conductors to crack prematurely.
However, when conductors are routed and staggered evenly, an isolated stress condition cannot develop. This ensures that no premature failure will occur.
In addition, be careful to avoid traversing conductors in the bend area. This can cause additional mechanical stress and can lead to cracking and failing traces.
5. Plan adequately for strain relief fillets.
Strain relief fillets are intended to prevent conductors from cracking during installation and are an important part of rigid-flex PCBs. Usually made from a two-part, epoxy-based material, its main purpose is to prevent flex circuits from being bent at the transition point between flex and rigid PCBs. However, this material can also protect flex PCB portions from being damaged by “prepreg squeeze-out,” which can create sharp edges along the sides of rigid PCB components.
Best Practices Make for Smooth Manufacturing
Flex and rigid-flex PCBs have opened a world of possibilities for designers. Their ability to conform to various shapes, along with a reduction in weight and size, has revolutionized the electronics industry. Designers now have the freedom to imagine and create products that were once limited by the constraints of rigid boards.
However, as with any new design component, we must remember the importance of following best practices when designing flex and rigid-flex PCBs. Attention to these details helps ensure optimal performance and reliability. Collaboration with experienced PCB manufacturers is also important for a smooth and reliable production experience.
Flex and rigid-flex PCBs are ready for designers to embrace. It is an exciting time when imagination and vision can be put to work to shape the future of electronics.
Download The Printed Circuit Designer’s Guide to… Designing for Reality by Matt Stevenson. You can view other titles in the I-007eBooks library.
This column originally appeared in the January 2024 issue of Design007 Magazine.
More Columns from Connect the Dots
Connect the Dots: The Future of PCB Design and ManufacturingConnect the Dots: Proactive Controlled Impedance
Connect the Dots: Involving Manufacturers Earlier Prevents Downstream Issues
Connect the Dots: Stop Killing Your Yield—The Hidden Cost of Design Oversights
Connect the Dots: Designing for Reality—Routing, Final Fab, and QC
Connect the Dots: Designing for Reality—Surface Finish
Connect the Dots: Designing for Reality—Solder Mask and Legend
Connect the Dots: Designing for Reality: Strip-Etch-Strip