-
- News
- Books
Featured Books
- pcb007 Magazine
Latest Issues
Current IssueFueling the Workforce Pipeline
We take a hard look at fueling the workforce pipeline, specifically at the early introduction of manufacturing concepts and business to young people in this issue of PCB007 Magazine.
Inner Layer Precision & Yields
In this issue, we examine the critical nature of building precisions into your inner layers and assessing their pass/fail status as early as possible. Whether it’s using automation to cut down on handling issues, identifying defects earlier, or replacing an old line...
Engineering Economics
The real cost to manufacture a PCB encompasses everything that goes into making the product: the materials and other value-added supplies, machine and personnel costs, and most importantly, your quality. A hard look at real costs seems wholly appropriate.
- Articles
- Columns
Search Console
- Links
- Media kit
||| MENU - pcb007 Magazine
X2F Demonstrates Ground-breaking Molding Technology
November 3, 2022 | X2FEstimated reading time: 2 minutes
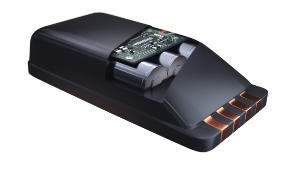
X2F is making waves with their breakthrough molding technology, unlocking new manufacturing capabilities for protecting electronics from heat. X2F’s unique technology molds highly filled and extremely viscous materials that are “impossible to mold” with today’s conventional approaches. Their innovative molding process provides a superior solution to potting and conformal coating when extreme thermal management is needed, and it improves thermal performance of the end product by as much as 200%.
Accomplishing the Impossible
Motivated by the tremendous need for high-performance thermally conductive solutions to dissipate heat from electronics used in a variety of industries, X2F developed a patented low-pressure and Controlled Viscosity Molding (CVM) approach. Typical difficult-to-mold materials such as highly filled thermally conductive hot melt adhesives, thermoplastic elastomers, polycarbonates, and nylons are no problem with X2F technology.
High-tech advances in a variety of industries have created electronics with more power and functionality. Today’s electronics require improved cooling methods to prevent overheating and ensure long-term reliable performance. For instance, printed circuit boards (PCBs) used to manage battery power in today’s power tools often develop hot spots during operation. These hot spots reduce the product’s lifespan by degrading battery charging and discharging performance. X2F technology eliminates hot spots via over-molding of electronics with highly filled thermally conductive materials. This type of thermal management is critical to achieving superior performance for today’s advanced electronics, batteries, and LED lighting.
Unique X2F Process
X2F’s technology delivers highly filled materials to the mold cavity via extruders that are designed specifically for X2F’s unique Extrude to Fill (“X2F”) process. The X2F process combines specialized hardware, sensors, software, and a process feedback loop. Utilizing electrically generated heat instead of high-pressure shearing, X2F technology precisely controls the pressure, temperature, and viscosity of the melted material throughout the molding process. And by continuously sensing mold cavity pressure and using their patented “pulse-pack” process, X2F molding can be performed at 70 to 90% lower pressure than traditional injection molding.
Faster Production
The X2F process easily molds highly filled materials at high-volume production speeds. Cycle times of 30 to 60 seconds are common with X2F, which is significantly faster than potting and conformal coating, which can take several hours. Companies can also expect ultra-fast prototyping from X2F – typically 5 to 10 business days for samples depending on the complexity. Their process even includes the ability to provide compounding at the press – adding fillers (ceramics, graphite, etc.) to impart added performance.
Enabling Innovation
In their recent collaboration with Covestro, X2F co-developed a thermally conductive automotive heat-sink with in-mold-electronics that was 49% lighter than traditional cast aluminum. And by eliminating the need for brackets, fasteners, thermal pastes, and adhesives, the X2F process was significantly less expensive. Covestro also saw improvements in thermal performance with the X2F solution compared to traditional injection-molding processes. This illustrates how X2F technology is enabling innovation. With X2F, previously un-moldable materials can be used, new higher-performance materials can be developed, and more intricate molded shapes can be designed.
“This innovative technology is a game-changer for the industry, helping to accelerate innovation and technology for new products with higher performance. Our molding technologies are eliminating barriers with materials everyone thought where impossible to mold. We can now streamline production, reduce manufacturing complexity, and add significant thermal enhancements to products with ever expanding performance requirements.” said Antonio Aceves, VP of Strategy & Business for X2F.
Suggested Items
Teledyne Completes Acquisition of Select Aerospace and Defense Electronics Businesses of Excelitas
02/05/2025 | BUSINESS WIRETeledyne Technologies Incorporated announced today the successful completion of the acquisition of select aerospace and defense electronics businesses from Excelitas Technologies Corp. (“Excelitas”) for approximately $710 million. The acquisition includes the optical systems business known under the Qioptiq® brand based in Northern Wales, UK, as well as the U.S.-based advanced electronic systems business.
Flexible Thinking: Mind-tapping into January
02/05/2025 | Joe Fjelstad -- Column: Flexible ThinkingIt’s January again, and our beleaguered planet has completed yet another trip around the sun. The Romans named January in honor of their god Janus, who is usually depicted as a bearded old man with two faces—one looking back to the past and the other looking forward to the future. People venerated Janus as the god of beginnings and endings, transitions, and the passage of time. With that in mind, I’ll look 10 years into the future—hopefully with a bit of inspiration from Janus—and prognosticate what might be happening in electronic design.
INEMI Launches Webinar on Ecological Footprint Minimization for Sustainable Electronics Roadmap
02/05/2025 | iNEMIJoin us for an insightful webinar as INEMI kicks off the development of additional content for the Sustainable Electronics Roadmap, focusing on ecological footprint minimization.
Jabil Recognizes Nordson Electronics Solutions with the 2024 Best Strategic Supplier Award
02/05/2025 | Nordson CorporationNordson Electronics Solutions, a global leader in electronics manufacturing technologies, has been honored with the 2024 Jabil Best Strategic Supplier Award, underscoring Nordson’s essential role in enabling Jabil, a global leader in manufacturing services, to achieve operational excellence and deliver exceptional value across its supply chain.
YINCAE Launches UF 120LA
02/04/2025 | YINCAEYINCAE has introduced UF 120LA, a high-purity liquid epoxy underfill engineered for advanced electronics packaging. With exceptional flowability into 20μ gaps, UF 120LA eliminates cleaning processes, reducing costs and environmental impact while ensuring superior performance across applications like BGA, flip chip, WLCSP, and multi-chip modules.