-
-
News
News Highlights
- Books
Featured Books
- pcb007 Magazine
Latest Issues
Current IssueThe Hole Truth: Via Integrity in an HDI World
From the drilled hole to registration across multiple sequential lamination cycles, to the quality of your copper plating, via reliability in an HDI world is becoming an ever-greater challenge. This month we look at “The Hole Truth,” from creating the “perfect” via to how you can assure via quality and reliability, the first time, every time.
In Pursuit of Perfection: Defect Reduction
For bare PCB board fabrication, defect reduction is a critical aspect of a company's bottom line profitability. In this issue, we examine how imaging, etching, and plating processes can provide information and insight into reducing defects and increasing yields.
Voices of the Industry
We take the pulse of the PCB industry by sharing insights from leading fabricators and suppliers in this month's issue. We've gathered their thoughts on the new U.S. administration, spending, the war in Ukraine, and their most pressing needs. It’s an eye-opening and enlightening look behind the curtain.
- Articles
- Columns
- Links
- Media kit
||| MENU - pcb007 Magazine
MKS' Atotech Embracing Digital Solutions for PCB Fabrication
November 10, 2022 | Nolan Johnson, I-Connect007Estimated reading time: 7 minutes
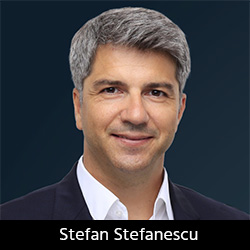
?MKS' Atotech continues to develop and release digital solutions within the Atotech product portfolio. In this conversation Stefan Stefanescu and Nolan Johnson, they discuss the work MKS' Atotech is engaged in, the problems to be solved, how this work will improve customer operations.
Nolan Johnson: I’m Nolan Johnson here for I-Connect007. I’m speaking currently with Stefan Stefanescu. He is the head of business development for Industrial Digital Solutions at MKS' Atotech. Stefan, welcome.
Stefan Stefanescu: Thank you, Nolan. Thank you for having me today.
Johnson: Well, as the head of Industrial Digital Solutions or the business development portion of that, update us on the digitalization work being done at MKS' Atotech.
Stefanescu: We have, since 2020, our internal software capabilities as we acquired our partner company that was building the visualization and control software for our equipment for almost 20 years. And with that, almost within a year, we made a strong move to have our own platform using industrial internal teams technology, digital twin, edge computing, and so on, to help our customers with digital solutions for our equipment.
What we are trying to solve with that is very, very clear. We have been very customer focused from the beginning, and the first thing that we wanted to do is we wanted to increase our customer focus. We wanted to reduce friction in our working with the customer and be closer with the customer by using those digital solutions. Number two, we wanted to help our customer increase their productivity, but also efficiency of the operation in the factory. Number three, we see a great opportunity to actually reduce bringing our solutions to the market, and reduce the R&D time by leveraging digital solutions.
And last but not least, there is a clear move of bringing manufacturing to a smart factory set up. And this is where our customers can build smart factories with digital solutions and also obviously with our equipment that we’re delivering to them.
Johnson: Why would Atotech go down a path such as this?
Stefanescu: Well, that’s a very good question. And as I mentioned, we acquired a software company, so we have this in-house. So there is a clear commitment that we wanted to do this. I will touch on three main points.
First, there is a clear demand of we’re having traceability and sustainability embedded in the manufacturing. And this is where we see digital solution has been a strong solution to solve and help our customer with this.
Number two, I mentioned productivity. I mean, the increase of production and reducing downtime is something that digital solution, using industrial internet of things, is something that can be delivered today. There were some buzzwords some years ago where people didn’t believe that this will bring value, but it actually does bring value.
And last is really about the fact that you almost do not have a choice anymore because you have partners, you have customers, that all moved to digitalization, all have their tools, and upstream, downstream, you cannot stay there and not have that because you’re not going to be part of their automation, and it forced you to do that.
And there is also another topic that is equally important, which is the fact that we need to ensure that our partners, our customers, can make a place also for the young generation in manufacturing, and how they going to use digital solutions as they are living in the digital world and how we make a factory attractive to this generation. And this is basically, we at Atotech, we are fully committed to bring our customers to a smart factory set up. And that’s why we made this move, and we are making it happen as it goes with our digital factory’s suite platform.
Johnson: What are some specific problems that a prospective customer should be bringing to you forth, with a digital solution?
Stefanescu: I will start with downtime. Downtime can cost as much as 20% of the production within a year, which is really about millions of dollars. Very, very painful. With digital solutions, we see the potential to reduce unplanned downtime basically by half. And how we do this, it’s by taking the data that is produced in the production by the equipment, putting it into the platform, model that data and allowing the engineers in the factory to have a different way to operate maintenance or quality inspections.
They do this directly at their desk. They have dashboards and they can monitor really the problems that they need to look at in comparison to what they do today, where they need to go to every individual equipment to check what issues might be, what needs to be planned in the maintenance, where with the digital solutions this can happen again at their desk.
And most important is that they can get alerts when there is an issue. So in the increased time of response is there. And that’s basically where downtime, as I mentioned, is a topic that we see a very high potential that can be solved with digitalization.
And there is another aspect, which in combination can make this even stronger, is remote service. I think that the pandemic situation showed how important that is, being forced not to travel and then we have to find solution. And it proved that it worked. And remote service is another aspect which contributes to increased speed of solving problems. And it’s also more sustainable because you don’t need to travel left and right, which I think brings value to everybody.
Johnson: Those certainly are two key solutions that are worthwhile investigating for a potential customer. That’s for sure.
Stefanescu: Yeah, I mean, again, there is more than that. So basically what we are doing with the data condition monitoring is one thing that allows the customer in almost real-time to see the performance of the equipment and the process, but at the same time, traceability. It’s equally important. By having this data and being able to go down to every panel and understand what was the performance during production, so that you can immediately do an investigation when you need to do that. When you have quality issues, you can also compare performance between different equipment or between processes within a second, just by clicking a button and basically getting that information.
And again, at your desk. Because today the engineers in the factory, they struggle to get this data, find this data, correlate this data, whereas with digital solutions, by leveraging the production data, this can be done immediately. And that saves a lot of time, a lot of time of people making them more efficient, because in the end digitalization is not about taking the people out but making them really efficient. And this is basically what we are aiming for.
And we can go further down in terms of what solution can be levered, but again, if we’re looking at condition monitoring, traceability, very important topics, remote service, those are things that can already boost the efficiency of the operation and reduce downtime, which I think everybody is looking at as that impacts production.
Johnson: I take it that the information you can get from the control software that you’re developing is also integrable across the rest of the manufacturing floor through industry standard protocols.
Stefanescu: Yes, it is. And we have been looking at that from the beginning because we wanted to make something that is scalable. It doesn’t bring our customers into a lock, so that they can leverage that. And there is also another aspect that we have been considering from the beginning, but it is clear that the data is an asset that is owned by the customers, and we have been serious about the security of this data, and that’s why we have designed our solutions in such a way that is deployed on premise. It means that all the security standards that applies to the local infrastructure of the customer applies also to the digital factory suite, bringing no risk in terms of data, and this is really important. Those two aspects make it scalable so that also other equipment can be integrated and have a solution that runs on premise. It’s secured. It is basically for us. It was very important to have it designed like that.
Johnson: Thank you for taking the time to update us on the impacts of digitalization and your work at MKS' Atotech. Thank you very much.
Stefanescu: Thank you, Nolan. And yeah, looking forward to continuing the conversation some other time. Have a good day.
Johnson: Here for I-Connect007, I’m Nolan Johnson. I’ve been speaking with Stefan Stefanescu. He is the head of business development for Industrial Digital Solutions at MKS' Atotech. And thanks for listening.
Suggested Items
TT Electronics Achieves ISO 13485 Medical Certification at Mexicali EMS Facility
06/27/2025 | TT ElectronicsThis milestone underscores TT Electronics’ commitment to delivering high-quality, compliant, and reliable manufacturing solutions to its global customers in healthcare and life sciences.
CEE PCB Appoints KT Technical Solutions as North American Sales Representative
06/23/2025 | CEE PCBStrategic Partnership Expands CEE PCB’s Reach into the North American Market with a Focus on Customer-Centric Service and High-Quality Manufacturing
Benchmark Strengthens Presence in Jalisco with Grand Opening of Advanced Manufacturing Facility in Guadalajara
06/21/2025 | BUSINESS WIREBenchmark Electronics, Inc., a global provider of engineering, design, and manufacturing services, celebrated the grand opening of its brand-new manufacturing facility in Guadalajara, Mexico.
PMGC Holdings Signs Letter of Intent to Acquire Profitable U.S.-Based Electronics Manufacturing Company
06/10/2025 | Globe NewswirePMGC Holdings Inc., a diversified public holding company, is pleased to announce the signing of a non-binding Letter of Intent (LOI) to acquire a U.S.-based, cash-flow positive electronics contract manufacturing company with over 40 years of operational history.
VeriSilicon’s AI-ISP Custom Chip Solution Enables Mass Production of Customer’s Smartphones
06/09/2025 | BUSINESS WIREVeriSilicon recently announced that its AI-ISP custom chip solution has been successfully adopted in a customer’s mass-produced smartphones, reaffirming the company’s comprehensive one-stop custom silicon service capabilities in AI vision processing.