-
-
News
News Highlights
- Books
Featured Books
- pcb007 Magazine
Latest Issues
Current IssueThe Hole Truth: Via Integrity in an HDI World
From the drilled hole to registration across multiple sequential lamination cycles, to the quality of your copper plating, via reliability in an HDI world is becoming an ever-greater challenge. This month we look at “The Hole Truth,” from creating the “perfect” via to how you can assure via quality and reliability, the first time, every time.
In Pursuit of Perfection: Defect Reduction
For bare PCB board fabrication, defect reduction is a critical aspect of a company's bottom line profitability. In this issue, we examine how imaging, etching, and plating processes can provide information and insight into reducing defects and increasing yields.
Voices of the Industry
We take the pulse of the PCB industry by sharing insights from leading fabricators and suppliers in this month's issue. We've gathered their thoughts on the new U.S. administration, spending, the war in Ukraine, and their most pressing needs. It’s an eye-opening and enlightening look behind the curtain.
- Articles
- Columns
- Links
- Media kit
||| MENU - pcb007 Magazine
The Growing Need for UHDI
November 30, 2022 | I-Connect007 Editorial TeamEstimated reading time: 3 minutes
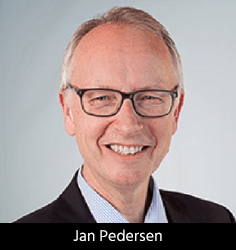
Jan Pedersen of NCAB Group is deeply involved in IPC standards development surrounding ultra HDI and keeps his finger on the pulse of the industry surrounding this type of fabrication. With Asia still dominating this area, Jan sees the need for U.S. and European PCB fabricators to make the investment if they want to stay competitive.
Nolan Johnson: Jan, you’re very involved in UHDI design and manufacturing. What’s your perspective on these topics within the industry now, and where UHDI is going?
Jan Pedersen: There are seven to 10 factories globally that can produce what we call ultra HDI. The definition for UHDI is 50-micron and below track and gap. You can use subtractive methods down to, let’s say, 35 or 40 microns, and then when you creep down below that level you need mSAP or xSAP technologies.
That has been around for many years. It’s not really a new technology. It was introduced into the packaging or the component industry in the 1970s and ‘80s, but it was brought up again when Apple and others started to do smartphones. There are those factories that are involved in this, but they are factored for one customer, so it’s very hard for a smaller customer to get into UHDI, and most companies are smaller than Apple.
If you are a bit smaller, you don’t get access. It’s simple as that. I’ve tried it myself, tried to place an order with a big European PCB group that claims they have the capability. But when you have your Gerbers and your data and you want to produce boards there, they say, “Oh, sorry. This is basically for one customer,” and they don’t accept us putting their competitors, which could be anybody, into the same factory.
Johnson: Given that, what is driving the development of UHDI?
Pedersen: For us, it’s coming from telecom and 5G, and you assume we’ll see 6G. But quite a few of our customers come from these industries. We see that need growing in the automotive and medical industries, and I’m discussing it almost globally. I’m looking to see if there is any availability of production capabilities in the U.S. today. We don’t find it. There’s one factory in Europe that has limited capacity, and then the rest are in Asia and producing for the big names.
Johnson: Where does HDI stop and UHDI begin?
Pedersen: Let’s use the ultra HDI definition of 50 microns down. It’s subtractive down to approximately 40 microns.
Where we are today approximately on BGA pitch below 350 microns, we talk about pads of 140, and then you are basically into mSAP or substrate-like PCB technologies, whatever that is. There are quite a few technologies out there now that can be used. But we see that we are going from a subtractive into an mSAP level; this depends on where you are coming from and how far you are coming with the investments in your factory, because some of the factories that are producing mSAP have invested in imaging, AOI—everything needed for that resolution now.
When you have a subtractive in that factor, they can go quite far down here. But if you don’t have all the other investments and just go for mSAP, that doesn’t help you.
I’m saying this as background because you have this producibility level C in IPC-2226, where you have 50-micron track and gap. Everything below that is ultra HDI—substrate-like PCBs can be produced by either subtractive or SAP-related technologies. If you go below that again, down to 15 to 20 microns, you need an embedded trace substrate or similar technologies. Then of course you come to high-end IC substrates which are in single microns.
In the U.S. today for substrate-like PCB, it’s below 50 microns, not touching 20 microns, but maybe 35 or 40. When I had my Gerbers and asked for quotations, they said they couldn’t do it. They do have mSAP equipment, if you can call it that, or a process in-house, but have not yet invested in the imaging and AOI that is able to detect down to 20 microns. I think they stop somewhere around 35 today.
To read this entire conversation, which appeared in the November 2022 issue of PCB007 Magazine, click here.
Suggested Items
IPC-CFX, 2.0: How to Use the QPL Effectively
07/02/2025 | Chris Jorgensen, Global Electronics AssociationIn part one of this series, we discussed the new features in CFX Version 2.0 and their implications for improved inter-machine communication. But what about bringing this new functionality to the shop floor? The IPC-CFX-2591 QPL is a powerful technical resource for manufacturers seeking CFX-enabled equipment. The Qualified Product List (QPL) helps streamline equipment selection by listing models verified for CFX compliance through a robust third-party virtual qualification process.
Advancing Aerospace Excellence: Emerald’s Medford Team Earns Space Addendum Certification
06/30/2025 | Emerald TechnologiesWe’re thrilled to announce a major achievement from our Medford, Oregon facility. Andy Abrigo has officially earned her credentials as a Certified IPC Trainer (CIT) under the IPC J-STD-001 Space Addendum, the leading industry standard for space and military-grade electronics manufacturing.
Magnalytix and Foresite to Host Technical Webinar on SIR Testing and Functional Reliability
06/26/2025 | MAGNALYTIXMagnalytix, in collaboration with Foresite Inc., is pleased to announce an upcoming one-hour Webinar Workshop titled “Comparing SIR IPC B-52 to Umpire 41 Functional & SIR Test Method.” This session will be held on July 24, 2025, and is open to professionals in electronics manufacturing, reliability engineering, and process development seeking insights into new testing standards for climatic reliability.
IPC Rebrands as Global Electronics Association: Interview With Dr. John W. Mitchell
06/22/2025 | Marcy LaRont, I-Connect007Today, following a major announcement, IPC is embracing the rapid advancement of technology with a bold decision to change its name to the Global Electronics Association. This name more accurately reflects the full breadth of its work and the modern realities of electronics manufacturing. In this exclusive interview, Global Electronics Association President and CEO Dr. John W. Mitchell shares the story behind the rebrand: Why now, what it means for the industry, and how it aligns with the organization’s mission.
Global Electronics Association Debuts; New Name Elevates IPC’s 70-Year Legacy as Voice of $6 Trillion Electronics Industry
06/25/2025 | Global Electronics AssociationToday begins a new chapter for IPC as it officially becomes the Global Electronics Association, reflecting its role as the voice of the electronics industry. Guided by the vision of “Better electronics for a better world,” the Global Electronics Association (electronics.org) is dedicated to enhancing supply chain resilience and promoting accelerated growth through engagement with more than 3,000 member companies, thousands of partners, and dozens of governments across the globe.