-
- News
- Books
Featured Books
- pcb007 Magazine
Latest Issues
Current IssueInventing the Future with SEL
Two years after launching its state-of-the-art PCB facility, SEL shares lessons in vision, execution, and innovation, plus insights from industry icons and technology leaders shaping the future of PCB fabrication.
Sales: From Pitch to PO
From the first cold call to finally receiving that first purchase order, the July PCB007 Magazine breaks down some critical parts of the sales stack. To up your sales game, read on!
The Hole Truth: Via Integrity in an HDI World
From the drilled hole to registration across multiple sequential lamination cycles, to the quality of your copper plating, via reliability in an HDI world is becoming an ever-greater challenge. This month we look at “The Hole Truth,” from creating the “perfect” via to how you can assure via quality and reliability, the first time, every time.
- Articles
- Columns
- Links
- Media kit
||| MENU - pcb007 Magazine
Estimated reading time: 3 minutes
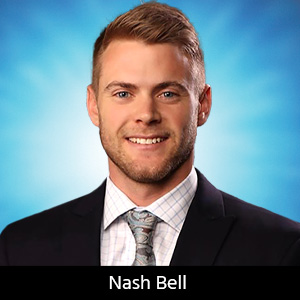
Knocking Down the Bone Pile: Eliminating Solder Balls in Hand Soldering
Cause of the Problem
While solder balls can be produced during both SMT reflow and wave soldering, PCB hand soldering during touch-up or rework can result in solder ball formation. When moisture or other impurities entrapped in or on the surface of the PCB or component outgas during the hand soldering process, solder balls form. Baking out or cleaning the PCB or the component and comparing the results can help determine if this is the case. Soldering irons used to reflow solder paste during rework may also heat the paste too quickly and prevent the flux from fully activating, which causes the solder to oxidize and form solder balls.
Solutions to the Problem
Solder balls form when the flux becomes molten and fails to clean all the soldering surfaces, which prevents the solder from coalescing into a single mass. The oxide coating that forms around smaller solder balls inhibits the solder from coming back together. Turning down the temperature of the soldering tip or using a lower tip temperature cartridge may solve the problem.
Because the soldering tip can only activate so much of the flux in each amount of time, slowing down the wire solder feed rate (Figure 2) or reducing the amount of solder being fed to create the solder joint (Figure 3) can also help prevent solder balls from forming. Fully activating the flux is the key to preventing oxide layers from forming.
Utilizing a slightly more active flux that can withstand this temperature ramp is another option for preventing oxide layer formation. Using a hot air or IR reflow source with a slower defined ramp rate can eliminate the solder balling problem when using paste for rework. A slower ramp rate ensures that the flux is fully activated, thus preventing solder balls from forming.
Soldering techs need to be adequately trained in hand soldering and the variables affecting outcomes to reduce the chances of solder ball formation. Training should include adequately reinforcing the correct materials, choosing the correct tip as a heat bridge between the lead and the land, maintaining the correct tip temperature, and keeping the soldering tips clean. Inexperienced soldering technicians may feed in too much solder too quickly (See Figure 1).
Another area to consider when assessing the likelihood of solder contamination is component lead contamination. Potential sources of contamination include improper storage of the components, improper MSD controls of the component, and the cleanliness of the tape, tray, or stick the components are stored in.
With the proper solder training, or in some cases retraining, soldering technicians can pick up better habits and help diagnose problems as they happen.
Reminder of the IPC-A-610 Spec on Solder Balls
A refresher is in order on what the inspection standard says about solder balls. Solder balls (IPC-A-610H 5.2.7.1) become a defect when:
- The presence of a solder ball reduces the distance between the solder ball and another conductive surface to below the minimum electric clearance.
- The solder ball is not entrapped, encapsulated, or attached, or can become dislodged in the service environment. A solder ball rolling around in an electronics enclosure is not acceptable.
- The solder ball is entrapped in coating or flux residue such that other form, fit, or functions of the electronics assembly cannot be maintained.
Removing Solder Balls
Solder balls can be removed by several means. For solder balls entrapped in flux residue, an orangewood or plastic stick can dislodge the solder balls. The challenge is making sure that solder balls dislodged in this manner do not get "lost" in the assembly and create a future reliability issue. Large solder balls can be removed with a soldering iron, flux, and soldering braid. If entrapped by a conformal coating or other material layer, the coating will need to be removed prior to eliminating the solder balls.
While solder balls typically appear in other PCB assembly processes, those formed in hand soldering can be mitigated through a variety of methods including proper flux usage; proper soldering tip and temperature selection; and by keeping the materials in the soldering process free from moisture and contaminants.
This column originally appeared in the December 2022 issue of SMT007 Magazine.
More Columns from Knocking Down the Bone Pile
Knocking Down the Bone Pile: Addressing End-of-life Component Solderability Issues, Part 4Knocking Down the Bone Pile: Tin Whisker Mitigation in Aerospace Applications, Part 3
Knocking Down the Bone Pile: Gold Mitigation for Class 2 Electronics
Knocking Down the Bone Pile: Basics of Component Lead Tinning
Knocking Down the Bone Pile: Package on Package Rework—Skill Required
Knocking Down the Bone Pile: 2023’s Top Challenges in BGA Rework
Knocking Down the Bone Pile: Opening a Trace on the Surface of a PCB
Knocking Down the Bone Pile: Soldering for QFPs and Other Gull Wing Leaded Parts