-
- News
- Books
Featured Books
- pcb007 Magazine
Latest Issues
Current IssueInventing the Future with SEL
Two years after launching its state-of-the-art PCB facility, SEL shares lessons in vision, execution, and innovation, plus insights from industry icons and technology leaders shaping the future of PCB fabrication.
Sales: From Pitch to PO
From the first cold call to finally receiving that first purchase order, the July PCB007 Magazine breaks down some critical parts of the sales stack. To up your sales game, read on!
The Hole Truth: Via Integrity in an HDI World
From the drilled hole to registration across multiple sequential lamination cycles, to the quality of your copper plating, via reliability in an HDI world is becoming an ever-greater challenge. This month we look at “The Hole Truth,” from creating the “perfect” via to how you can assure via quality and reliability, the first time, every time.
- Articles
- Columns
- Links
- Media kit
||| MENU - pcb007 Magazine
Estimated reading time: 5 minutes
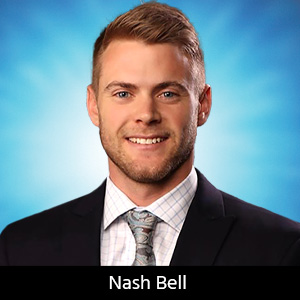
Knocking Down the Bone Pile: 2023’s Top Challenges in BGA Rework
Over seven years ago, I put pen to paper to enumerate the top challenges needing to be overcome for a successful BGA rework. With the continued advancement of BGA technology, it’s time to apply a fresh coat of paint to that list. Read on to find out my revised take on today’s top BGA rework challenges (in no particular order).
Challenge #1: Very Large BGAs
As devices become more complex and computing power requirements increase, the maximum physical size of BGA packages has continued to increase. Currently, some devices in development are planned to be 125 mm x 125 mm in size. These large package sizes present some very challenging scenarios for rework process technicians.
Today, the placement systems for such large packages are limited by the split vision prism systems that align the components during placement. To successfully handle such large packages, BGA rework equipment vision systems will need to be upgraded.
Bottom heaters, which ensure that the board onto which the package is placed is uniformly heated, need to be upgraded to handle these large component package sizes. Undersized underside heating sources may cause an inconsistent temperature gradient from the top of the component to the underlying area, thereby sending different areas of the component into reflow at different times. This results in component balls that are stretched or elongated; “cold peels” due to improper temperature profiles can also damage BGA pads on the board.
Maintaining a consistent temperature over the entire component surface area presents another challenge in reworking these large packages. Air flow turbulence in the hot air rework nozzles can make it difficult to maintain a consistent reflow temperature coming out of the nozzle, which limits its ability to uniformly reflow and remove these large packages. Similarly, many commercially available IR rework systems do not have a spot size which can cover the entire size of these packages heat the component uniformly.
Custom-machined board supports for these larger packages, stay-in-place stencils to open the process window through solder paste printing, and a thorough understanding of proper thermal profiling can all be used to allow older machines to accommodate these larger packages—albeit only to a certain extent.
Challenge #2: Neighboring Device Damage
Components in and around the rework area can be damaged during the rework process, as the heat sources typically used—both IR and hot air—can thermally damage neighboring components. Nearby components such as aluminum, tantalum and ceramic capacitors, crystals, oscillators, plastic-bodied components, and others need to be properly thermally shielded. LEDs and cameras can also be damaged at reflow temperatures.
Not only can these neighboring components be damaged when exposed to heat, they can also be sent into reflow if heating areas and temperature cycles are improperly controlled. This can cause heavier components to fall off the underside of the PCB during BGA rework. Furthermore, when solder is reflowed, the intermetallic formed in the solder fillet can grow, causing the component to form a weaker mechanical bond to the PCB.
With the use of the proper thermal shielding materials, these problems can be avoided1. Newer materials are now available to help protect components from both damage and reaching reflow temperatures. Thermal shielding materials such as water-absorbing cool gels, as well as ceramic non-wovens, are the most effective thermal shields.
Challenge #3: Underfilled BGA Rework
Underfill has made its way into a variety of industries, including automotive, military, and aerospace applications. Underfill boosts the reliability of the component, which is subject to mechanical impacts and shocks by distributing the forces. Thermal stresses caused by the coefficient of thermal expansion mismatch between the component and the PCB are also
lessened by using underfill. However, the proliferation of underfills has increased the need for solutions to underfill component rework. With underfill usage expected to grow over 5% per year through the next five years, finding appropriate solutions for underfill component rework issues will remain challenging2.
BGA rework locations neighboring the same or opposite side of the PCB can be damaged during the rework process. Since the underfill softens before reaching the solder’s liquidus temperature, underfills near the rework location can “push out” solder from its desired location, thereby creating soldering anomalies such as shorts or other soldering defects.
Another major rework challenge is breaking the BGA free from the underfill during the component removal process. During reflow, the tack of the underfill holds the BGA tightly to the PCB. Removing the BGA requires the rework technician to either “cut through” the underfill using a knife or to use specially designed nozzles to pull the BGA off the board. Either of these operations can result in damage to the PCB pads or solder mask. Once the BGA has been removed, this underfill material, as well as the remnant solder, needs to be manually cleaned from the board. This labor-intensive process is necessary to ensure that the site is adequately cleaned prior to replacement of the BGA.
Newer methods such as cold removal using a highly controlled milling process or laser ablation of the component can overcome some of these rework challenges. These advanced methods, while faster and repeatable, require both capital and higher-end programming and processing skills on the part of the rework supplier.
Challenge #4: Mirrored BGAs
When BGAs are placed “back-to-back” directly opposite one another on both sides of a double-sided PCB, the configuration is known as “mirroring” (Figure 2). This is a continuing challenge in BGA rework as board densities increase. In BGA rework, it is necessary to preheat the PCB from the opposite side of where the BGA is to be removed and replaced. This necessitates heating the BGA underneath the rework location causing the underside BGA to be exposed to a minimum of 125°C. In addition, this causes the underside BGA to be exposed to a longer duration heat cycle, which increases the potential for damaging or warping the BGA. It may also cause the underside component to go into reflow resulting in soldering anomalies and solder joint embrittlement. Another danger is the potential for larger more massive BGA components to “fall off” the oppositely located BGAs as the surface tension may no longer be able to overcome gravity, which is pulling down on the component.
Summary
The challenges for BGA rework will continue to evolve. Large BGA packages, BGAs in close proximity to neighboring devices, underfilled BGAs, and mirrored BGAs currently present the greatest challenges in BGA rework today.
References
- “Shielding Effectiveness of Polyimide Tape During Rework,” by Adam Gaynor and Bob Wettermann, Circuits Assembly Magazine, Oct. 1, 2014.
- “Electronic Board Level Underfill Material Market,” by Future Market Insights Global Consulting, 2022.
This column originally appeared in the February 2023 issue of SMT007 Magazine.
More Columns from Knocking Down the Bone Pile
Knocking Down the Bone Pile: Addressing End-of-life Component Solderability Issues, Part 4Knocking Down the Bone Pile: Tin Whisker Mitigation in Aerospace Applications, Part 3
Knocking Down the Bone Pile: Gold Mitigation for Class 2 Electronics
Knocking Down the Bone Pile: Basics of Component Lead Tinning
Knocking Down the Bone Pile: Package on Package Rework—Skill Required
Knocking Down the Bone Pile: Eliminating Solder Balls in Hand Soldering
Knocking Down the Bone Pile: Opening a Trace on the Surface of a PCB
Knocking Down the Bone Pile: Soldering for QFPs and Other Gull Wing Leaded Parts