-
- News
- Books
Featured Books
- pcb007 Magazine
Latest Issues
Current IssueSales: From Pitch to PO
From the first cold call to finally receiving that first purchase order, the July PCB007 Magazine breaks down some critical parts of the sales stack. To up your sales game, read on!
The Hole Truth: Via Integrity in an HDI World
From the drilled hole to registration across multiple sequential lamination cycles, to the quality of your copper plating, via reliability in an HDI world is becoming an ever-greater challenge. This month we look at “The Hole Truth,” from creating the “perfect” via to how you can assure via quality and reliability, the first time, every time.
In Pursuit of Perfection: Defect Reduction
For bare PCB board fabrication, defect reduction is a critical aspect of a company's bottom line profitability. In this issue, we examine how imaging, etching, and plating processes can provide information and insight into reducing defects and increasing yields.
- Articles
- Columns
- Links
- Media kit
||| MENU - pcb007 Magazine
Estimated reading time: 4 minutes
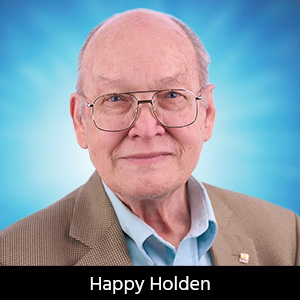
Contact Columnist Form
Happy’s Tech Talk #16: Protocols for a Smart Factory Future
Introduction
Karl Dietz never wrote on automation and the Smart factory, but these topics have been a priority for larger OEMs since the early 1980s. I became involved in automation planning after designing and building Hewlett-Packard’s printed circuit fabrication facility in Sunnyvale, California. This was the first fabrication facility to demonstrate the capability of computer process control and management planning. Soon after, I moved into the role of automation consultant for HP with its introduction of the Manufacturing Productivity Network (MPN) for a product line of computers, software, and data acquisition systems.
Starting the Process
The journey to a Smart factory is evolutionary; it starts with a thorough business plan that charts a roadmap for your enterprise into the future. That roadmap will have six stages (Figure 1):
- Environmental assessment
- Program strategy
- Conceptual design
- Detailed design and requirement specifications
- Development
- Implementation
Mechanization was the primary focus of automation in the 1980s and ‘90s, with an emphasis on robotics and continuous product flow. The focus of Industry 4.0 has been on sensors, data collection, data aggregation, data analysis/analytics, business intelligence/corrective actions, and predictions (digital twins) or systemization. As seen in Figure 2, the emphasis is now on analytics and optimizations in all forms.
Smart Factory Protocols
When considering automation and data in the electronics manufacturing factory, three protocols stand out as de facto standards (Figure 3):
- PLC protocols
- IPC-CFX
- SEMI SECS/GEM
PLC Protocols
Programmable logic controllers (PLC) came about in the 1960s and have steadily grown in use and popularity.
PLCs, like those produced by Siemens and Allen Bradley, have extensive networking capabilities. There are at least six to eight open, but proprietary, messaging and protocols used by PLCs, with the ModBus TCP being the most popular and largest installed base. These are used in automation protocols as seen in Figure 3.
Four of the most popular protocols for PLCs are:
- ModBus TCP
- Profinet
- OPC-UA
- MAPS
IPC-CFX/HERMES
For electronics assembly, over 300 corporate IPC members came together to create the connected Factory Exchange (CFX) in 2018. The IPC-2591 is an open-source standard for “plug-and-play” connectivity for electronics assembly.
It establishes three critical elements for plug-and-play industrial IoT:
- A message protocol using AMQP.
- An encoding mechanism using JSON.
- A specific content creation element-structured topics and messages.
These elements allow for the creation of automatic decision making, dashboard displays, alerts, and reports. Applications that improve productivity, efficiency, capacity planning, and quality while lowering costs can be seen in Figure 5. It allows the full traceability of components (IPC-1782) and feedback to design (IPC-2581).
Typical CFX topics and messages are shown in Figure 6. IPC has established the “CFX Message Submission Process,” a methodology to add/edit new messages for the CFX standard, which allows the standard to grow and be applied by more machines and processes. There is even CFX messaging for hand soldering.
To facilitate adapting machines and applications, there are free software development kits (SDK) available for Windows, .Net, Linux, LabVIEW, JAVA, etc. Already, hundreds of machines have been adapted and demonstrated with native CFX. Figure 6 is an overview of the CFX SDK life cycle. The goal of the IPC committee is to facilitate a fully functioning Industry 4.0 Digital Manufacturing World.
Example (Figure 6)
The IPC-CFX standard allows inspection data (2) and (3) from devices to be uploaded to MEM software where compensation data (2) and correction data (2) are determined and downloaded to the screen printer and pick-and-place machines to improve quality and reduce downtime.
SEMI-SECS/GEM
The third standard protocol is SEMI’s SECS/GEM standard. This standard was established in the 1980s and ‘90s by the semiconductor industry (SEMI) and has been continuously updated. There are over 900 English SEMI standards, with many more in Korean, Japanese, and Chinese. SEMI also has standards for other industries, including photovoltaic and liquid crystal display fabrication. The standards are open and non-proprietary. SEMI’s documentation is useful to establish messages and responses for PCB fabrication protocols. Like IC fabrication, the PCB fabrication process is thermodynamic, so the IC fabrication model is very useful for PCB fab and is different from the kinematic PCB assembly model. It has been updated with current wireless networking and security and is a convenient model for additional PCB automation. The PCB fabrication standards are under development by the Taiwan Printed Circuit Association (TPCA); its model is shown in Figure 7.
SEMI has PCB fabrication and assembly advisory boards working to connect the entire electronics supply chain into one digital thread. Because of accessibility, originality, and security, SEMI is looking at “distributed ledger technologies” (blockchain) as a possible technology to include in its General Equipment Model (GEM-E30) protocol. Find the SEMI standards on its website6.
Conclusion
The automation planning methodology is detailed in Automation and Advanced Procedures in PCB Fabrication1. By breaking down all work into time spent by a worker and by the machines for mechanization and systemization at various levels and classes, a plan can easily be prepared for new performance stages. The material handling of products from operation to operation (Figure 8) is benchmarked, as well as the networking of information.
References
- Automation and Advanced Procedures in PCB Fabrication, by Happy Holden, June 2018.
- “Building An AI Ready Culture,” keynote address by Irene Petrick, SMTA eSmart Factory Conference, Detroit, 2019.
- “IPC CFX: Plug and Play Equipment Messaging Supporting the Factory of the Future,” IPC.org, 2022.
- “The Smart Factory Program,” at IPC APEX EXPO in San Diego, CA, 2022.
- “SEMI SECS/GEM Presentation,” translated from Chinese at the TPCA Conference in Taipei, Taiwan, November 2021.
- SEMI website, www1.semi.org/standards.
Happy Holden has worked in printed circuit technology since 1970 with Hewlett-Packard, NanYa Westwood, Merix, Foxconn, and Gentex. He is currently a contributing technical editor with I-Connect007, and the author of Automation and Advanced Procedures in PCB Fabrication, and 24 Essential Skills for Engineers.
This column originally appeared in the January 2023 issue of PCB007 Magazine.
More Columns from Happy’s Tech Talk
Happy’s Tech Talk #40: Factors in PTH Reliability—Hole VoidsHappy’s Tech Talk #39: PCBs Replace Motor Windings
Happy’s Tech Talk #38: Novel Metallization for UHDI
Happy’s Tech Talk #37: New Ultra HDI Materials
Happy’s Tech Talk #36: The LEGO Principle of Optical Assembly
Happy’s Tech Talk #35: Yields March to Design Rules
Happy’s Tech Talk #34: Producibility and Other Pseudo-metrics
Happy’s Tech Talk #33: Wet Process Management and Control