Advanced Packaging Means Advanced Routing Issues
January 26, 2023 | Kris Moyer, IPCEstimated reading time: 1 minute
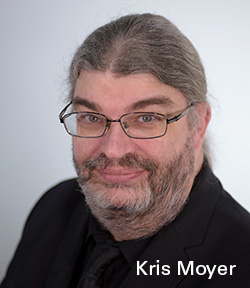
In today’s ever-shrinking world of electronics designs, the use of BGA parts with very fine pitch features is becoming more prevalent. As these fine-pitch BGAs continue to increase in complexity and user I/O (number of balls), the difficulty of finding escape routes and fan-out patterns increases. Additionally, with the shrinking of silicon geometry leading to both smaller channel length and increased signal integrity issues, some of the traditional BGA escape routing techniques will require a revisit and/or adjustment to allow for not only successful fan-out, but also successful functioning of the circuitry of the BGA design.
Historically, BGAs could be routed using traditional full through-via structures, with dog-bone traces off the BGA pad. These BGAs were typically 1.27 mm in pitch and had sufficient clearance between the pads to place a Class 3 Level A via without violating any design rules. Additionally, the feature sizes of these packages were sufficient to fabricate in 1-ounce copper without any issues. With increases in chip complexity and I/O density, most BGA packages are now 1 mm or smaller pitch, with some packages as small as 0.4 mm pitch. With these finer pitch packages, it is no longer possible to use traditional full-thru via structures under the BGA. This, in turn, will require the use of sequential lamination and micro-via structures in order to successfully escape route the BGA. Figure 1 shows a comparison between the package and feature sizes of 484-ball 1 mm pitch BGA (U100) and a 100-ball 0.4 mm pitch BGA (U101).
First, we look at the 1 mm pitch part, then evaluate what it will take to escape all balls to the outside perimeter of the BGA. For this evaluation, we will only consider the use of stacked microvias. Staggered microvias will also work, but require significantly more board area. Additionally, the stackup will assume dual stripline for all internal signal layers.
To read this entire article, which appeared in the January 2023 issue of Design007 Magazine, click here.
Suggested Items
I-Connect007 Editor’s Choice: Five Must-Reads for the Week
07/18/2025 | Nolan Johnson, I-Connect007It may be the middle of the summer, but the news doesn’t quit, and there’s plenty to talk about this week, whether you’re talking technical or on a global scale. When I have to choose six items instead of my regular five, you know it’s good. I start by highlighting my interview with Martyn Gaudion on his latest book, share some concerning tariff news, follow that up with some promising (and not-so-promising) investments, and feature a paper from last January’s inaugural Pan-European Design Conference.
Elephantech Launches World’s Smallest-Class Copper Nanofiller
07/17/2025 | ElephantechJapanese deep-tech startup Elephantech has launched its cutting-edge 15 nm class copper nanofiller – the smallest class available globally. This breakthrough makes Elephantech one of the first companies in the world to provide such advanced material for commercial use.
Copper Price Surge Raises Alarms for Electronics
07/15/2025 | Global Electronics Association Advocacy and Government Relations TeamThe copper market is experiencing major turbulence in the wake of U.S. President Donald Trump’s announcement of a 50% tariff on imported copper effective Aug. 1. Recent news reports, including from the New York Times, sent U.S. copper futures soaring to record highs, climbing nearly 13% in a single day as manufacturers braced for supply shocks and surging costs.
I-Connect007 Editor’s Choice: Five Must-Reads for the Week
07/11/2025 | Andy Shaughnessy, Design007 MagazineThis week, we have quite a variety of news items and articles for you. News continues to stream out of Washington, D.C., with tariffs rearing their controversial head again. Because these tariffs are targeted at overseas copper manufacturers, this news has a direct effect on our industry.I-Connect007 Editor’s Choice: Five Must-Reads for the Week
Digital Twin Concept in Copper Electroplating Process Performance
07/11/2025 | Aga Franczak, Robrecht Belis, Elsyca N.V.PCB manufacturing involves transforming a design into a physical board while meeting specific requirements. Understanding these design specifications is crucial, as they directly impact the PCB's fabrication process, performance, and yield rate. One key design specification is copper thieving—the addition of “dummy” pads across the surface that are plated along with the features designed on the outer layers. The purpose of the process is to provide a uniform distribution of copper across the outer layers to make the plating current density and plating in the holes more uniform.