Digital Twin Concept in Copper Electroplating Process Performance
July 11, 2025 | Aga Franczak, Robrecht Belis, Elsyca N.V.Estimated reading time: 1 minute
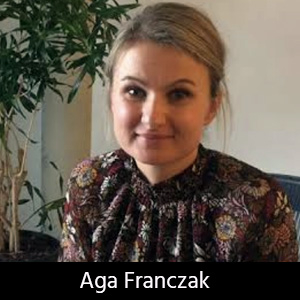
Editor’s Note: This is an excerpt from a technical paper presented at the inaugural Pan European Design Conference in January 2025. It is reflected as originally presented with minor edits for grammar. There is a link to access the full paper at the conclusion of this excerpt.
Abstract
PCB manufacturing involves transforming a design into a physical board while meeting specific requirements. Understanding these design specifications is crucial, as they directly impact the PCB's fabrication process, performance, and yield rate. One key design specification is copper thieving—the addition of “dummy” pads across the surface that are plated along with the features designed on the outer layers. The purpose of the process is to provide a uniform distribution of copper across the outer layers to make the plating current density and plating in the holes more uniform.
Copper electroplating is crucial in PCB manufacturing, primarily because it reduces ground line impedance and voltage drop. The performance of the electroplating process directly affects the quality of the copper layer and related mechanical properties. In acid copper plating, achieving proper thickness distribution and surface uniformity without compromising metallurgical properties like elongation and tensile strength is challenging. Lowering the current density can help equalize copper thickness but significantly increases plating time, adversely affecting PCB throughput.
Therefore, controlling process performance and the quality of the electroplated copper layer are vital aspects of PCB plating, which remains challenging even for experienced PCB manufacturers. Recognizing plating process performance in terms of copper layer coverage and thickness up front adds significant value to process design and control. This paper explores the concept of automated copper thieving and the digital twin of the copper plating process in PCB manufacturing. These modern CAE tools facilitate the rapid assessment and mitigation of copper under- and over-plated surface areas, aligning closely with the principles of smart manufacturing.
To read the entire paper, which appeared in the June 2025 issue of PCB007 Magazine, click here.
Testimonial
"The I-Connect007 team is outstanding—kind, responsive, and a true marketing partner. Their design team created fresh, eye-catching ads, and their editorial support polished our content to let our brand shine. Thank you all! "
Sweeney Ng - CEE PCBSuggested Items
How Good Design Enables Sustainable PCBs
08/21/2025 | Gerry Partida, Summit InterconnectSustainability has become a key focus for PCB companies seeking to reduce waste, conserve energy, and optimize resources. While many discussions on sustainability center around materials or energy-efficient processes, PCB design is an often overlooked factor that lies at the heart of manufacturing. Good design practices, especially those based on established IPC standards, play a central role in enabling sustainable PCB production. By ensuring designs are manufacturable and reliable, engineers can significantly reduce the environmental impact of their products.
50% Copper Tariffs, 100% Chip Uncertainty, and a Truce
08/19/2025 | Andy Shaughnessy, I-Connect007If you’re like me, tariffs were not on your radar screen until a few months ago, but now political rhetoric has turned to presidential action. Tariffs are front-page news with major developments coming directly from the Oval Office. These are not typical times. President Donald Trump campaigned on tariff reform, and he’s now busy revamping America’s tariff policy.
Global PCB Connections: Understanding the General Fabrication Process—A Designer’s Hidden Advantage
08/14/2025 | Markus Voeltz -- Column: Global PCB ConnectionsDesigners don’t need to become fabricators, but understanding the basics of PCB fabrication can save you time, money, and frustration. The more you understand what’s happening on the shop floor, the better you’ll be able to prevent downstream issues. As you move into more advanced designs like HDI, flex circuits, stacked vias, and embedded components, this foundational knowledge becomes even more critical. Remember: the fabricator is your partner.
MKS’ Atotech to Participate in IPCA Electronics Expo 2025
08/11/2025 | AtotechMKS Inc., a global provider of enabling technologies that transform our world, announced that its strategic brands ESI® (laser systems) and Atotech® (process chemicals, equipment, software, and services) will showcase their latest range of leading manufacturing solutions for printed circuit board (PCB) and package substrate manufacturing at the upcoming 17th IPCA Show to be held at Pragati Maidan, New Delhi from August 21-23, 2025.
MKS Showcases Next-generation PCB Manufacturing Solutions at the Thailand Electronics Circuit Asia 2025
08/06/2025 | MKS Instruments, Inc.MKS Inc, a global provider of enabling technologies that transform our world, today announced its participation in Thailand Electronics Circuit Asia 2025 (THECA 2025), taking place August 20–22 at BITEC in Bangkok.