MacDermid Alpha Presents on the Future of Semiconductor Solutions at IMAPS 2023
March 6, 2023 | MacDermid Alpha Electronics SolutionsEstimated reading time: 2 minutes
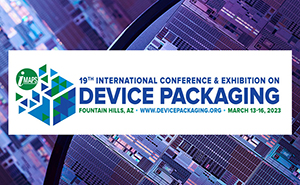
MacDermid Alpha, one of the world’s largest providers of solutions for circuitry, assembly, and semiconductor manufacturers within the electronics industry will present its latest research on high-speed copper plating at the 19th Annual Device Packaging Conference (DPC 2023), held March 13-16, at the We-Ko-Pa Conference Center in Fountain Hills, Arizona. Engage the industry experts at booth 31-32, where MacDermid Alpha will showcase the performance benefits of advanced materials for die attach, chip fabrication, and wafer-level packaging.
Sean Fleuriel, Research Chemist, will present a paper at the technical conference, titled “High-Speed Copper Plating Process for IC Substrate”. In this paper, Sean presents findings from an acid copper electrolyte utilized for plating 2-in-1 redistribution layers (RDL), with small vias and fine lines down to 10µm wide. The electrolytic process successfully plated these features, while maintaining a uniform surface across the panel that met the demanding physical requirements for IC substrate applications. Sean will explore the new high-speed findings in greater detail, revealing new degrees of control unavailable in VCPs, and cover the benefits of the high-speed tool to reduce plating time.
MacDermid Alpha is powering the future of advanced semiconductor solutions that exceed demanding packaging design requirements and help overcome the challenges of miniaturization thereby enabling greater device reliability. Highlighted at the show will be:
- Systek®, MacDermid Alpha’s family of high-performance build-up processes for IC Substrates and their integrated leadframe package portfolio which spans the entire process of building QFN packages from leadframe roughening and improving sidewall solderability for enhanced reliability to selective EMC plating for higher functionality.
- NOVAFAB® NANOTWIN Cu is a ready-to-use, high-purity copper electroplating process designed for use with soluble or insoluble anodes. This system enables low-temperature, high-reliability copper-to-copper interconnects for die-to-die (D2D), die-to-wafer (D2W), and wafer-to-wafer (W2W) bonding.
Additionally, for solutions designed for the challenges of power electronics, MacDermid Alpha will share information on the latest capabilities of the ALPHA® ARGOMAX® portfolio of sinter materials and ATROX® conductive and non-conductive die attach pastes and films will be available. ALPHA® ARGOMAX® engineered sinter materials are proven to have the best process times and reliability while providing flexible and easy-to-use form factors that reduce the capital cost and time to market. ATROX® conductive die attach products are an enabler for package shrinkage and higher power density packaging, designed for excellent workability and processing, and offer proven performance across a range of exposed pad power packages.
Let’s start a conversation at booth 31-32; the team from MacDermid Alpha will be ready to discuss how to elevate your process with an integrated ‘start to finish’ roadmap featuring some of the most advanced technologies on the market, backed by extensive R&D facilities, a robust supply chain, and extraordinary customer service. Established brands aligned under MacDermid Alpha Electronics Solutions include Alpha®, Compugraphics, Electrolube®, Kester®, and MacDermid Enthone®. MacDermid Alpha will resolve your pain points today, tomorrow, and beyond. Discover how we make a difference by visiting www.macdermidalpha.com.
Testimonial
"Our marketing partnership with I-Connect007 is already delivering. Just a day after our press release went live, we received a direct inquiry about our updated products!"
Rachael Temple - AlltematedSuggested Items
Statement from the Global Electronics Association on the July 2025 Tariff on Copper Foil and Electronics-Grade Copper Inputs
07/31/2025 | Global Electronics AssociationWe are disappointed by today’s decision to impose a 50% tariff on imported copper foil and other essential materials critical to electronics manufacturing in the United States.
Trouble in Your Tank: Metallizing Flexible Circuit Materials—Mitigating Deposit Stress
08/04/2025 | Michael Carano -- Column: Trouble in Your TankMetallizing materials, such as polyimide used for flexible circuitry and high-reliability multilayer printed wiring boards, provide a significant challenge for process engineers. Conventional electroless copper systems often require pre-treatments with hazardous chemicals or have a small process window to achieve uniform coverage without blistering. It all boils down to enhancing the adhesion of the thin film of electroless copper to these smooth surfaces.
Considering the Future of Impending Copper Tariffs
07/30/2025 | I-Connect007 Editorial TeamThe Global Electronics Association is alerting industry members that a potential 50% tariff on copper could hit U.S. electronics manufacturers where it hurts.
Connect the Dots: Sequential Lamination in HDI PCB Manufacturing
07/31/2025 | Matt Stevenson -- Column: Connect the DotsAs HDI technology becomes mainstream in high-speed and miniaturized electronics, understanding the PCB manufacturing process can help PCB design engineers create successful, cost-effective designs using advanced technologies. Designs that incorporate blind and buried vias, boards with space constraints, sensitive signal integrity requirements, or internal heat dissipation concerns are often candidates for HDI technology and usually require sequential lamination to satisfy the requirements.
OKI Launches Rigid-Flex PCBs with Embedded Copper Coins Featuring Improved Heat Dissipation for Space Equipment Applications
07/29/2025 | BUSINESS WIREOKI Circuit Technology, the OKI Group’s printed circuit board (PCB) business company, has developed rigid-flex PCBs with embedded copper coins that offer improved heat dissipation for use in rockets and satellite-mounted equipment operating in vacuum environments.