DFM 101: Final Finishes—OSP
March 9, 2023 | Anaya Vardya, American Standard CircuitsEstimated reading time: 1 minute
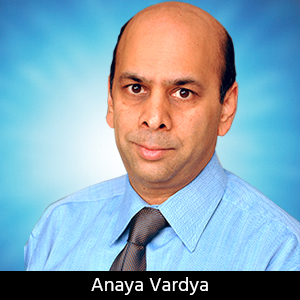
Introduction
One of the biggest challenges facing PCB designers is not understanding the cost drivers in the PCB manufacturing process. The next final finishes to discuss in this series is OSP. As with all surface finishes there are pros and cons with the decision of which to use. It is a combination of application, cost, and the properties of the finish. OSP is RoHS-compliant as there is zero lead content in the finish.
Final Finishes
OSP (Organic Solderability Preservative)
OSP is a thin organic coating, typically 5.9 to 11.8 µin [0.15 to 0.30 µm] thick, designed to prevent the oxidation of copper to maintain solderability over an extended period. Compared with other surface finish technologies, OSP is somewhat different. It uses a chemical process to produce an organic film on the bare copper surface which acts as a barrier to copper oxidation. OSP is organic, not metallic, and its cost is lower than most surface treatment technologies.
As with all surface finishes, the primary purpose is to protect the solderable surfaces on the PCB from oxidation and to aid in assembly soldering. This process coats a very thin coating of an organic material that inhibits copper oxidation. It is so thin that it is nearly impossible to see and measure. The organic material is removed by the assembly flux. Boards that have been OSP coated will have bright copper pad coloration. OSP is specially designed for mixed metal applications, such as electroless nickel immersion gold (ENIG). The OSP selectively deposits on copper while leaving gold connectors or metallic heat sinks free of contamination.
There are a couple of common OSP finishes widely used in the industry:
ENTEK CU-56: This is used for assemblies that will only go through a single reflow process. This finish is not being utilized much anymore because of the use of mixed technology boards (SMT and through-hole).
ENTEK CU-106A: This is the most prevalent version primarily due to the ability to survive multiple thermal assembly operations. PCBs that have multiple surface finishes can use the CU-106A(X) finish.
To read this entire article, which appeared in the February 2023 issue of Design007 Magazine, click here.
Suggested Items
I-Connect007 Editor’s Choice: Five Must-Reads for the Week
07/11/2025 | Andy Shaughnessy, Design007 MagazineThis week, we have quite a variety of news items and articles for you. News continues to stream out of Washington, D.C., with tariffs rearing their controversial head again. Because these tariffs are targeted at overseas copper manufacturers, this news has a direct effect on our industry.I-Connect007 Editor’s Choice: Five Must-Reads for the Week
Digital Twin Concept in Copper Electroplating Process Performance
07/11/2025 | Aga Franczak, Robrecht Belis, Elsyca N.V.PCB manufacturing involves transforming a design into a physical board while meeting specific requirements. Understanding these design specifications is crucial, as they directly impact the PCB's fabrication process, performance, and yield rate. One key design specification is copper thieving—the addition of “dummy” pads across the surface that are plated along with the features designed on the outer layers. The purpose of the process is to provide a uniform distribution of copper across the outer layers to make the plating current density and plating in the holes more uniform.
Trump Copper Tariffs Spark Concern
07/10/2025 | I-Connect007 Editorial TeamPresident Donald Trump stated on July 8 that he plans to impose a 50% tariff on copper imports, sparking concern in a global industry whose output is critical to electric vehicles, military hardware, semiconductors, and a wide range of consumer goods. According to Yahoo Finance, copper futures climbed over 2% following tariff confirmation.
Happy’s Tech Talk #40: Factors in PTH Reliability—Hole Voids
07/09/2025 | Happy Holden -- Column: Happy’s Tech TalkWhen we consider via reliability, the major contributing factors are typically processing deviations. These can be subtle and not always visible. One particularly insightful column was by Mike Carano, “Causes of Plating Voids, Pre-electroless Copper,” where he outlined some of the possible causes of hole defects for both plated through-hole (PTH) and blind vias.
Trouble in Your Tank: Can You Drill the Perfect Hole?
07/07/2025 | Michael Carano -- Column: Trouble in Your TankIn the movie “Friday Night Lights,” the head football coach (played by Billy Bob Thornton) addresses his high school football team on a hot day in August in West Texas. He asks his players one question: “Can you be perfect?” That is an interesting question, in football and the printed circuit board fabrication world, where being perfect is somewhat elusive. When it comes to mechanical drilling and via formation, can you drill the perfect hole time after time?