-
- News
- Books
Featured Books
- pcb007 Magazine
Latest Issues
Current IssueThe Hole Truth: Via Integrity in an HDI World
From the drilled hole to registration across multiple sequential lamination cycles, to the quality of your copper plating, via reliability in an HDI world is becoming an ever-greater challenge. This month we look at “The Hole Truth,” from creating the “perfect” via to how you can assure via quality and reliability, the first time, every time.
In Pursuit of Perfection: Defect Reduction
For bare PCB board fabrication, defect reduction is a critical aspect of a company's bottom line profitability. In this issue, we examine how imaging, etching, and plating processes can provide information and insight into reducing defects and increasing yields.
Voices of the Industry
We take the pulse of the PCB industry by sharing insights from leading fabricators and suppliers in this month's issue. We've gathered their thoughts on the new U.S. administration, spending, the war in Ukraine, and their most pressing needs. It’s an eye-opening and enlightening look behind the curtain.
- Articles
- Columns
- Links
- Media kit
||| MENU - pcb007 Magazine
Estimated reading time: 8 minutes
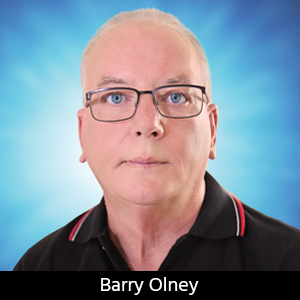
Beyond Design: Containing Electromagnetic Fields in Wireless PCB Design
The path of electromagnetic energy in multilayer PCBs is generally guided by a signal trace bounded by the plane(s). However, as the demand for high-density, high-performance microwave (µWave), and millimeter wave (mmWave) circuits increases in the latest wireless technologies, the electromagnetic fields require more stringent control as they tend to radiate more—particularly on microstrip (surface) layers. Thus, as we enter the realm of µWave (3-30 GHz) and mmWave (30-300 GHz), designers are compelled to implement waveguide techniques, used traditionally in RF design, to reduce radiation loss. At these ultra-high frequencies, the behavior of electromagnetic waves and their interaction with circuit components is significantly different from what is observed at lower frequencies. It requires specialized circuit design techniques and the use of components that are tailored to the specific requirements of RF circuits.
One of the most fundamental steps in the process of gaining proficiency in high-speed digital, and RF design (encompassing µWave/mmWave) is learning to think in the frequency domain. For most of us, the vast majority of our early experience with electrical circuits and signals remains within the context of voltages and currents that are either static or dynamic with respect to time.
An RF circuit is a special type of analog circuit operating at very high frequencies suitable for wireless transmission. One prominent feature of an RF circuit is the use of inductive elements to tune the resonant circuit operation around a specific carrier frequency. In the world of RF design, intentional coupling of electromagnetic fields is also used to create ports between individual circuits.
Typical communication designs incorporate analog, digital, and RF signals on the same substrate, so partitioning is particularly important. In applications where high power is not required, such as a smartphone, Wi-Fi, and Bluetooth, transceiver circuits often take the form of a silicon-based IC, reducing the footprint and simplifying the layout. However, routing all the essential power distribution networks and grounding is always a challenge.
The most effective board stackup for RF design is to have a ground reference plane immediately adjacent to the surface layers and to keep the RF traces on the surface as much as possible. Minimizing vias in the RF path reduces trace inductance, reduces the voids in the ground plane, and gives less opportunity for the electromagnetic energy to escape. Through-board vias should be avoided to prevent unwanted fields from transferring from one side of the board to the other or into the plane cavity. The field, emanating from the vicinity of the signal via, injects a propagating wave into the cavity which can excite the cavity resonances or any other parallel structure. Other signal vias passing through this cavity can pick up this transient energy as crosstalk. The usual technique to prevent this is to use blind microvias from both sides, effectively making two separate back-to-back boards. Digital signals and power can be routed in the internal layers. One can minimize the impact of the essential through-vias by placing them in an area that has no RF signals.
Microstrip transmission lines have been widely used in RF circuit design for decades. However, at high frequencies, microstrip lines can suffer from significant signal loss due to radiation and dielectric losses. Coplanar waveguides (CPWs), on the other hand, offer lower radiation loss and are becoming a popular alternative for high-frequency digital circuits. CPWs consist of a central conductor on the surface layer of the PCB, flanked by two ground planes on either side, and are usually ground referenced, which confines the electromagnetic field and reduces radiation losses (Figure 1).
The CPW offers several advantages over a conventional microstrip transmission line:
- Simplifies fabrication
- Facilitates easy shunt as well as series surface mounting of active and passive devices
- Eliminates the need for via holes and wraparound (ground plating on the edge of a substrate to provide a low inductance path)
- Reduces radiation loss at very high microwave frequencies
The impedance of a CPW is determined by the ratio of trace width to clearance, so size reduction is possible without limit, the only penalty being higher losses. In addition, a virtual ground plane exists between any two adjacent lines, as there is no field at that point. Hence crosstalk effects, between parallel trace segments, are extremely weak. Despite the efforts to evolve and improve the existing transmission line structures, it still remains a technological challenge, which necessitates the emergence of a revolutionary concept.
As digital transmission frequencies head toward 100 GHz and beyond, the current mainstream PCB technology—the copper interconnect—is reaching its performance threshold. Ultimately, dielectric loss, copper roughness, and data transfer capacity are the culprits. However, the biggest performance restriction for PCB interconnects is the size of the conductor. Metallic waveguides, on the other hand, are a better option compared to traditional transmission lines, but they are bulky, expensive, and non-planar in nature. Recently, substrate integrated waveguide (SIW) structures have emerged as a viable alternative and are ideally suited to the high-speed transmission of electromagnetic waves. SIWs are planar structures fabricated using two periodic rows of PTH vias or plated slots connecting adjacent copper ground planes of a dielectric substrate as shown in Figure 2 (left).
Several types of transition from SIWs to microstrip or CPW structures are possible but most are challenging to implement. They can be roughly divided into single-substrate or multilayer substrate applications. Dual-layered SIW transitions to microstrip or CPW structures have been successfully applied. But multilayer SIW circuits often suffer from alignment issues. Z-axis alignment of the multilayer laminate book has always been a major limitation of implementing any broadside-coupled application. However, due to the similarity between the traditional waveguide and microstrip modes, the dual-layer microstrip-to-SIW transition is undoubtedly the simplest to implement.
Figure 3 illustrates the transition from a microstrip transmission line to a SIW. The propagating electromagnetic wave, guided by the microstrip trace, travels through the dielectric between layers 1 and 2 and radiates from the solder mask into the surrounding volume. However, as the wave enters the SIW, it begins to tunnel between the ground planes and as such, the dispersion losses are solely based on the losses of the substrate material. The simulation of the electric field shows how the losses reduce as the electromagnetic wave enters the SIW. Here the field becomes more intense and less distributed, providing clarity of signal and thus higher bandwidth. Obviously, another similar transition back to the microstrip, at the other end to receive the signal, is also required. The downside, of this configuration, is the distortion of the field—limiting bandwidth—at the transition from the microstrip to the SIW.
While it is relatively simple to interface SIW with microstrip lines, in order to exploit connectivity to surface-mount devices, CPW technology is more amenable to integration with leadless monolithic microwave integrated circuits (MMIC). An MMIC is a device that operates at µWave frequencies and typically performs functions such as µWave mixing, power amplification, low-noise amplification, and high-frequency switching. Figure 4 illustrates a back-to-back CPW grounded to SIW structure. Ultra-low loss RT/Duriod 5880 dielectric is used for the core material. The transition performance can be controlled by three main parameters (Lt, Wt and Wedge) which are adjusted to optimize the return loss and insertion loss properties.
The drawback of the coplanar-to-SIW transition is the limitation of bandwidth due to higher-order mode propagation if the via holes are not placed in close vicinity to the CPW slots. Also, if the via pitch is increased while the via hole diameter is unchanged, the electromagnetic field starts to radiate outside the via hole arrays. This gives rise to leakage loss in addition to the dielectric and conductor loss of the waveguide. The energy escaping the SIW channel is shown graphically in Figure 5 where field propagation outside the functional region of the waveguide is observed. Thus, it is imperative to select SIW parameters such that the leakage loss is maintained within an acceptable range. The via pitch length, the hole diameter, and their ratio prove to play a key role in confining the fields in an optimal manner.
Substrate-integrated waveguides are similar to traditional waveguides in terms of their ability to support the propagation of electromagnetic waves with low loss and dispersion. However, SIWs achieve this performance in a planar structure by using a substrate material with a low Dk and a low Df. SIWs can be used in a wide range of µWave applications, such as filters, couplers, power dividers, and antennas. The combination of microstrip, CPW, and SIW technologies provides designers with a high degree of flexibility in the design of complex µWave/mmWave systems. Overall, the design of RF circuits requires specialized knowledge and techniques that are tailored to the unique challenges of high-frequency circuit design.
Key Points
- Wireless technologies require more stringent control of electromagnetic fields as they tend to radiate more—particularly on microstrip (surface) layers.
- An RF circuit is a special type of analog circuit operating at very high frequencies suitable for wireless transmission.
- The most effective board stackup for RF design is to have a ground reference plane immediately adjacent to the surface layers and to keep the RF traces on the surface as much as possible.
- To prevent unwanted coupling, use blind microvias from both sides, effectively making two separate back-to-back boards.
- At high frequencies, microstrip lines can suffer from significant signal loss due to radiation and dielectric losses.
- CPWs offer lower radiation loss and are becoming a popular alternative for high-frequency digital circuits.
- The impedance of a CPW is determined by the ratio of trace width to clearance, so size reduction is possible without limit, the only penalty being higher losses.
- SIW are planar structures fabricated using two periodic rows of PTH vias or plated slots connecting adjacent copper ground planes of a dielectric substrate.
- SIW structures have emerged as a viable alternative to microstrip lines due to their low loss, and are ideally suited to the high-speed transmission of electromagnetic waves.
- Several types of transition from SIWs to microstrip or CPW structures are possible but most are challenging to implement. The dual-layer microstrip-to-SIW transition is undoubtedly the simplest.
- CPW technology is more amenable to integration with leadless monolithic microwave integrated circuits.
References
- Beyond Design columns by Barry Olney: “The Frequency Domain,” “Next Gen PCBs: Substrate Integrated Waveguides,” “Microstrip Coplanar Wave Guides,” “It’s a Material World, Plane Cavity Resonance.”
- “Partitioning for RF Design,” by Andy Kowalewski (RIP, old friend).
- “A Review on Substrate Integrated Waveguide and its Microstrip Interconnect,” by Kumar, Jadhav, Ranade.
- “Transitions from Substrate Integrated Waveguide to Planar Transmission Lines and their Applications to Amplifier Integration,” by Farzaneh Taringou.
- “What is RF Circuit Design? How to Design RF Circuits,” by Synopsys.
This column originally appeared in the April 2023 issue of Design007 Magazine.
More Columns from Beyond Design
Beyond Design: The Metamorphosis of the PCB RouterBeyond Design: Radiation and Interference Coupling
Beyond Design: Key SI Considerations for High-speed PCB Design
Beyond Design: Electro-optical Circuit Boards
Beyond Design: AI-driven Inverse Stackup Optimization
Beyond Design: High-speed Rules of Thumb
Beyond Design: Integrated Circuit to PCB Integration
Beyond Design: Does Current Deliver the Energy in a Circuit?