-
- News
- Books
Featured Books
- pcb007 Magazine
Latest Issues
Current IssueSales: From Pitch to PO
From the first cold call to finally receiving that first purchase order, the July PCB007 Magazine breaks down some critical parts of the sales stack. To up your sales game, read on!
The Hole Truth: Via Integrity in an HDI World
From the drilled hole to registration across multiple sequential lamination cycles, to the quality of your copper plating, via reliability in an HDI world is becoming an ever-greater challenge. This month we look at “The Hole Truth,” from creating the “perfect” via to how you can assure via quality and reliability, the first time, every time.
In Pursuit of Perfection: Defect Reduction
For bare PCB board fabrication, defect reduction is a critical aspect of a company's bottom line profitability. In this issue, we examine how imaging, etching, and plating processes can provide information and insight into reducing defects and increasing yields.
- Articles
- Columns
- Links
- Media kit
||| MENU - pcb007 Magazine
Rogers Corporation to Highlight Next Generation Thin Materials for Millimeter Wave Multilayer Designs at Del Mar 2023
April 19, 2023 | Rogers CorporationEstimated reading time: 3 minutes
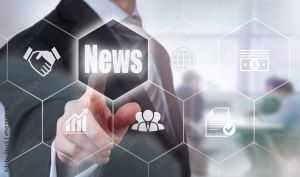
Rogers Corporation will exhibit at the Del Mar Electronics & Manufacturing Show April 26 and 27 at the Del Mar Fairgrounds in San Diego, CA (booth #622). High performance circuit materials used in multilayer structures which include a family of thin laminates and bonding materials are being highlighted along with Radix™ 3D Printable Dielectrics.
Highlighted Products:
Recently introduced Radix™ 3D Printable Dielectrics family of products, is the first available material featuring a dielectric constant of 2.8 and low loss characteristics at microwave frequencies. These printable dielectric materials give radio frequency (RF) designers unprecedented design freedom in creating new components, eliminating the need to consider typical manufacturing design constraints.
Radix3D Printable Dielectrics are proprietary composite materials designed for Digital Light Processing (DLP) 3D printing, enabling a scalable, high-resolution printing process for end-use RF dielectric component manufacturing. Rogers Corporation’s first Radix 3D Printable Dielectric material has a targeted dielectric constant of 2.8 and a dissipation factor of 0.0043 at 10 GHz when cured.
CLTE-MW™ laminates now include lower profile and thinner copper foil options to better serve the needs of designers and PCB fabricators producing millimeter wave PCB circuit designs. The new hyper very low profile (HVLP) ED copper cladding reduces insertion loss of transmission lines operating at 77 GHz by about 20% compared to standard ED copper foil. Additionally, the new HVLP copper cladding option is available in 9 µm, 18 µm and 35 µm thicknesses. These additional copper thickness options provide PCB fabricators more flexibility to achieve tight feature tolerances on signal layers, particularly with sequentially laminated designs.
These laminates are well suited for a range of applications including millimeter wave automotive and industrial radar antennas, 5G millimeter wave base stations and backhaul radios, and phased array radar systems.
SpeedWave® 300P Ultra-Low Loss Prepreg. With the increasing need for stackup flexibility in high layer count designs for 5G mmWave, high resolution 77 GHz automotive radar, aerospace & defense and high speed digital designs, SpeedWave 300P prepreg offers a broad range of competitively priced high performance options for the circuit designer. SpeedWave 300P prepreg can be used to bond a variety of Rogers’ materials including XtremeSpeed™ RO1200™, CLTE-MW™, and RO4000® series laminates.
This prepreg system offers a low dielectric constant of 3.0 – 3.3 and a low dissipation factor of 0.0019 – 0.0022 at 10 GHz with stable performance over a broad frequency range. This material is offered in multiple spread and open weave glass styles and resin content combinations to maximize stackup options.
RO4000® Products for Multilayer Structures:
Next generation products designed to meet the existing and emerging needs of advanced millimeter wave multilayer designs. RO4835T™ laminates, offered in a 2.5 mil, 3 mil and 4 mil core thickness, are 3.3 Dk, low loss, spread glass reinforced, ceramic filled thermoset materials designed for inner-layer use in multilayer board designs, and they complement RO4835™ laminates when thinner cores are needed.
RO4450T™ 3.2-3.3 Dk, low loss, spread glass reinforced, ceramic filled bonding materials were designed to complement RO4835T laminates and the existing RO4000 laminate family, and come in 2.5, 3, 3.5, 4, 4.5, 5 or 6 mil thicknesses.
RO4835T laminates and RO4450T bonding materials exhibit excellent Dk control for repeatable electrical performance, a low z-axis expansion for plated through-hole reliability, and are compatible with standard epoxy/glass (FR-4) processes. These materials are an excellent choice for multilayer designs requiring sequential laminations, as fully cured RO4000 products are capable of withstanding multiple lamination cycles. RO4835T laminates and RO4450T bondplys have the UL 94 V-0 flame retardant rating, and are compatible with lead-free processes.
RO3003G2™ high frequency laminates build on Rogers’ industry-leading RO3003™ platform to provide designers with improved insertion loss and reduced Dk variation. The combination of Rogers’ optimized resin and filler content along with the introduction of hyper very low-profile ED copper (HVLP) translates to Dk of 3.00 @ 10 GHz (clamped stripline method) and 3.07 @ 77 GHz (microstrip differential phase length method). RO3003G2 laminates also show very low insertion loss of 1.3dB/inch for 5 mil laminates as measured by the microstrip differential phase length method.
Testimonial
"We’re proud to call I-Connect007 a trusted partner. Their innovative approach and industry insight made our podcast collaboration a success by connecting us with the right audience and delivering real results."
Julia McCaffrey - NCAB GroupSuggested Items
Statement from the Global Electronics Association on the July 2025 Tariff on Copper Foil and Electronics-Grade Copper Inputs
07/31/2025 | Global Electronics AssociationWe are disappointed by today’s decision to impose a 50% tariff on imported copper foil and other essential materials critical to electronics manufacturing in the United States.
Trouble in Your Tank: Metallizing Flexible Circuit Materials—Mitigating Deposit Stress
08/04/2025 | Michael Carano -- Column: Trouble in Your TankMetallizing materials, such as polyimide used for flexible circuitry and high-reliability multilayer printed wiring boards, provide a significant challenge for process engineers. Conventional electroless copper systems often require pre-treatments with hazardous chemicals or have a small process window to achieve uniform coverage without blistering. It all boils down to enhancing the adhesion of the thin film of electroless copper to these smooth surfaces.
Considering the Future of Impending Copper Tariffs
07/30/2025 | I-Connect007 Editorial TeamThe Global Electronics Association is alerting industry members that a potential 50% tariff on copper could hit U.S. electronics manufacturers where it hurts.
Connect the Dots: Sequential Lamination in HDI PCB Manufacturing
07/31/2025 | Matt Stevenson -- Column: Connect the DotsAs HDI technology becomes mainstream in high-speed and miniaturized electronics, understanding the PCB manufacturing process can help PCB design engineers create successful, cost-effective designs using advanced technologies. Designs that incorporate blind and buried vias, boards with space constraints, sensitive signal integrity requirements, or internal heat dissipation concerns are often candidates for HDI technology and usually require sequential lamination to satisfy the requirements.
OKI Launches Rigid-Flex PCBs with Embedded Copper Coins Featuring Improved Heat Dissipation for Space Equipment Applications
07/29/2025 | BUSINESS WIREOKI Circuit Technology, the OKI Group’s printed circuit board (PCB) business company, has developed rigid-flex PCBs with embedded copper coins that offer improved heat dissipation for use in rockets and satellite-mounted equipment operating in vacuum environments.